In manufacturing, the right surface coating isn’t just about aesthetics—it’s a critical defense against corrosion, wear, and environmental damage. Yet, with options like e coating and powder coating dominating the market, choosing the ideal solution can feel overwhelming. Both technologies promise durability and efficiency, but their applications, costs, and environmental footprints differ significantly.
Is your priority seamless coverage for intricate metal parts, or vibrant colors for outdoor structures? Do sustainability mandates or production costs weigh heavier in your decision? This article cuts through the complexity, comparing e coating vs powder coating head-to-head, so you can invest in a finish that aligns with your industry needs, budget, and long-term goals. Let’s dive in.
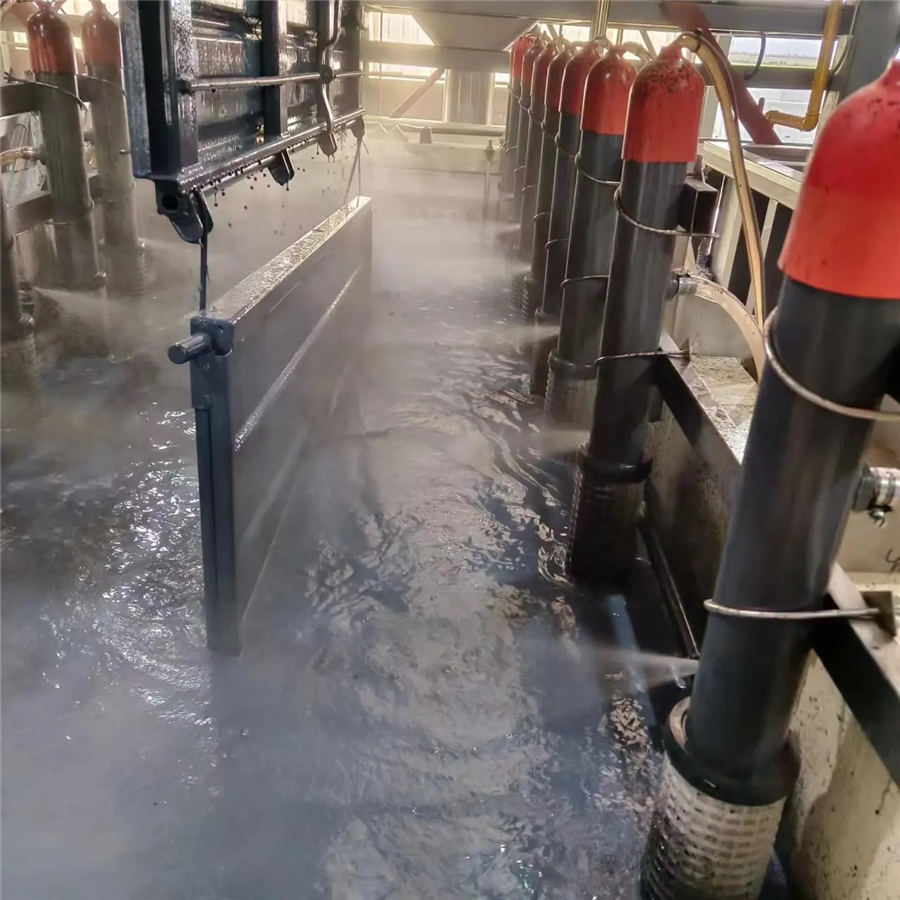
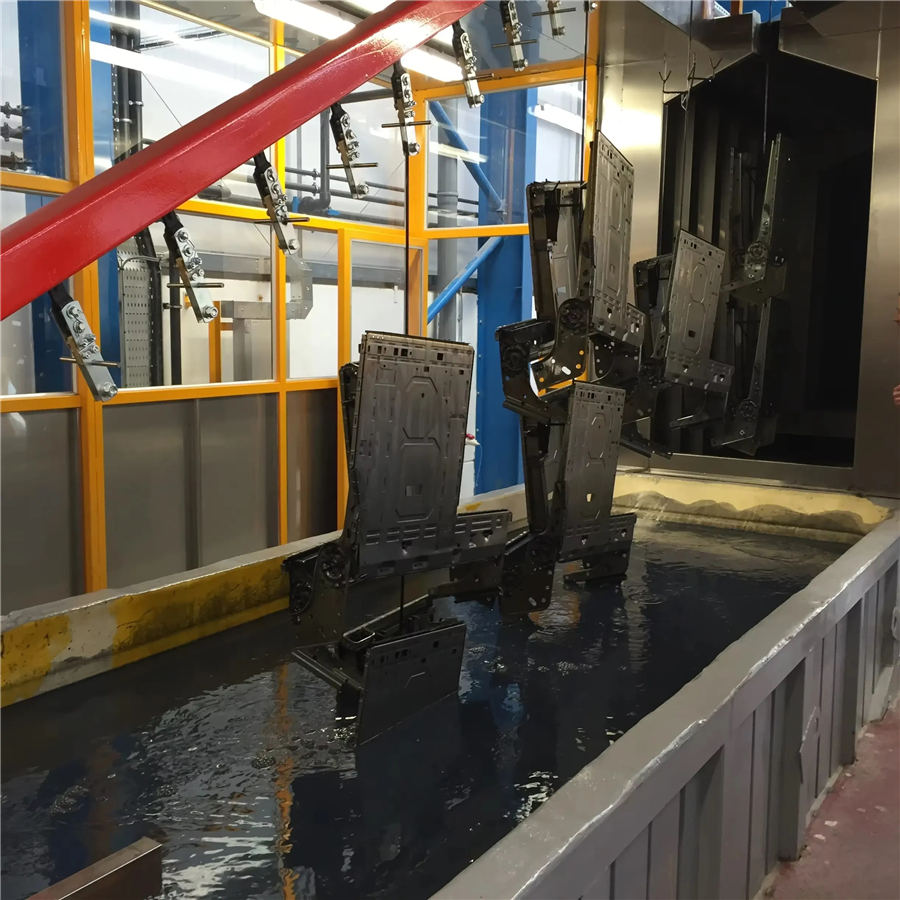
A Deep Dive into Electrophoretic Coating
E-coating (electrophoretic coating) is a cutting-edge finishing process that uses electrical currents to deposit paint uniformly onto metal surfaces. By immersing a workpiece in a water-based paint bath and applying voltage, charged paint particles migrate and bond tightly to the substrate, creating a seamless, corrosion-resistant layer—even on complex geometries.
Industry Applications
- Automotive: Engine parts, chassis, and fasteners rely on e-coating for rust protection.
- Consumer Electronics: Smartphone brackets, circuit board shields.
- Medical Devices: Sterile, durable finishes for surgical tools.
E Coating’s Edge
If your project demands flawless protection for complex shapes or strict environmental compliance, this technology is a game-changer.
Next, we’ll explore its rival: powder coating.
