Home » Products » E-coating System Accessories » E-coat Tank
e-coat Tank
Flexible and efficient e-coating system.
Electrophoretic tank is the key part of electrophoretic coating system with the following features and functions.
Features:
- Tank material: the electrophoresis tank is usually made of corrosion-resistant materials such as stainless steel or plastic to withstand the chemical reaction between the coating and the workpiece.
- Conductivity: The tank must have a certain degree of conductivity, which is usually realized by coating a conductive layer or adding a conductive agent in the tank body.
- Adjustability: The electrophoresis tank can adjust parameters such as electric field strength, liquid circulation, and temperature to meet different coating requirements.
- Closure: The tank body should have good closure to prevent paint leakage and pollution of the environment.
In a word, the electrophoresis tank plays multiple roles in the process of electrophoresis coating, such as carrying the coating, providing an electric field, controlling parameters, and guaranteeing the quality of coating, which is an important part of realizing high-quality and high-efficiency coating.
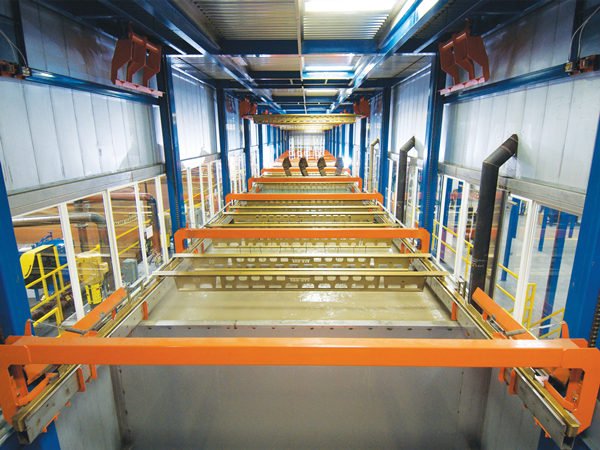

Product Description
In electrophoretic coating, electrophoretic tanks can be categorized according to different classification criteria. The following are the common types of electrophoresis tanks according to different types of classification:
I. Classification according to coating method:
- Unipolar electrophoresis tank: Only one electrode is set up in the unipolar electrophoresis tank, and the paint particles are charged and deposited on the workpiece to form a coating. This type is commonly used for coating large workpieces.
- Bipolar electrophoresis tank: Two electrodes are set up in the bipolar electrophoresis tank, usually one electrode is the anode and one electrode is the cathode so that the paint particles form a coating on the workpiece. This type is widely used for coating small and medium-sized workpieces.
II. Classified according to the way of liquid circulation:
- Static electrophoresis tank: there is no liquid circulation system in the static electrophoresis tank, and the coating is static in the tank, which is usually used for small and fine coating or special process requirements.
- Dynamic electrophoresis tank: Dynamic electrophoresis tank has a liquid circulation system, and the paint is circulated and supplied to the workpiece by a pump to keep the uniformity and stability of the paint. This type is suitable for high-volume coating.
These are the common types of electrophoresis tanks, each type has its applicable scenarios and characteristics. Factors such as the size and shape of the workpiece and the nature of the paint during the coating process will affect the selection of electrophoresis tanks.
III. Action:
- Providing electric field: the electrophoresis tank provides an electric field through the built-in electrode system so that the charged paint particles are uniformly distributed in the tank and move toward the surface of the workpiece.
- Paint storage and circulation: The electrophoresis tank stores the paint solution and continuously conveys the paint to the surface of the workpiece through a circulation pump to ensure the stability and uniformity of the paint.
- Filtering and removing impurities: The tank is permanently equipped with a screen or filtering system for removing impurities suspended in the coating to ensure the quality of the coating.
- Controlling coating thickness: By adjusting the electric field strength and coating concentration, the thickness of the coating can be controlled to meet different requirements.
- Provide cooling: A cooling system is usually provided in the electrophoresis tank to control the temperature of the surface of the workpiece during the coating process to avoid overheating which may lead to degradation of the coating quality.
