E coating equipment is vital in industries like automotive and manufacturing, where it applies protective coatings to metal parts. Its efficiency directly impacts product quality and production timelines.
Regular maintenance ensures optimal performance, extends equipment life, and minimizes downtime. By maintaining e-coating equipment, businesses can improve production efficiency, reduce unexpected repairs, and avoid costly disruptions.
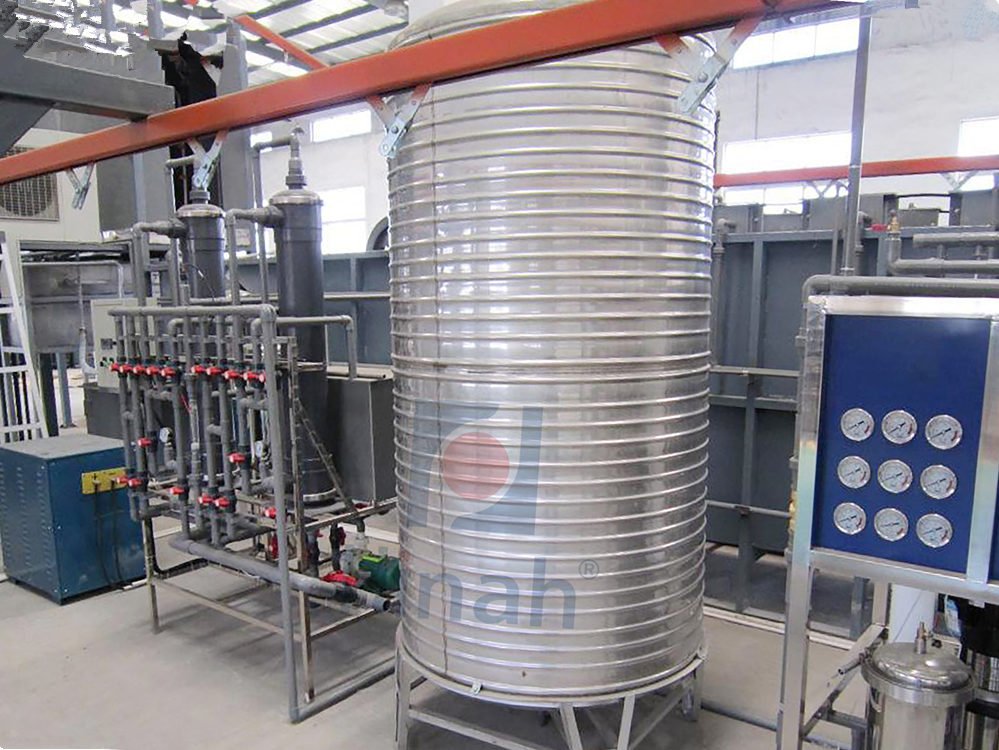
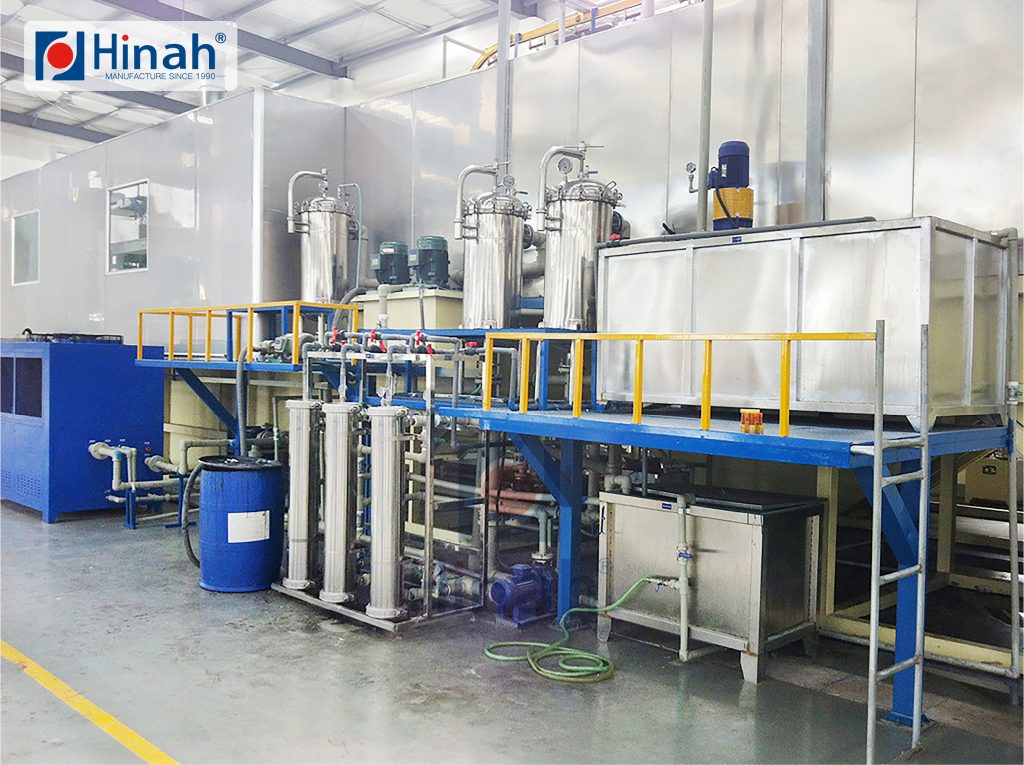
I. Regular cleaning and inspection of e coating equipment
Regular cleaning and inspection are the basis for maintaining the performance and extending the service life of electrophoresis equipment. Over time, paint residue, dirt, and other contaminants may accumulate on key components, which can affect the coating quality and the system’s overall efficiency. Proper maintenance helps prevent these problems and ensures the smooth operation of the equipment.