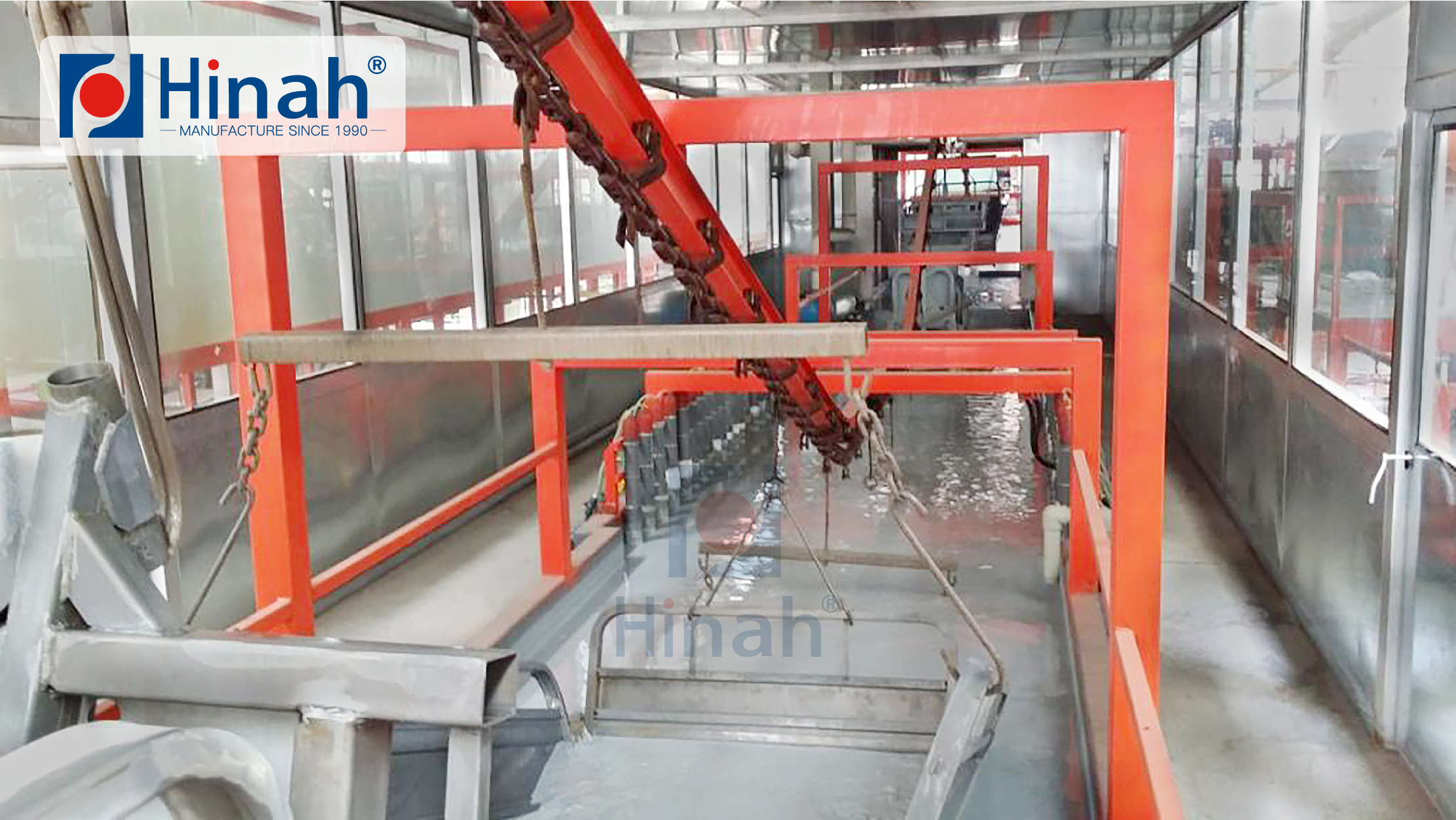
Exploring the Dry Finishing – Powder Coating Process
Powder Coating is a high-performance surface finishing method that bonds dry, free-flowing polymer powder to metal substrates through electrostatic attraction. Unlike liquid paints, this solvent-free process skips harmful emissions and delivers a thick, uniform layer of color and protection in a single step.
Industry Applications
- Architecture: Window frames, aluminum facades, and steel beams.
- Consumer Goods: Appliances (refrigerators, washing machines), lighting fixtures.
- Agriculture: Machinery parts exposed to harsh weather and abrasion.
Powder Coating’s Strength
Ideal for projects prioritizing bold aesthetics, heavy-duty protection, and rapid turnaround.
