In the metal surface treatment, liquid coating line plays a vital role due to their unmatched efficiency and precision in achieving high-quality coatings. Industries relying on these systems demand consistent performance to meet production goals and maintain product standards.
Effective maintenance is crucial to ensuring this reliability. Studies show that systematic maintenance can reduce downtime risks by up to 90%, significantly improving operational continuity. By investing in proactive upkeep, businesses can safeguard production flow, and minimize costly interruptions.
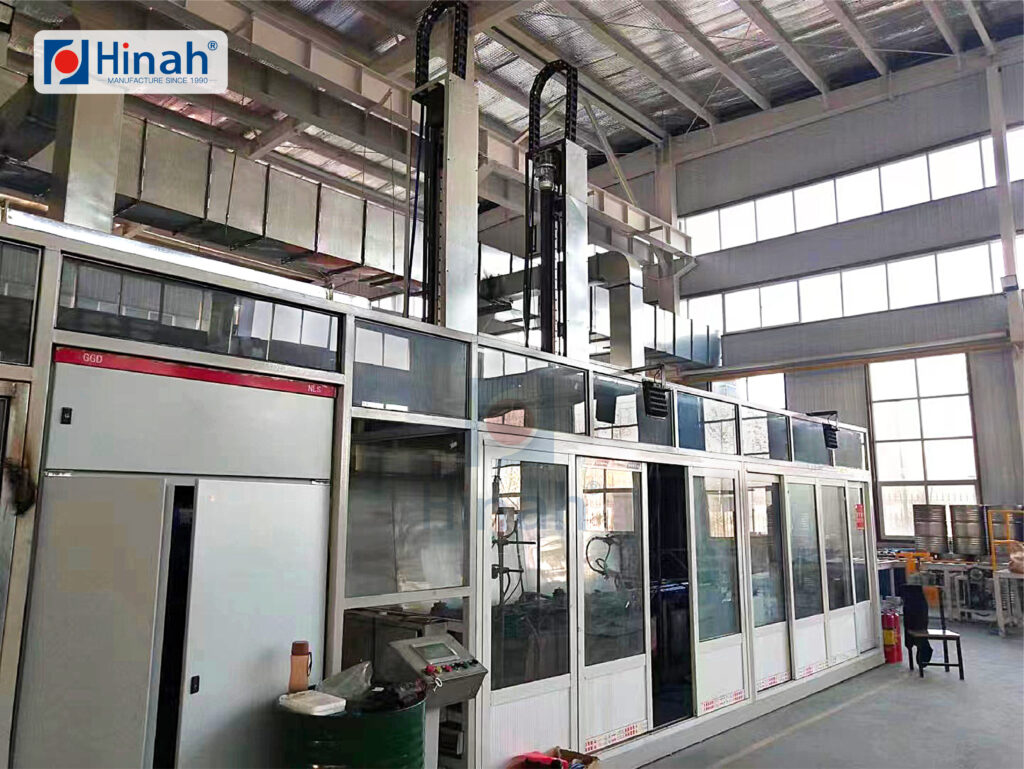
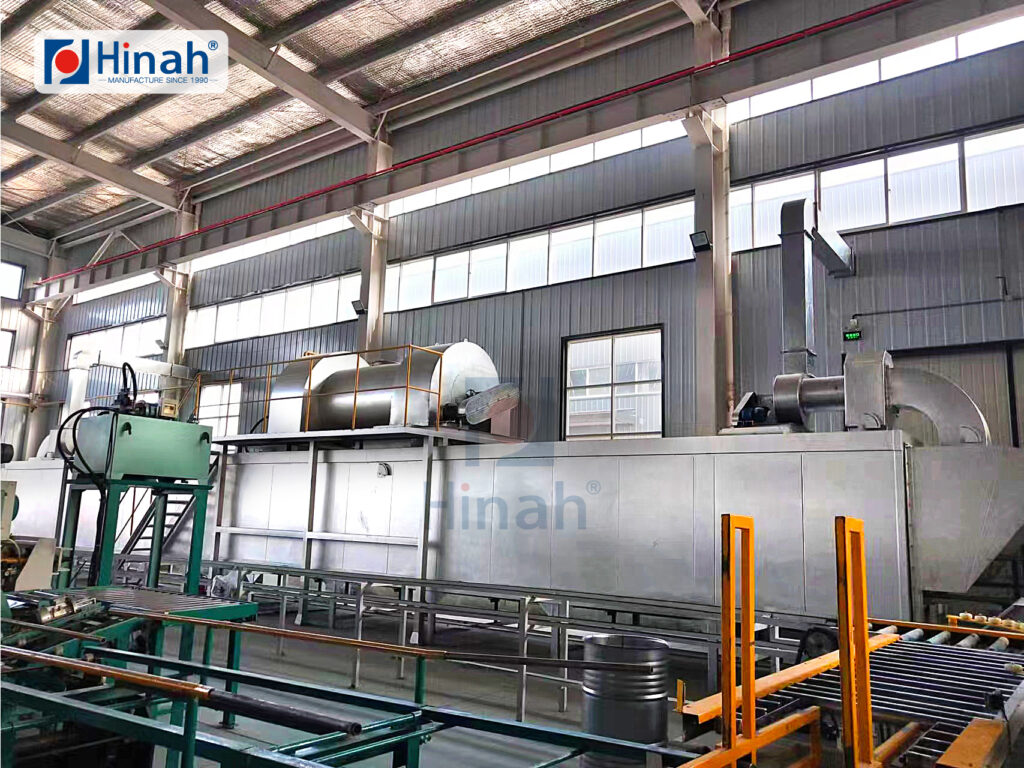
Common Liquid Coating Line Issues
Even well-designed liquid coating lines can encounter issues that disrupt production. Understanding these common problems is key to preventing costly downtime.
Issue 1: Liquid Coating Line Clogging