Cleaning of key components:
- Spray gun: Spray guns may be clogged by dry paint. Regular cleaning can prevent clogging and ensure uniform coating thickness.
- Filter: Filters are used to prevent contaminants from entering the system. Clogged filters will lead to reduced coating quality and reduced system efficiency. They should be cleaned or replaced regularly.
- Tanks and racks: Electrophoresis tanks should be cleaned regularly to remove residues to avoid affecting the coating quality of the next batch. In addition, the racks that carry the parts during the coating process should also be inspected for wear or contamination.
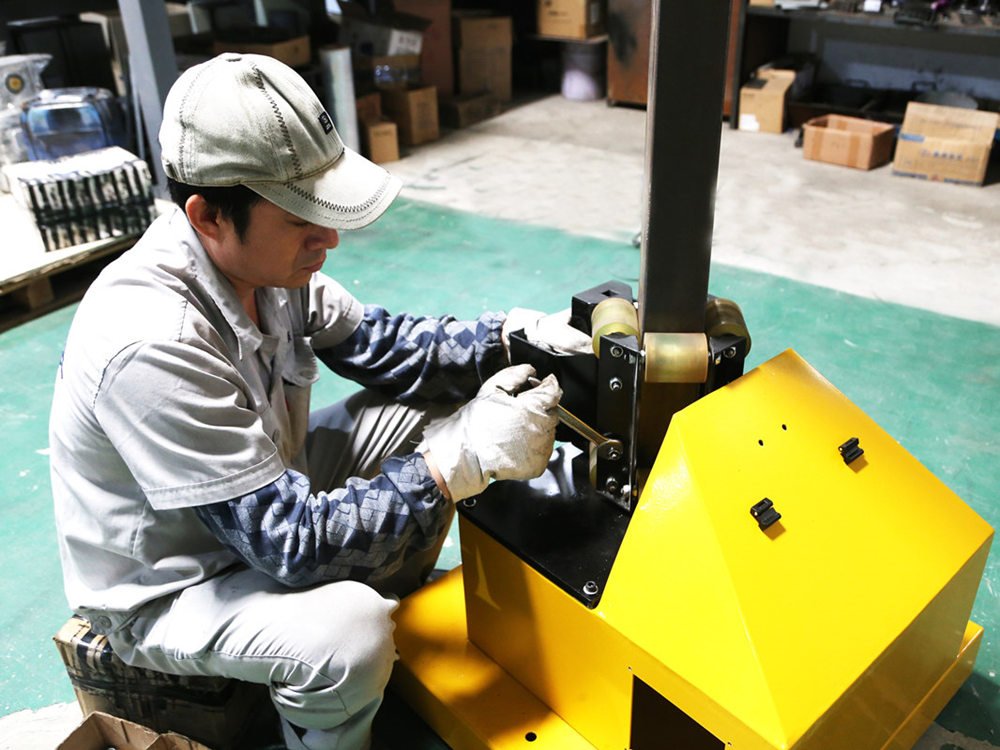
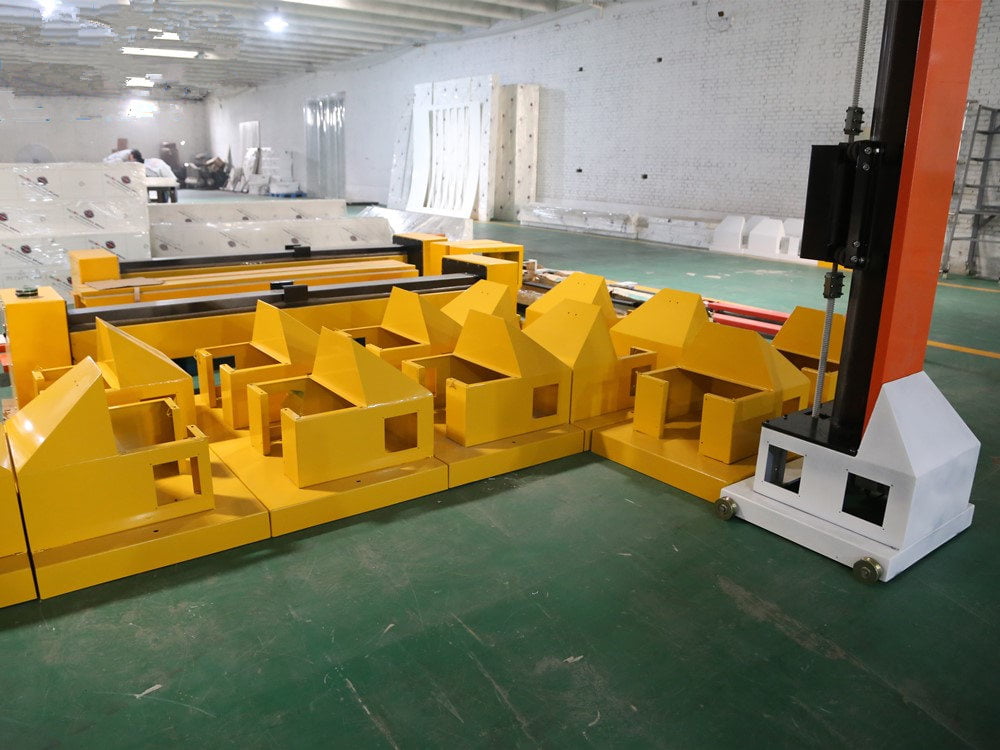
II. Check the quality of e coat tank and coating solution
Ensuring the quality of the electrophoretic tank and coating solution is crucial for the coating effect and equipment performance. Regular inspection helps to ensure the consistency of coating and long-term stable operation of equipment.
1. Coating solution quality inspection
Test the pH, concentration, and temperature of the coating solution regularly to ensure that it meets the operating requirements.
- pH value: A too-high or too-low pH value will affect the adhesion and uniformity of the coating, so it should be kept within the recommended range.
- Concentration: Too low or too high coating concentration may lead to an unsatisfactory coating effect and needs to be checked and adjusted regularly.
- Temperature: The temperature of the solution will affect the quality of the coating and should be kept within the appropriate range.
2. Electrophoretic tank maintenance
Ensure that the coating tank is leak-free and stable to avoid leakage of coating liquid or damage to the tank body.
- Regularly check the tank body for cracks or corrosion.
- Check the tank liquid level to avoid a low solution affecting the coating effect.
3. Solution replacement cycle
The coating solution should be replaced regularly according to the frequency of use and solution quality.
- Replacement frequency: Usually replaced every three to six months according to production volume and solution quality.
- Replacement method: After draining the old solution and cleaning the tank, refill with a new solution to ensure that no contaminants remain.