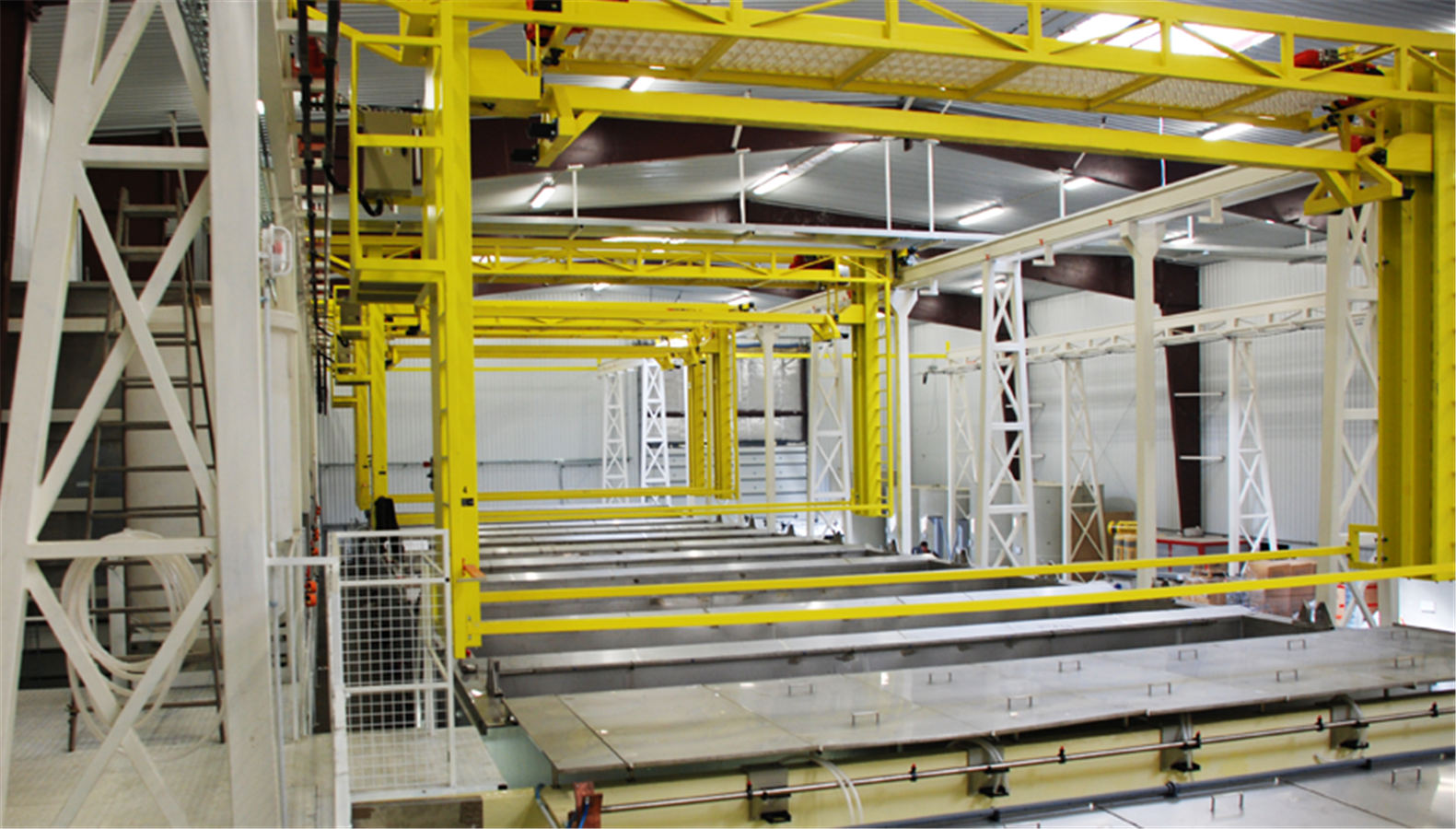
E Coating vs Powder Coating: Key Differences Compared
Choosing between e coating and powder coating hinges on understanding their core distinctions in process, performance, and practicality. Here’s a breakdown to clarify which technology aligns with your needs:
1. Process Comparison
E Coating Line
- Liquid-based: Electrochemical deposition from a waterborne paint bath.
- Requires immersion in an e-coating tank, enabling full coverage of complex shapes (e.g., crevices, internal channels).
