In modern manufacturing, the choice of coating process is crucial to product quality and production efficiency. As a widely used coating technology, a liquid coating line is particularly suitable for large-scale production environments. With the continuous growth of production needs, liquid coating lines have become an ideal choice for high-volume manufacturing due to their high efficiency and flexibility. Liquid coating can not only ensure the uniformity and quality of the coating but also process the surfaces of various materials to meet the coating needs of different industrial fields. This article will explore the advantages of liquid coating lines, especially their application in high-volume manufacturing, and the huge benefits they bring.
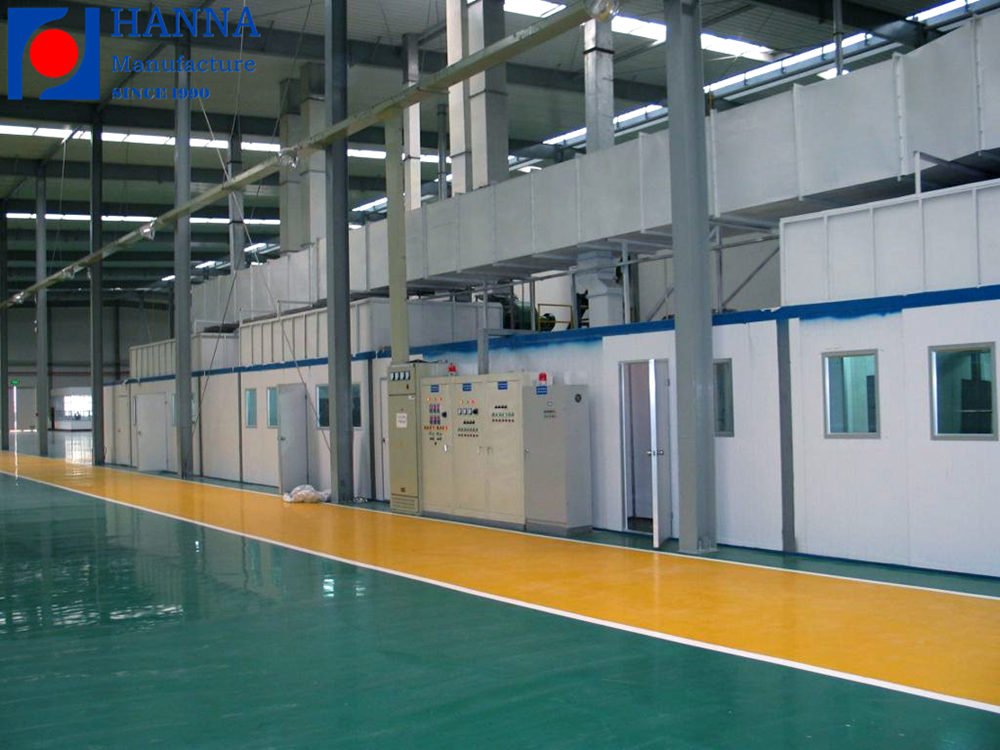
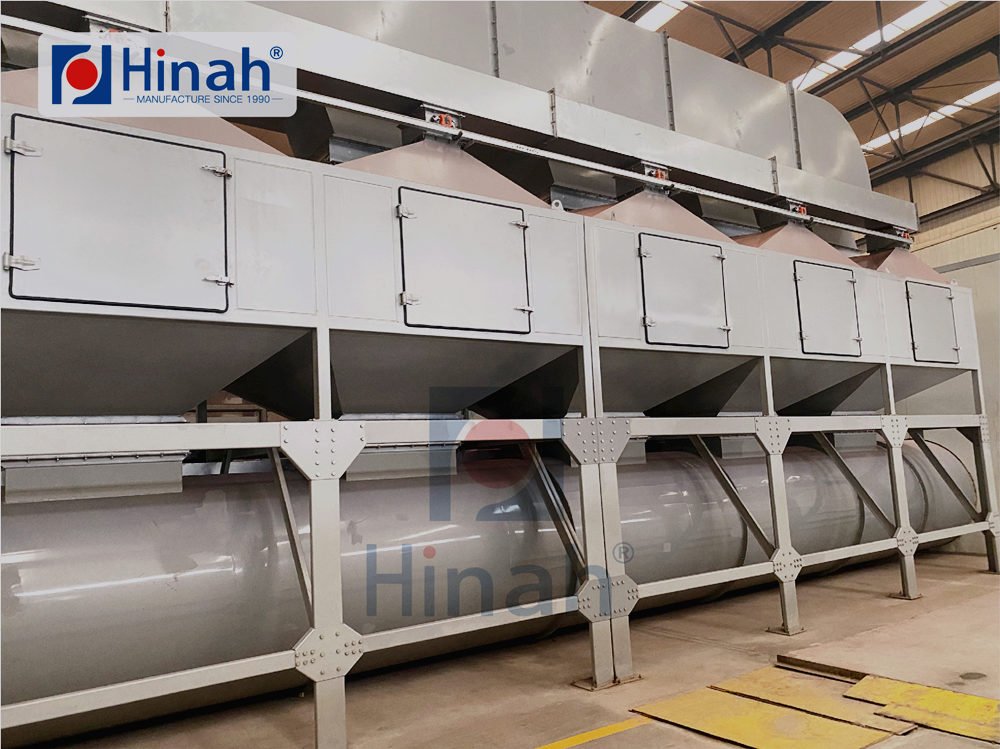
I. Overview of Liquid Coating Line
Liquid coating line is a production line system that uses liquid coating to coat the surface of products. Unlike powder coating, liquid coating uses liquid coating containing solvents, which is evenly coated on the surface of products by spray gun, roller coating, or dipping. Liquid coating technology is widely used in many industries such as automobiles, home appliances, construction, machinery, etc., and can provide smooth, durable coatings with excellent visual effects.