Clogging is often caused by paint sediment buildup, filter failures, or insufficient pipeline cleaning. Over time, these factors restrict flow, reducing coating quality and causing system blockages. Regular flushing and filter inspections can help prevent this.
Issue 2: Inconsistent Spray Patterns
Uneven spray patterns may result from worn nozzles, unstable air pressure, or variations in paint viscosity. Routine nozzle checks, maintaining stable pressure, and monitoring paint consistency are very important.
Issue 3: Curing Oven Inefficiency
Curing ovens may lose efficiency due to aging heating elements, uneven airflow, or faulty temperature sensors. Regular calibration, airflow adjustments, and timely replacement of worn components are crucial to maintaining optimal curing conditions.
Issue 4: Electrical System Failures
Electrical issues often stem from PLC programming errors, sensor contamination, or aging wiring. Routine inspection of sensors, software updates, and wiring checks can reduce the risk of unexpected shutdowns.
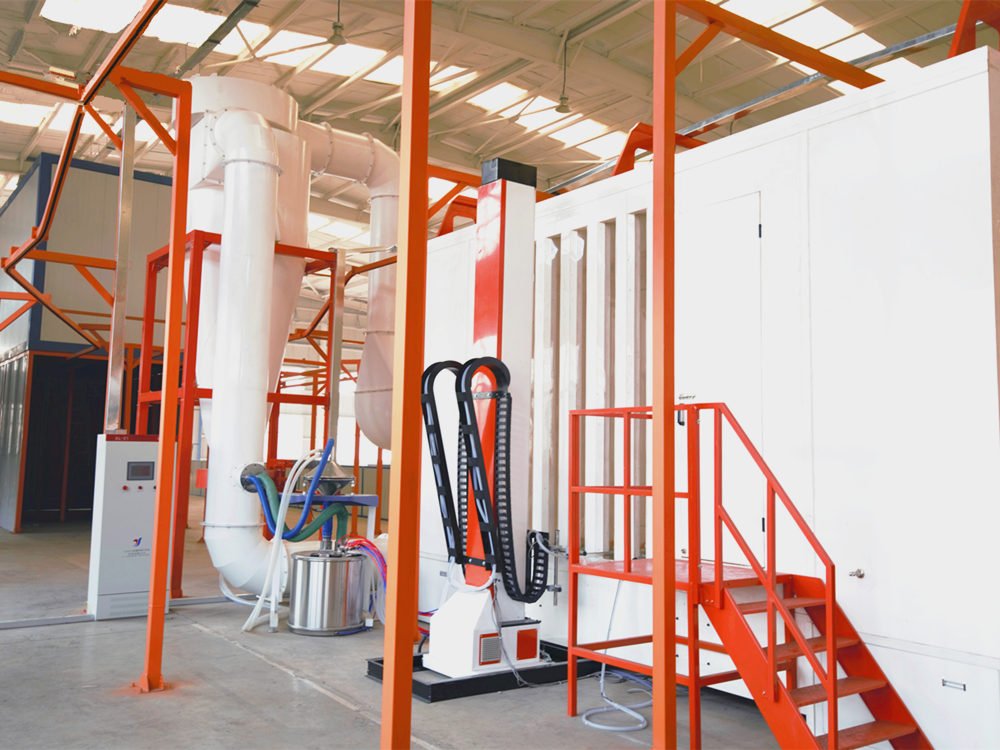
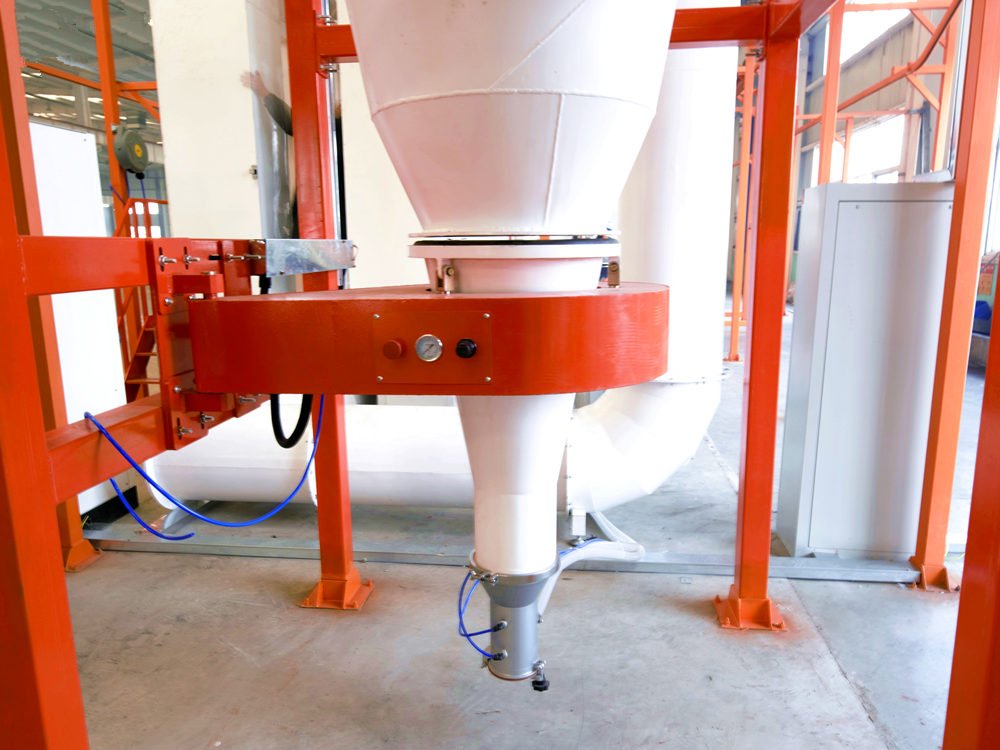
Key Maintenance Tasks for a Liquid Coating Line
To keep your liquid coating line running at peak performance, regular maintenance is essential. Here are key tasks that ensure efficiency, quality, and longevity:
1. Clean and Flush the System Regularly
Paint residues can accumulate in pipes, filters, and spray nozzles, leading to clogging. Regularly flushing the system with appropriate cleaning agents helps prevent buildup and ensures smooth operation.
2. Inspect and Replace Filters
Filters are critical in keeping contaminants out of the coating system. Establish a routine to inspect and replace filters to maintain consistent paint flow and protect equipment components.
3. Calibrate Spray Guns and Nozzles
Worn or misaligned spray guns can cause uneven coatings. Regular calibration and timely nozzle replacement ensure precise spray patterns and optimal material usage.
