Home » Products » E-coating System Accessories » Dosing System
E-coat Dosing system
Flexible and efficient e-coating system.
In the electrophoretic coating line equipment, the dosing system is the system used to add coating solution or coating raw material. It has the following roles in the electrophoretic coating process:
- Supply of paint: Controlling components such as pumps, pipes, and valves in the dosing system, ensures a stable supply and flow of paint.
- Maintaining paint consistency: By accurately controlling the amount of paint added and the ratio of the solution, it ensures that the paint is within a certain concentration range to meet the requirements of the coating process.
- Adjustment of coating properties: The dosing system can add different additives to the coating, such as diluents, curing agents, anti-sinking agents, etc.
In general, the dosing system plays an important role in supplying the coating material, maintaining the concentration of the coating material, regulating the performance of the coating material, controlling the temperature of the coating material, as well as monitoring and regulating the flow of coating material in the electrophoretic coating line equipment. It is vital to achieving a stable, high-quality electrophoretic coating process.
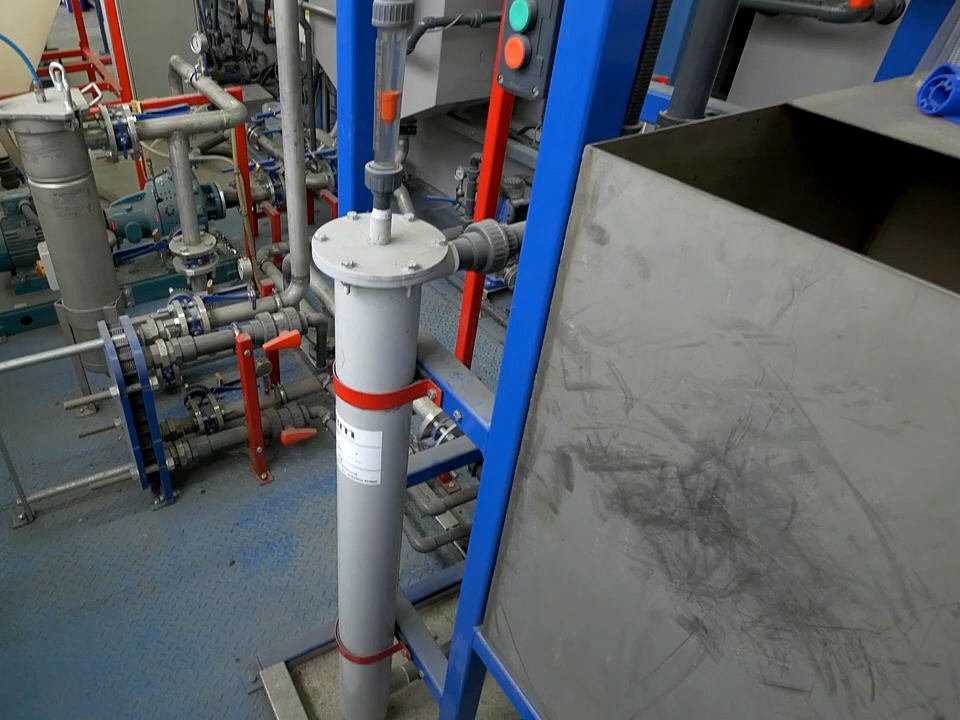

Product Description
In the electrophoretic coating line equipment, the dosing system is the system used to add coating solution or coating raw material. It has the following roles in the electrophoretic coating process:
- Supply of paint: controlling components such as pumps, pipes, and valves in the dosing system, ensures a stable supply and flow of paint.
- Maintaining the concentration of paint: By accurately controlling the amount of paint added and the ratio of the solution, it ensures that the paint is within a certain concentration range to meet the requirements of the coating process.
- Adjustment of coating properties: The dosing system can add different additives to the coating, such as diluents, curing agents, anti-sinking agents, etc. These additives can adjust the viscosity of the coating. These additives can regulate the viscosity, drying speed, antioxidant properties, etc. of the coating to meet different coating requirements.
- Controlling Paint Temperature: The dosing system is usually connected to the paint heating system, which can be heated or cooled to control the temperature of the paint. Maintaining the proper coating temperature improves flow, reduces viscosity, and affects the quality and performance of the coating.
- Monitoring and regulating paint flow: Dosing systems are often equipped with flow meters and control valves to monitor and regulate paint flow. By accurately controlling the flow of coating material, a consistent supply of coating material can be ensured during the coating process, avoiding coating defects and waste.
In general, the dosing system plays an important role in supplying the coating material, maintaining the concentration of the coating material, regulating the performance of the coating material, controlling the temperature of the coating material, as well as monitoring and regulating the flow of coating material in the electrophoretic coating line equipment. It is vital to achieving a stable, high-quality electrophoretic coating process.