The basic components of liquid coating lines usually include the following main parts:
- Paint spraying system: This is the core part of the liquid coating line, usually including automatic spray guns, spray chambers and paint recovery devices. The spraying system is responsible for evenly coating the liquid paint on the surface of the object.
- Pre-treatment system: Before coating, the surface of the product usually needs to be cleaned, degreased, and rust-removed to ensure the adhesion and long-term durability of the coating. Common pre-treatment methods include pickling, sandblasting, phosphating, etc.
- Drying or curing system: After the coating is applied, the coating needs to be cured by heating or ultraviolet irradiation so that it can form a solid protective layer. The drying system usually includes a heating furnace, ultraviolet curing equipment, etc.
- Conveying system: To ensure that the coated products can smoothly enter each link, the liquid coating line is usually equipped with an automated conveying system, such as a chain conveyor, a slide rail, etc., to achieve efficient movement of products between various processes.
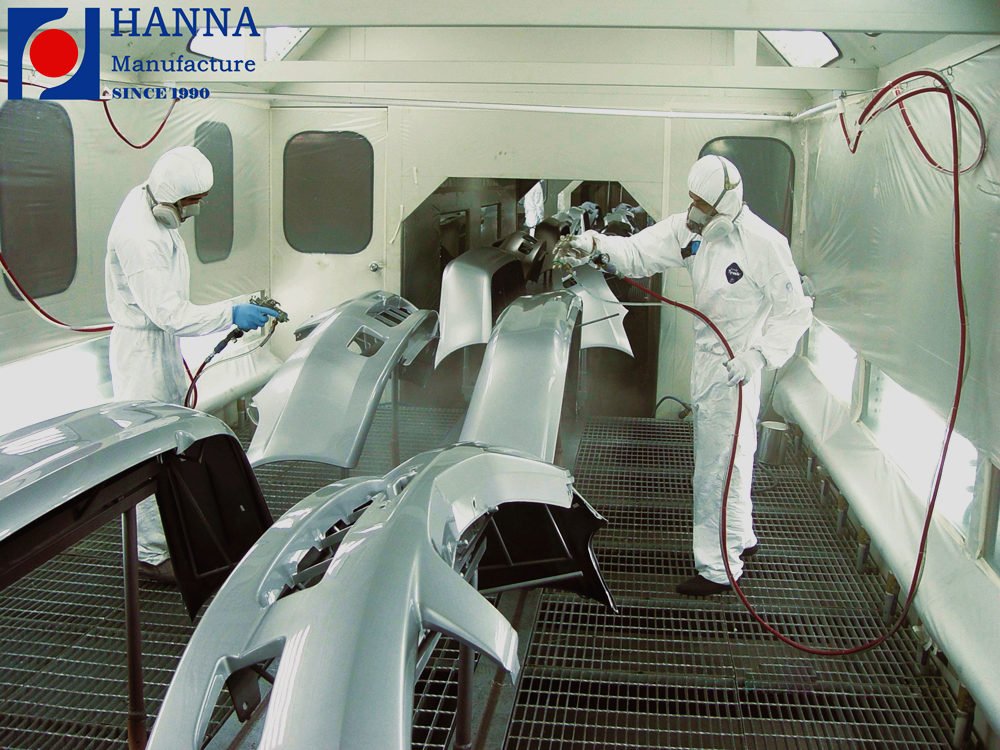
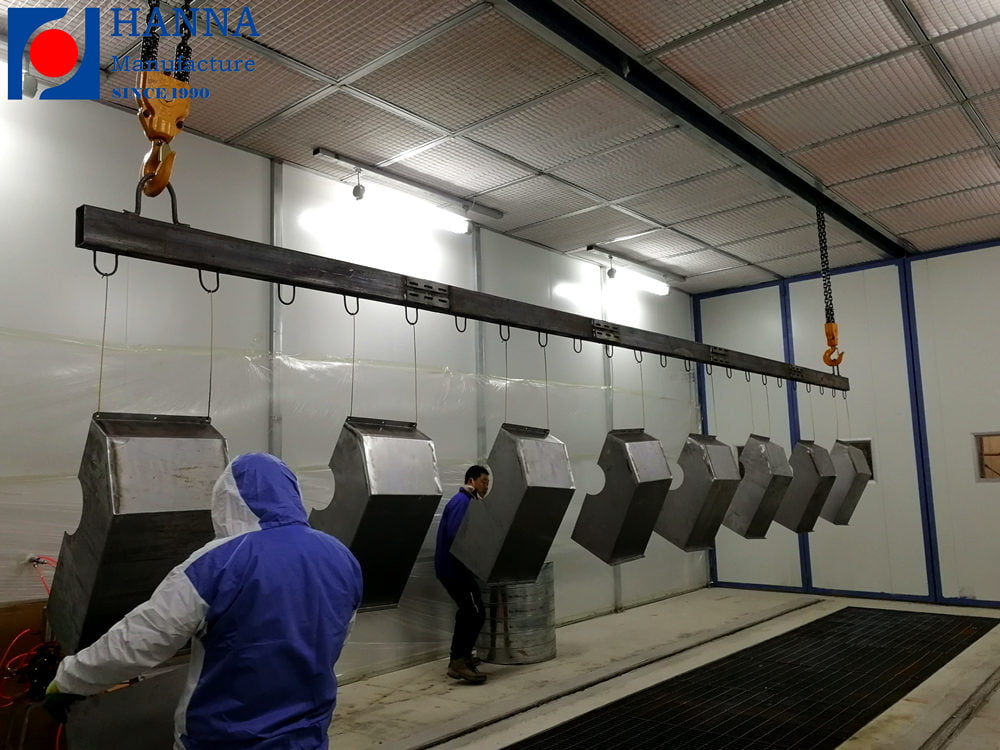
II. Advantages of liquid coating line
1. Wide adaptability
Liquid coating line is highly adaptable and can coat many different types of substrates, including metal, plastic, wood, glass, etc. Whether conventional industrial or special composite materials, liquid coating can provide good adhesion and coating quality. This diversity makes liquid coating lines an indispensable surface treatment tool in various industries.
2. Rich colors, effects, and surface textures
Liquid coating technology provides extremely rich color options and decorative effects. In addition to basic single-color coatings, various surface textures and visual effects such as metallic luster, pearlescent effect, frosted texture, etc. can be created by adding different types of pigments, gloss regulators, and effect materials. This makes the liquid coating line not only meet functional needs but also provide highly customized aesthetic effects.
3. High chemical resistance and high mechanical strength
Liquid coating can form a protective layer with high chemical resistance and mechanical strength, which is particularly suitable for application scenarios that need to withstand harsh environments. The coating can effectively resist corrosion, solvents, acids, alkalis, and other chemicals, and has good scratch resistance, impact resistance, and wear resistance, ensuring the durability and reliability of the coated products in long-term use.