4. Monitor and Maintain the Curing Oven
Check heating elements, airflow systems, and temperature sensors to ensure the curing oven maintains stable and accurate heat levels. This prevents under-curing or over-curing defects.
5. Conduct Routine Electrical System Checks
Regularly inspect PLC programming, wiring connections, and sensors for signs of wear or malfunction. Addressing minor electrical issues early can prevent costly system failures.
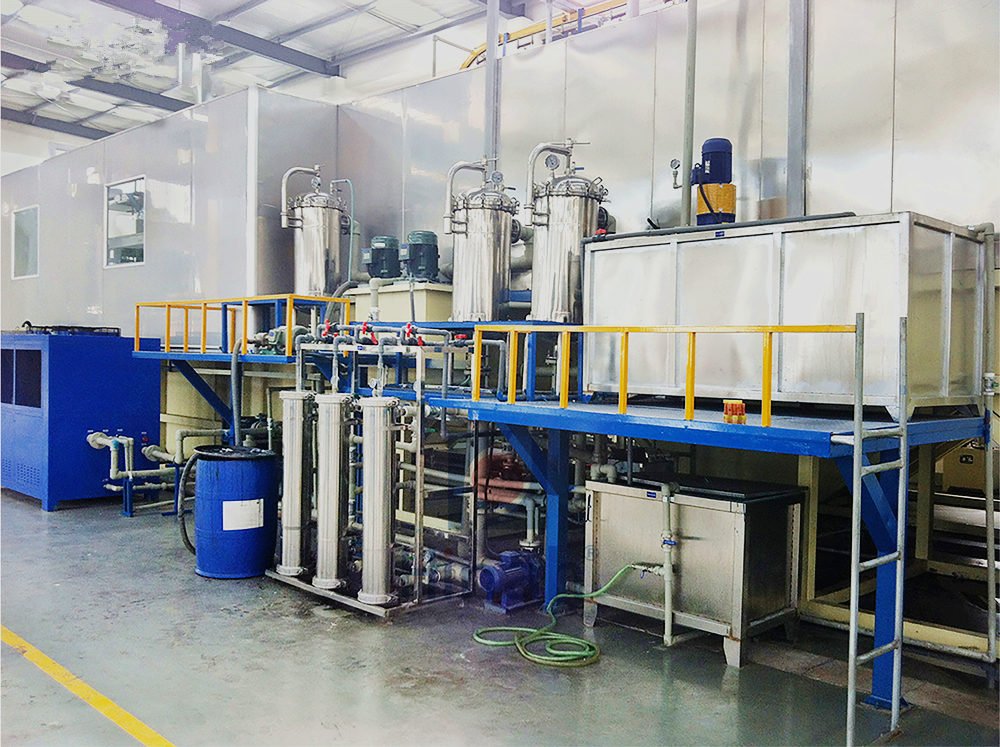
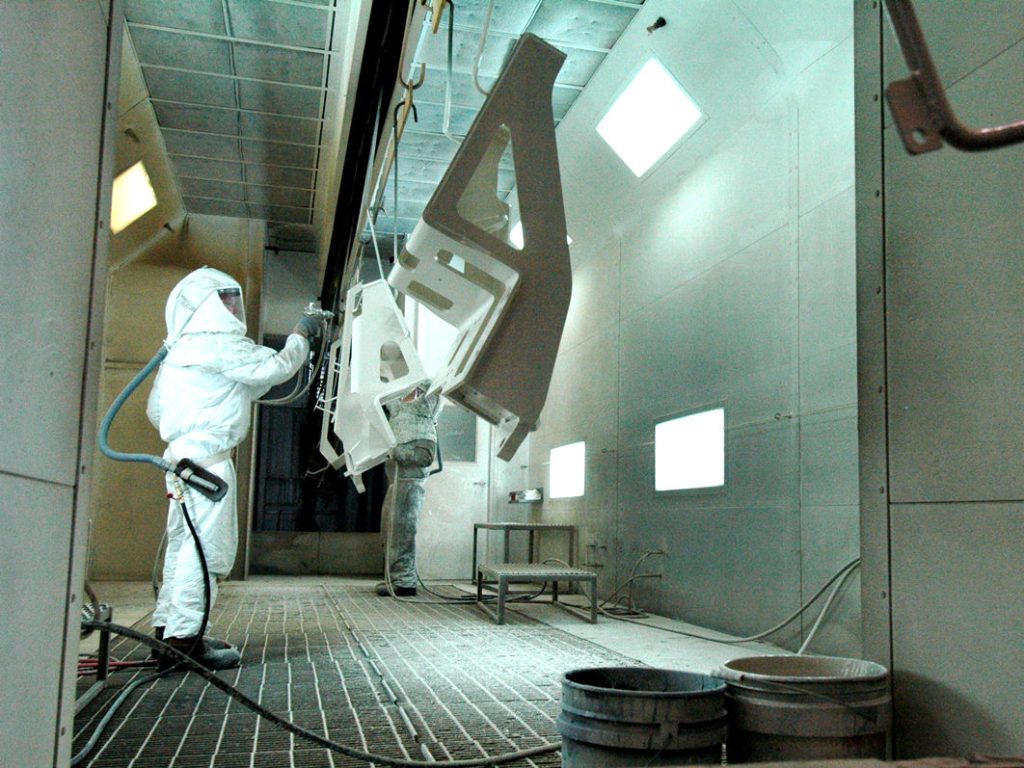
Benefits of Proactive Liquid Coating Line Maintenance
Investing in proactive maintenance for your liquid coating line offers several key benefits that go beyond just keeping the system running.
- Cost Savings
Preventive maintenance helps identify and resolve minor issues before they escalate into costly repairs or prolonged downtime. By