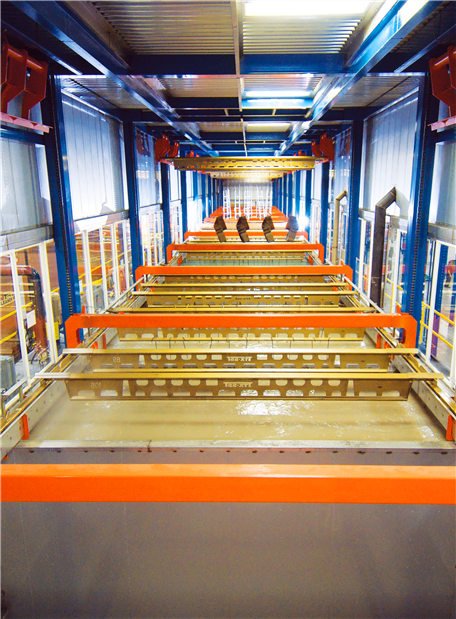
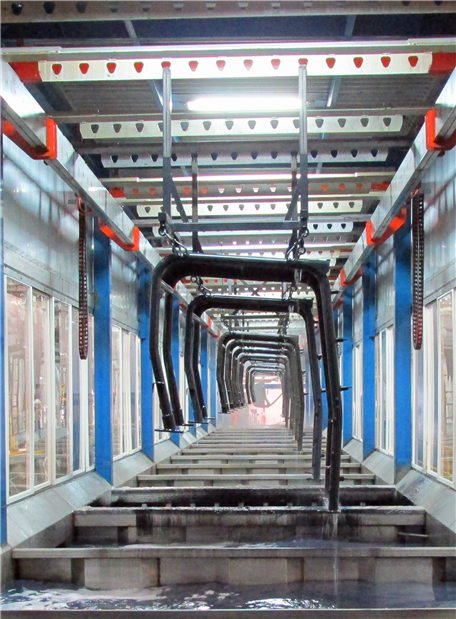
Basic Principle:
Electrophoretic coating is a process that uses an electric field to form a uniform and durable coating on the surface of a conductive object. The electrophoretic tank is the core equipment in the electrophoretic coating line, and its working principle is based on electrochemical reactions and electric field effects. The following are the basic principles of the electrophoretic tank:
- Electrochemical reaction
In the electrophoretic tank, the surface of the workpiece is immersed in an electrophoretic paint solution, usually water-based. The particles in the paint are charged, usually negatively. The surface of the workpiece is then connected to the anode (positive electrode), and when the current passes through the electrophoretic tank, the paint particles are guided to the surface of the workpiece. - Electric field effect
The electrophoretic tank is equipped with an internal electrode system that generates an electric field by applying a voltage. This electric field attracts the charged paint particles to the surface of the workpiece, causing them to be evenly deposited on the surface of the workpiece. This process is called electrophoretic deposition, in which the paint particles are deposited on the surface of the workpiece and form a uniform coating. - Coating curing
Once the coating particles are deposited on the surface of the workpiece, the coating usually needs to be cured. This can be achieved by methods such as baking or UV curing. After curing, the coating will be strong and have excellent adhesion.
Application areas:
Automotive Manufacturing
Electrophoretic coatings play a key role in automotive manufacturing, providing an anti-corrosion and wear-resistant coating for the exterior of the vehicle, improving the appearance quality, and life of the vehicle.
Metal Manufacturing
The metal manufacturing industry uses electrophoretic coatings to protect metal products from rust and corrosion. This includes pipes, guardrails, steel structures, etc.
Appliance Manufacturing
Electrophoretic coatings are also used to coat household appliances such as refrigerators, washing machines, microwave ovens, etc. to provide an attractive and corrosion-resistant surface.
Construction
The construction industry uses electrophoretic coatings to protect building structures, such as steel beams and aluminum window frames, from adverse weather conditions.
Product Features
- Highly automated
- Uniform coating
- Large batch processing
- Flexibility
Learn more about the details ?
FAQ
The gantry-type electrodeposition coating line offers the advantages of high automation, uniform coating, high-volume handling and flexibility. It increases productivity and reduces human error, while ensuring quality and consistency of coating. The gantry-type electrophoresis line is ideal for painting operations that require large scale, high quality painting.
The gantry-type electrodeposition coating line is widely used in industries such as automotive manufacturing, furniture manufacturing, metalwork painting, electronic products and building decoration. It is suitable for painting workpieces of different shapes, sizes and materials, including flat, curved and three-dimensional workpieces, as well as a wide range of materials such as metal, plastic and wood.
Gantry-type electrodeposition coating lines ensure coating quality by providing uniform coating coverage through stable motion trajectories and coating devices. Our equipment is equipped with advanced computer control systems and sensors that are capable of monitoring and adjusting the coating parameters to achieve a precise coating process.
Yes, gantry-type electrodeposition coating lines are flexible and can be designed and adjusted to suit customised needs. We can customise a gantry-type electrodeposition coating line to suit the size, shape and coating requirements of the workpiece to ensure optimum coating results and production efficiency.