4. Accurate coating thickness control
The spraying technology of the liquid coating line can achieve precise coating thickness control and even apply extremely thin coatings. This is especially important for those application scenarios that have strict requirements on coating thickness, such as electronic products, precision instruments, etc. Thin coatings can not only save paint but also maintain excellent functionality and aesthetics.
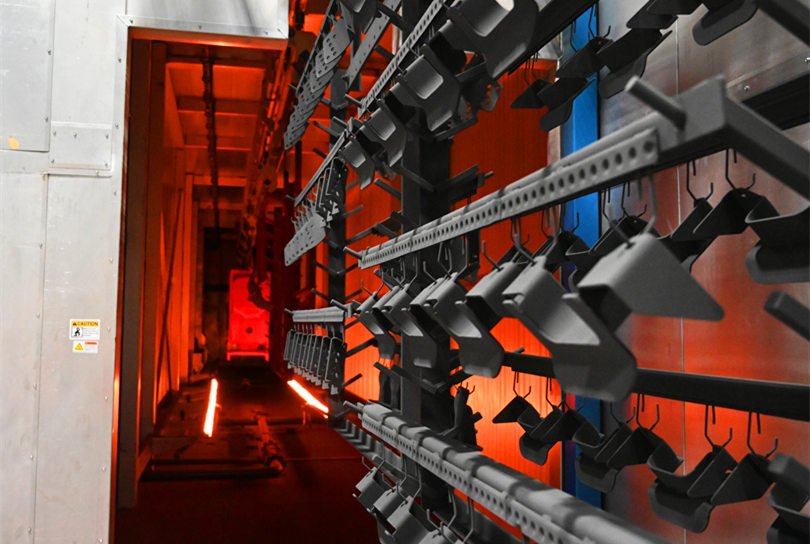
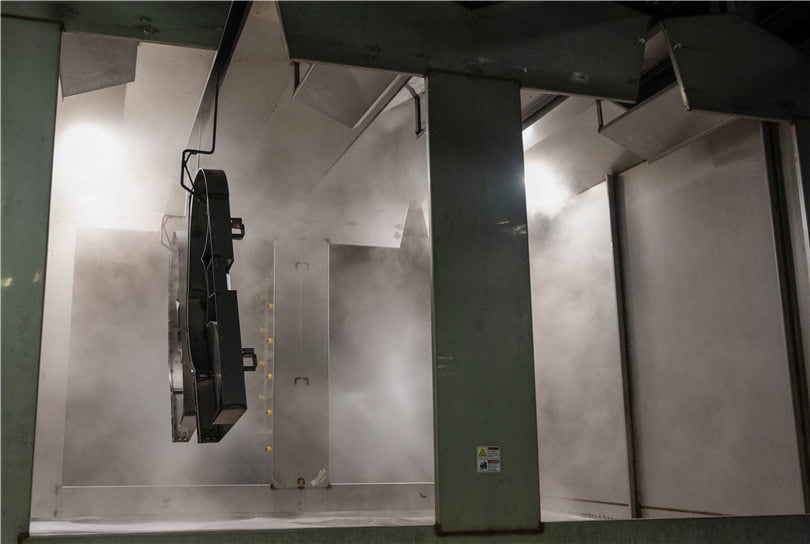
III. Why is liquid coating line suitable for high-volume production?
1. High-speed application: Liquid coatings can be quickly sprayed or flowed onto surfaces using automated systems, allowing for rapid coverage of large areas and high production volumes.
2. Flexible coating types: A wide range of liquid coatings, including water-based, solvent-based, and high-performance formulations, are available to meet different application needs and desired surface effects.
3. Precise control: Advanced spray guns and fluid delivery systems allow for precise control of coating thickness and application patterns, resulting in consistent quality in large quantities.
4. Scalability: Liquid coating line can be easily expanded to accommodate increased production volumes by adding additional application stations or expanding the delivery system.