replacing worn parts, cleaning pipelines, and inspecting filters regularly, businesses can avoid emergency shutdowns and reduce expenses on major repairs.
- Improved Quality
Consistent maintenance ensures stable coating performance, reducing defects such as uneven finishes, drips, or under-curing. With well-maintained equipment, businesses can deliver high-quality products that meet customer expectations and minimize rework or product waste.
- Sustainability Advantage
A well-maintained system operates more efficiently, reducing energy consumption and minimizing material waste. By optimizing spray patterns, curing conditions, and airflow systems, businesses can achieve eco-friendly production while lowering operational costs.
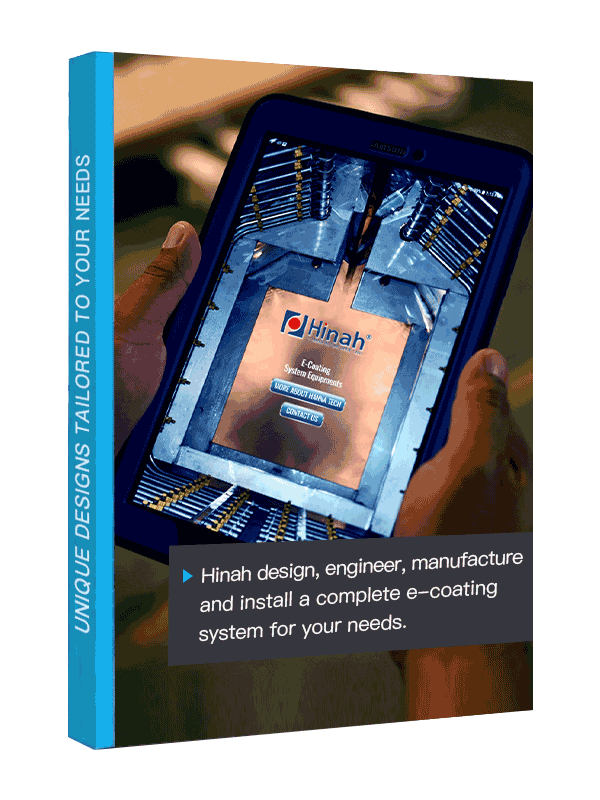
Let's Have A Chat
Get An E-coating Line Planning !
Match Your Products, Get The Solution & Price..