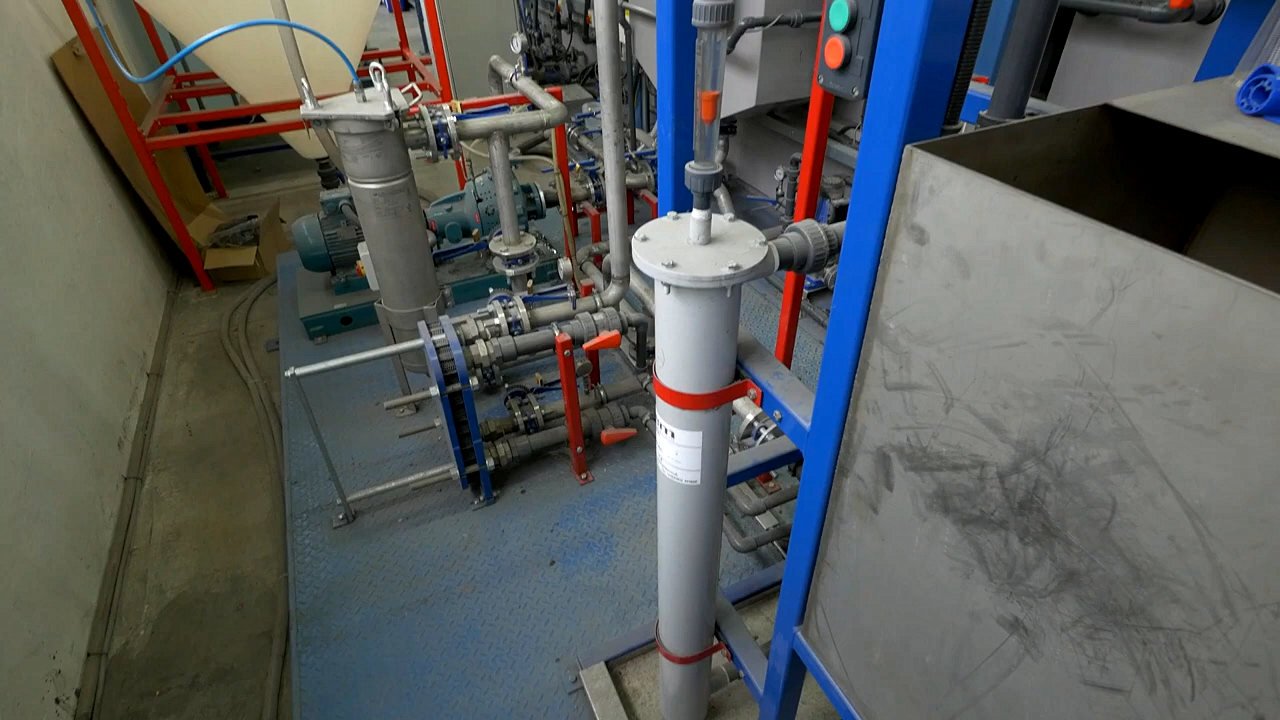
Industry applications:
Automobile manufacturing industry: used to accurately control the amount of paint to ensure the consistency and quality of the coating of automobile parts (such as body, chassis, doors, etc.).
Home appliance industry: used in the coating process of home appliances (such as refrigerators, washing machines, air conditioners, etc.) to improve the efficiency of paint use and coating uniformity.
Metal processing industry: used for electrophoretic coating of various metal surfaces (such as steel, aluminum alloy, etc.) to enhance their corrosion resistance and aesthetics.
Mechanical equipment: such as surface treatment of tools, machine parts, steel frames, etc., to improve durability and wear resistance.
Product Features
- Highly automated
- Uniform coating
- Large batch processing
- Flexibility
Learn more about the details ?
FAQ
The gantry-type electrodeposition coating line offers the advantages of high automation, uniform coating, high-volume handling and flexibility. It increases productivity and reduces human error, while ensuring quality and consistency of coating. The gantry-type electrophoresis line is ideal for painting operations that require large scale, high quality painting.
The gantry-type electrodeposition coating line is widely used in industries such as automotive manufacturing, furniture manufacturing, metalwork painting, electronic products and building decoration. It is suitable for painting workpieces of different shapes, sizes and materials, including flat, curved and three-dimensional workpieces, as well as a wide range of materials such as metal, plastic and wood.
Gantry-type electrodeposition coating lines ensure coating quality by providing uniform coating coverage through stable motion trajectories and coating devices. Our equipment is equipped with advanced computer control systems and sensors that are capable of monitoring and adjusting the coating parameters to achieve a precise coating process.
Yes, gantry-type electrodeposition coating lines are flexible and can be designed and adjusted to suit customised needs. We can customise a gantry-type electrodeposition coating line to suit the size, shape and coating requirements of the workpiece to ensure optimum coating results and production efficiency.