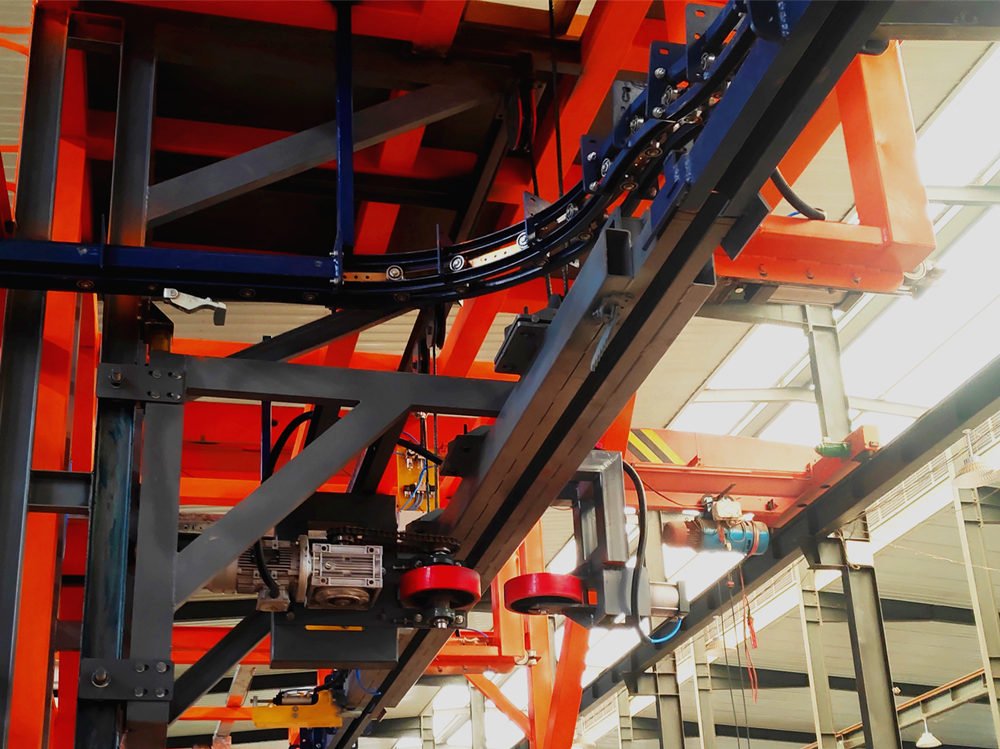
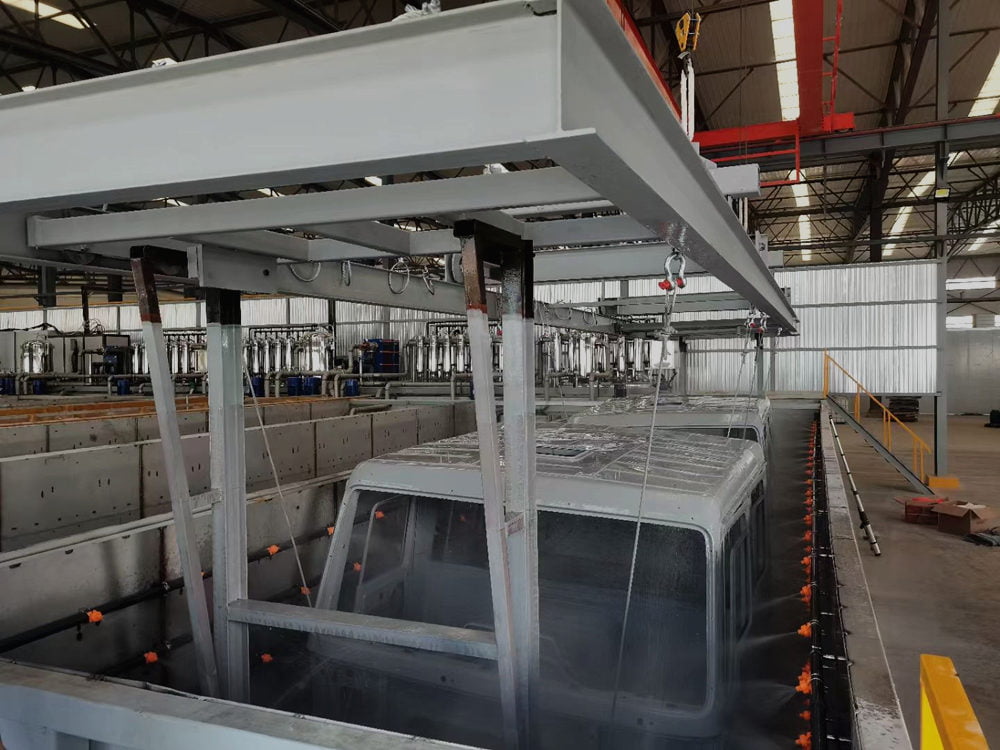
III. Mechanical maintenance of e coating equipment
1. Spray gun maintenance
The spray gun is one of the most important parts of the electrophoretic equipment. Maintaining the spray gun can effectively prevent the problem of uneven coating. After each use, the spray gun should be cleaned in time to remove paint residues and avoid nozzle clogging. The nozzle of the spray gun needs to be checked regularly to ensure that it is not worn or blocked to ensure uniform spraying of the paint. In addition, the moving parts of the spray gun need to be lubricated regularly to ensure that the spraying process is smooth and unobstructed to avoid uneven spraying or poor coating quality.