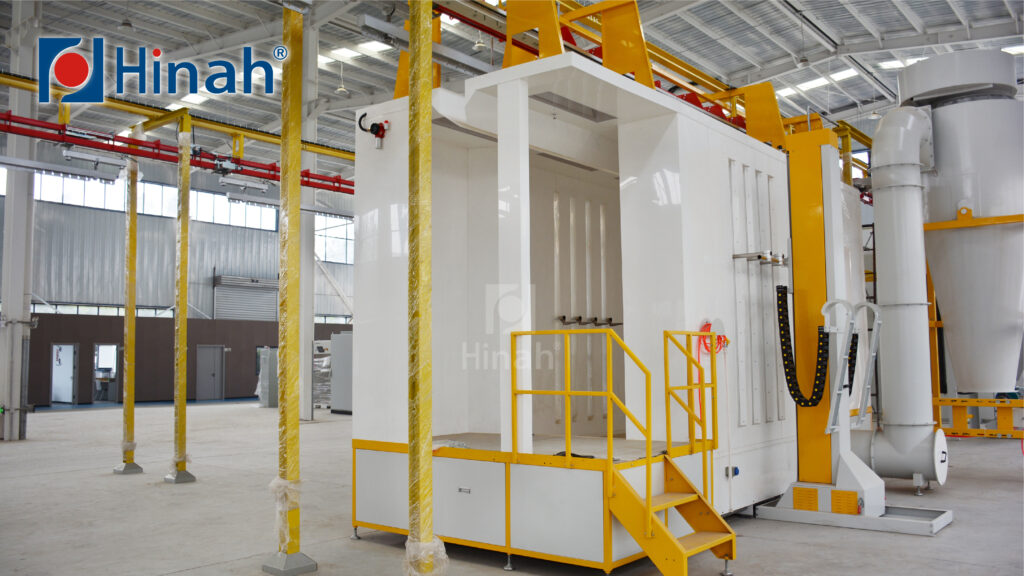
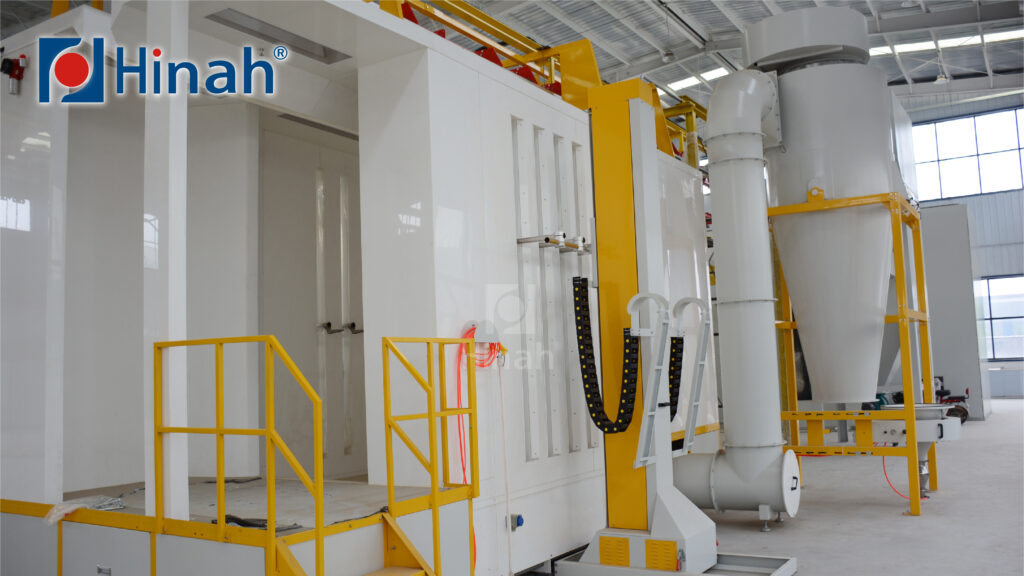
Turn Maintenance into Your Competitive Edge
A stable and well-maintained liquid coating line is more than just a production asset — it’s a strategic advantage. Reliable equipment ensures consistent product quality, fewer disruptions, and improved efficiency, directly contributing to customer trust and business profitability.
By adopting proactive maintenance practices, businesses can minimize costly downtime, enhance product consistency, and promote sustainable operations. In the competitive world of surface finishing, turning maintenance into a priority is the key to long-term success.