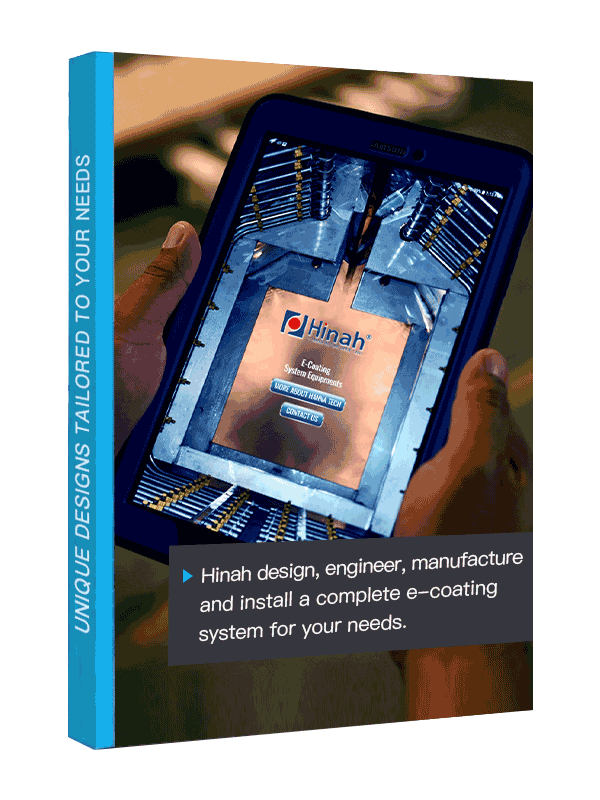
Let's Have A Chat
Get An E-coating Line Planning !
Match Your Products, Get The Solution & Price..
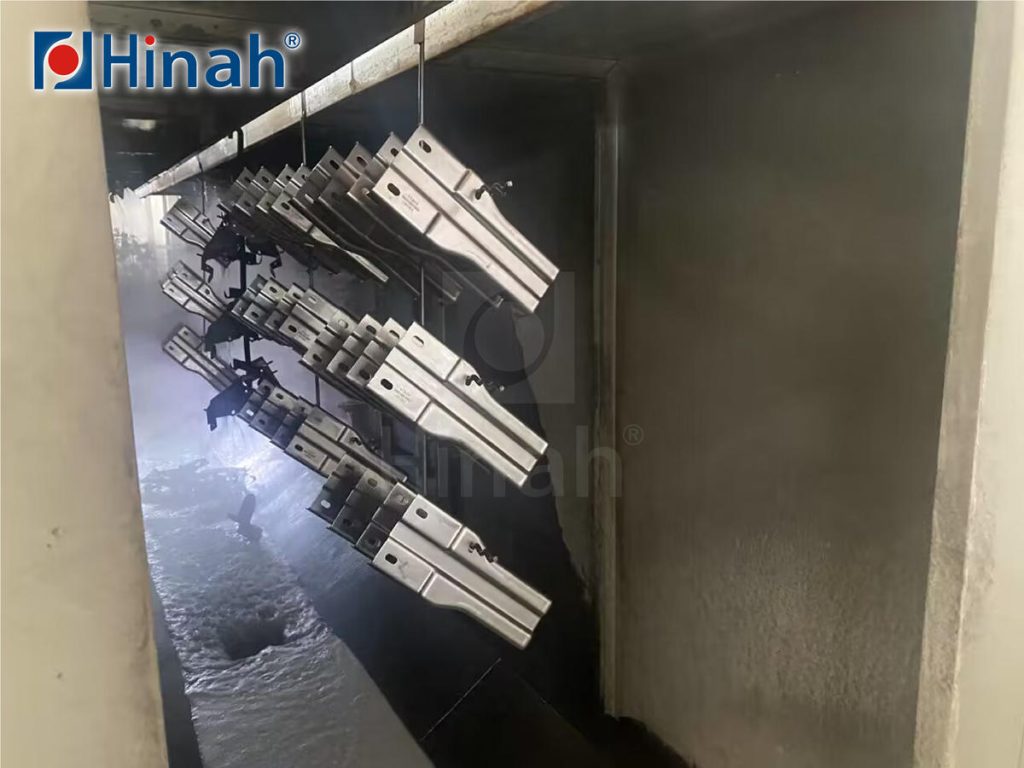
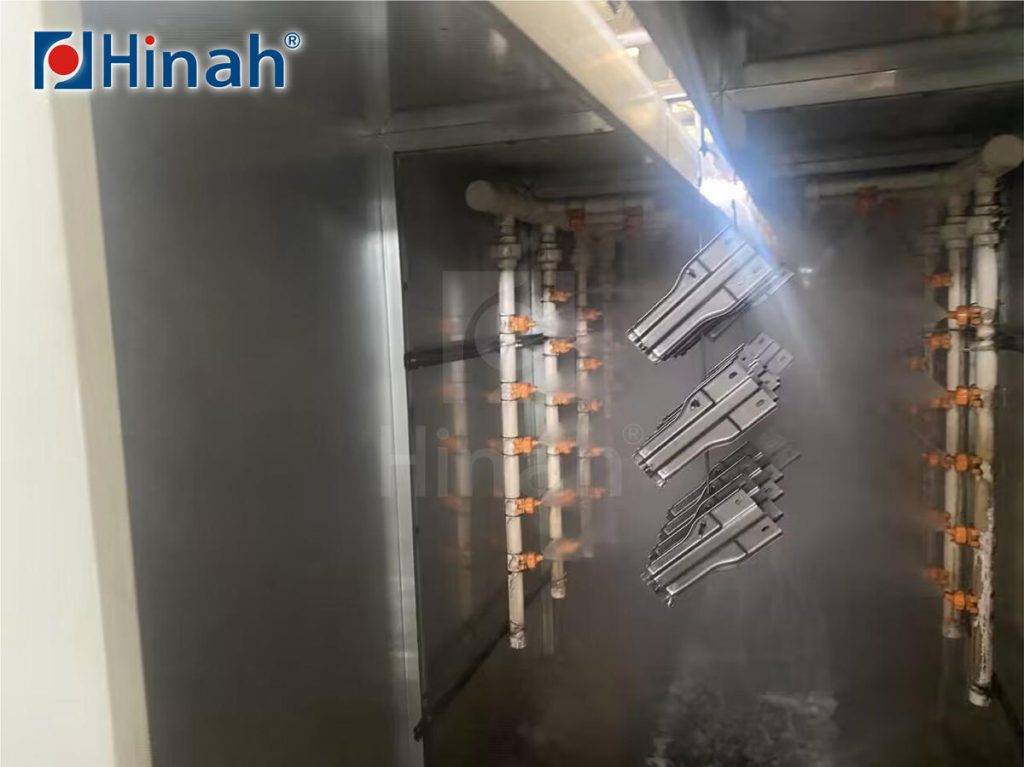
IV. How long can liquid coatings last?
The lifespan of liquid coatings is generally between 3 and 10 years, but the actual lifespan varies for different coating types.
- Acrylic coatings: Usually last 3 to 5 years. Acrylic coatings are often used in outdoor applications and have good UV resistance.
- Polyurethane coatings: Usually last 5 to 10 years, depending on the environment. Polyurethane coatings have excellent wear resistance and are often used in industrial and automotive coatings.
- Epoxy coatings: Epoxy coatings usually last between 5 and 10 years, are suitable for harsh environments, and have excellent chemical resistance.
- Baking varnish coatings (glaze coatings): Usually last 5 to 7 years and are more affected by sunlight and moisture.