- Multi-stage curing: Rinsing, baking, and post-treatment often needed.
Powder Coating Line
- Dry application: Electrostatic coating of free-flowing polymer powder.
- Applied via powder coating gun, limited by “Faraday cage effect” (powder struggles to reach deep recesses).
- Single-step curing: Powder melts into a continuous film during oven heating.
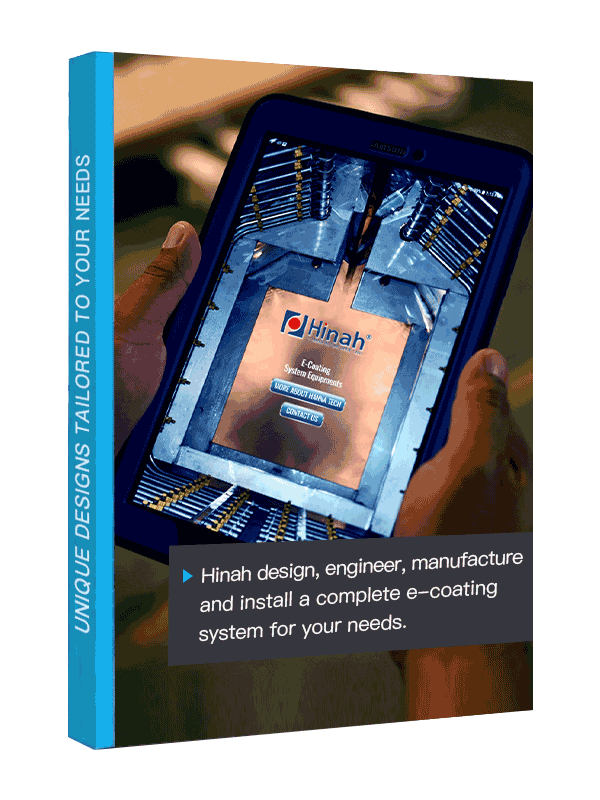
Let's Have A Chat
Get An E-coating Line Planning !
Match Your Products, Get The Solution & Price..
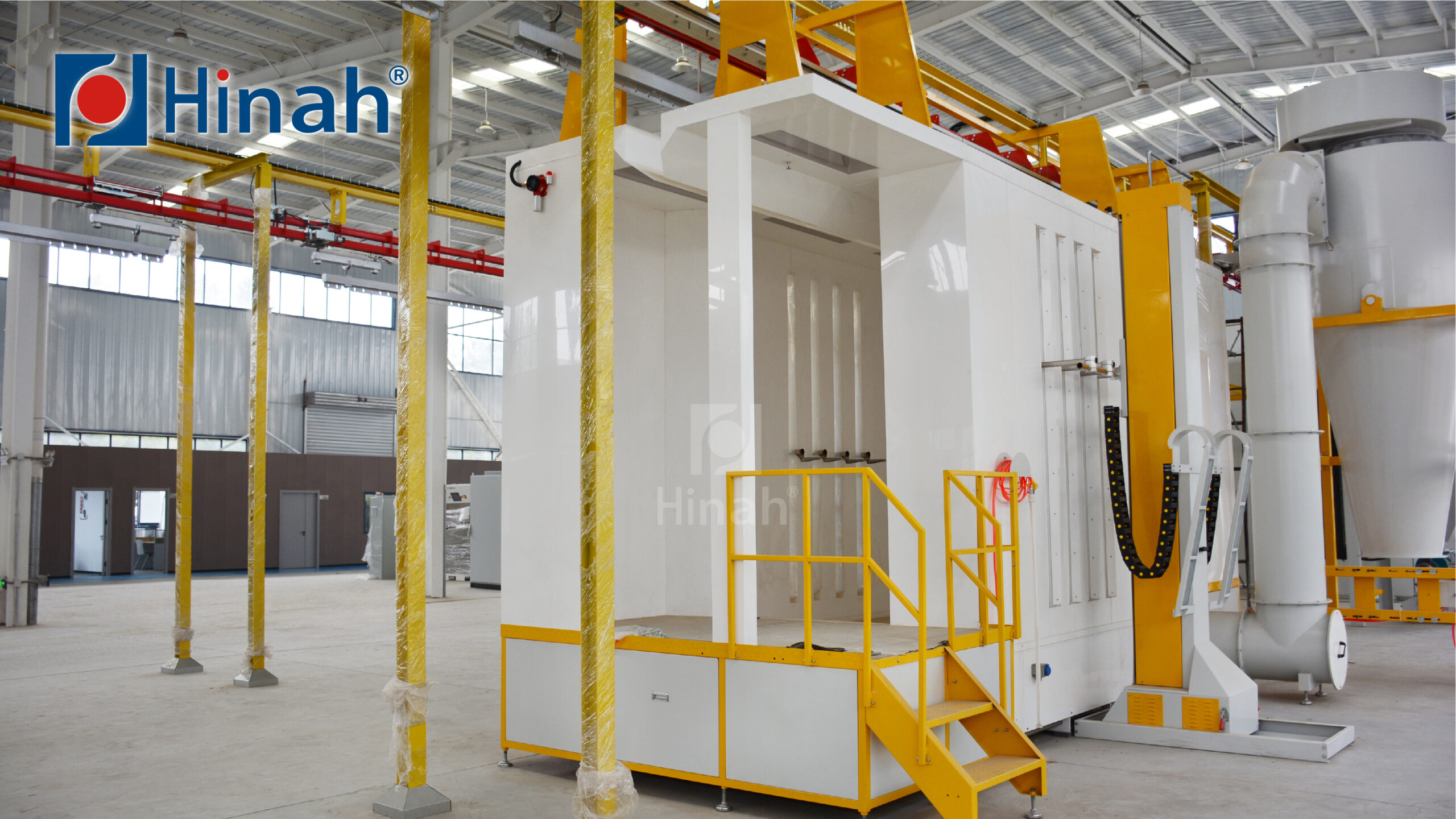
2. Performance Showdown
Coating Performance | E Coating | Powder Coating |
Corrosion Resistance | Penetrates microscopic pores, creating a chemically bonded layer ideal for rust-prone environments (e.g., marine hardware, undercarriages). | Forms a thicker, physical barrier against abrasion and UV rays, better suited for outdoor exposure (fences, agricultural machinery). |