2. Mechanical system inspection
The stable operation of the mechanical system and automatic control system of the electrophoretic equipment is crucial to ensure the coating effect. Regularly check whether the mechanical transmission system is running smoothly to avoid abnormal noise or vibration. If a problem is found in the drive system, it should be adjusted or replaced immediately. At the same time, the electrical system also needs to be checked regularly to ensure that all sensors, control panels, and cables are well connected. The automation system should be calibrated regularly to ensure its accuracy and reliability, to ensure the precise execution of the coating process.
3. Anti-corrosion
Anti-corrosion measures are an important part of the maintenance of electrophoretic equipment, especially in humid environments, where metal parts are prone to corrosion. To prevent parts from rusting, anti-rust oil or anti-corrosion coating can be applied regularly to metal parts prone to corrosion to enhance their durability. The humidity and temperature of the environment where the equipment is located should also be properly controlled to avoid excessive moisture that accelerates the corrosion process. Check the corrosion of metal parts regularly, and deal with signs of corrosion promptly to prevent it from affecting the overall performance of the equipment.
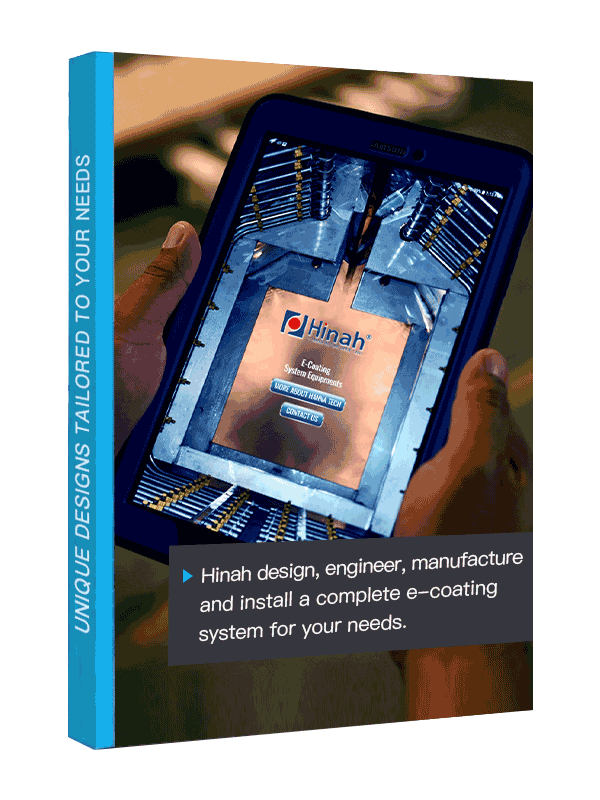
Let's Have A Chat
Get An E-coating Line Planning !
Match Your Products, Get The Solution & Price..
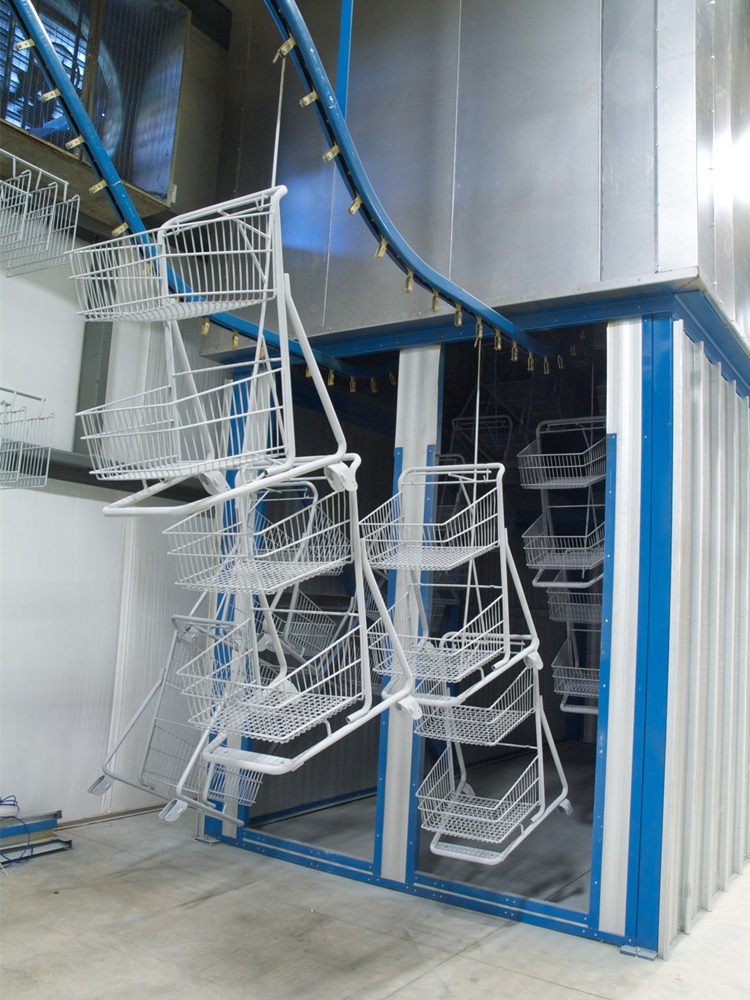
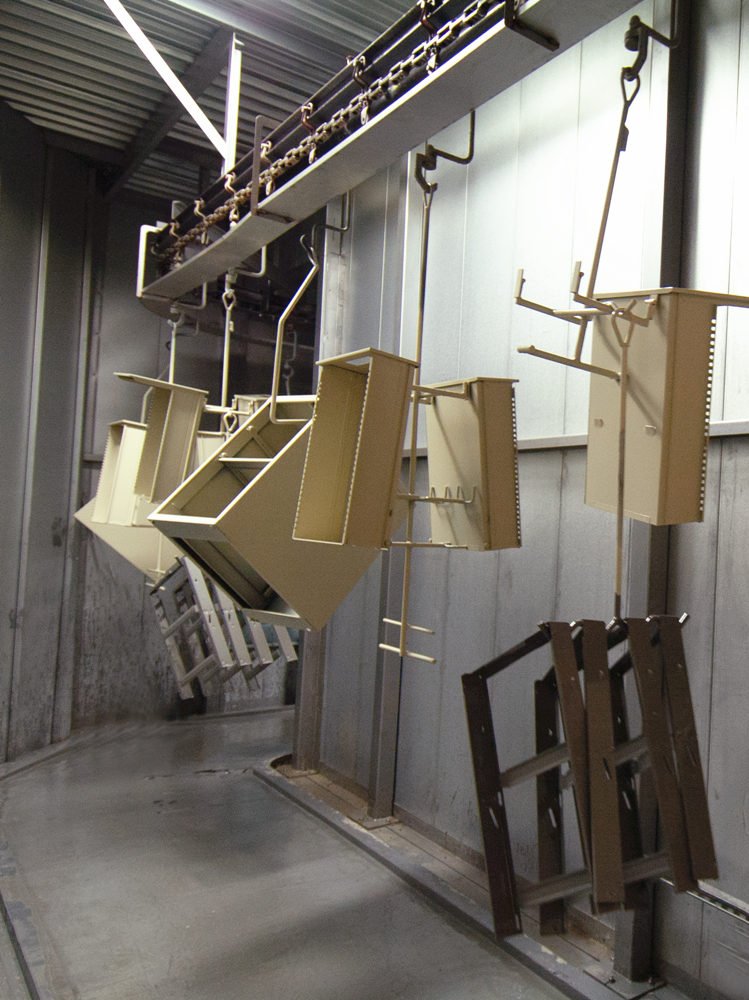
IV. Training of electrophoresis equipment operators
Ensuring that electrophoresis equipment operators are familiar with the correct operating procedures and emergency plans is the basis for the smooth operation of the equipment. Operators should receive systematic training, master the correct operation methods of the equipment, be familiar with common troubleshooting procedures, and be able to respond to emergencies to ensure the continuity and safety of production. At the same time, enterprises should also conduct regular skill improvement training to continuously improve the professional capabilities of operators and reduce equipment failures and downtime caused by improper operation. Through continuous training and management, not only can the operator’s work efficiency be improved, but also the risk of equipment maintenance and production interruption can be reduced, ensuring the long-term stable operation of the equipment.
V. Conclusion
Regular maintenance of electrophoresis equipment is essential to ensure coating quality, improve production efficiency, and extend the service life of equipment. By regularly cleaning and inspecting the equipment, maintaining the stability of the coating solution, and performing mechanical maintenance and anti-corrosion treatment on time, failures and downtime can be effectively reduced. In addition, continuous training of operators to ensure that they master the correct operating procedures and emergency plans can not only improve production efficiency but also reduce equipment damage caused by improper operation. Through comprehensive maintenance and management measures, companies can maximize the performance and life cycle of electrophoresis equipment and ensure the smooth progress of the production process.