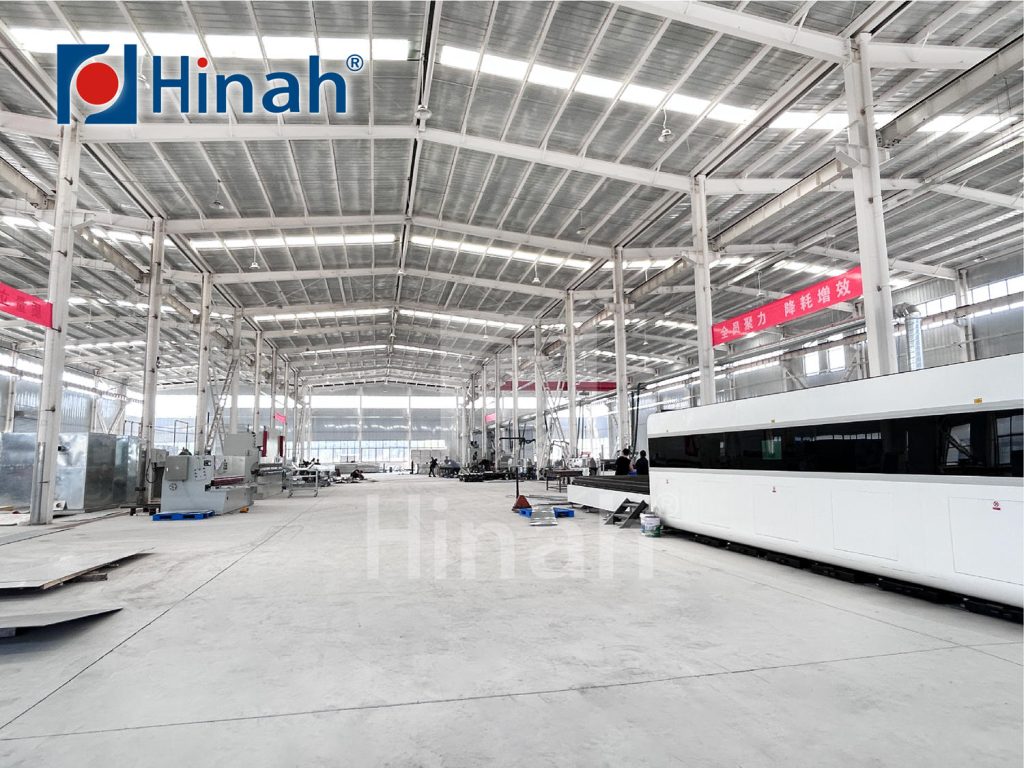
V. How to maintain the life of liquid coating?
1. Regular cleaning
It is very important to keep the coating surface clean. Regularly remove dirt, grease, and other contaminants to prevent them from eroding the coating surface. When cleaning, avoid using strong acid or alkaline cleaners to avoid damaging the coating.
2. Prevent mechanical damage
Avoid physical damage such as friction or impact on the coating, especially during handling or installation. Use a soft cloth or soft brush to wipe to avoid scratching the coating surface.
3. Prevent UV exposure
Exposed to sunlight for a long time, ultraviolet rays will accelerate the aging of the coating, causing color fading or brittle coating. Therefore, use UV shielding paint or strengthen coating protection when necessary to extend the life of the coating.
4. Control environmental humidity
High-humidity environments can cause bubbles, peeling, or corrosion on the coating surface, especially on metal surfaces. Therefore, when used in an environment with high humidity, avoid excessive moisture contact and check the integrity of the coating regularly.

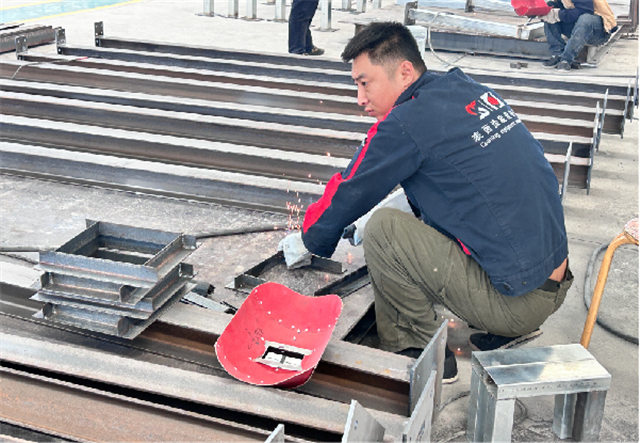
VI. Conclusion
Liquid coating line has become a key surface treatment tool in many industries due to their wide adaptability, rich color effects, excellent chemical resistance, and mechanical strength. Its precise coating thickness control and efficient mass production capabilities make the liquid coating line outstanding in meeting large-scale production needs. The life of a liquid coating generally depends on the type of coating and the environment in which it is used, but by taking effective maintenance measures, its service life can be significantly extended. Regular cleaning, avoiding mechanical damage, preventing UV radiation, and controlling ambient humidity are all important measures to ensure the long-term stability of liquid coatings. In general, liquid coating lines not only provide high-quality coating effects but also ensure that the coating can play its protective function for a long time through proper care and maintenance to meet the needs of various industrial applications.