Aesthetic Flexibility | Limited to thin, smooth finishes in muted colors (typically black or gray). | Offers bold colors, textures (matte, glossy, wrinkled), and custom metallic effects. |
Durability | Prone to chipping if uncured properly but resists salt spray and chemicals. | Highly impact-resistant but may fade under prolonged UV exposure. |
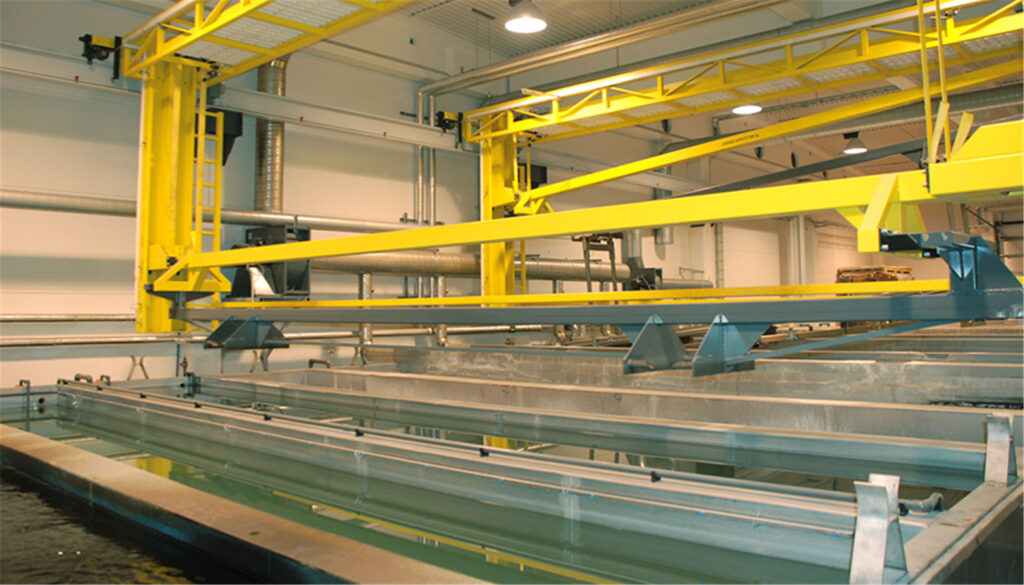
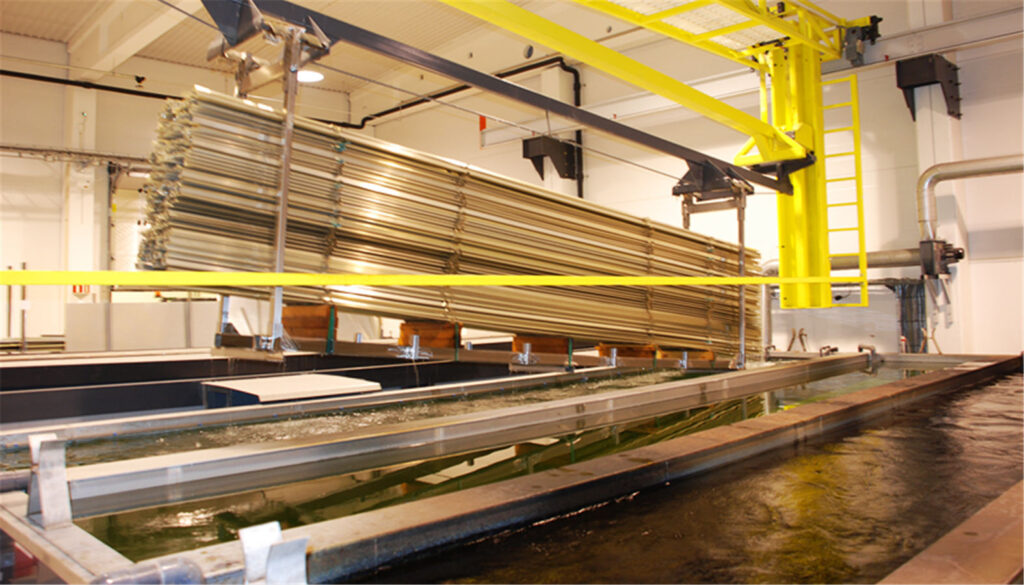
Cost Analysis: E Coating vs Powder Coating
Understanding the financial implications of e coating vs powder coating requires a holistic view of both upfront investments and long-term operational efficiency.
Initial Investment
E coating line typically demands higher initial capital due to specialized equipment like immersion tanks, rectifiers, and advanced filtration systems. These systems require precise chemical control and significant floor space, making the setup ideal for large-scale manufacturers focused on high-volume production—think automotive assembly lines or industrial component suppliers. In contrast, powder coating line offers a lower entry barrier. Its core equipment—spray guns, compact curing ovens, and powder recovery units—suits smaller workshops or businesses prioritizing flexibility. The simpler pretreatment process (often just sandblasting) further reduces setup complexity and space requirements.
Long-Term Operational Costs
While e coating line boasts 90–95% paint utilization rates (minimizing overspray waste), it incurs ongoing expenses for wastewater treatment, pH-balancing chemicals, and sludge disposal. Labor costs also add up, as technicians must monitor bath chemistry and manage environmental compliance. Powder coating line, however, operates with near-zero waste—95–99% of unused powder is recycled—and avoids liquid waste entirely. Though its curing ovens consume more energy (heating to 200°C vs e-coating line’s 150°C), automated coating systems slash labor needs, especially for mass production.