In the coating industry, a-coating and e-coating are two common coating technologies, which have been widely used in many fields such as automobile manufacturing, home appliances, and industrial equipment. With the increasingly stringent environmental protection standards, electrophoretic coating (e-coating) has gradually gained favor due to its excellent environmental performance and corrosion resistance. However, traditional a-coating technology still occupies a place with its cost-effectiveness and high adaptability. Faced with the different characteristics and advantages of the two coating technologies, many companies are often confused when choosing: Which coating method is more suitable for their production needs?
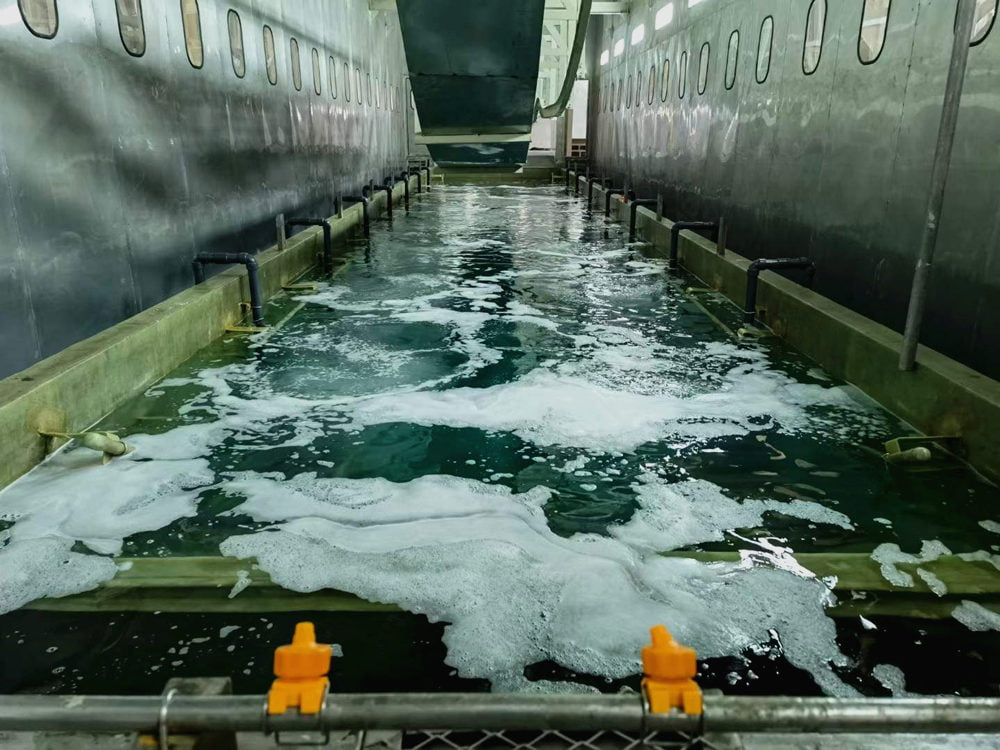
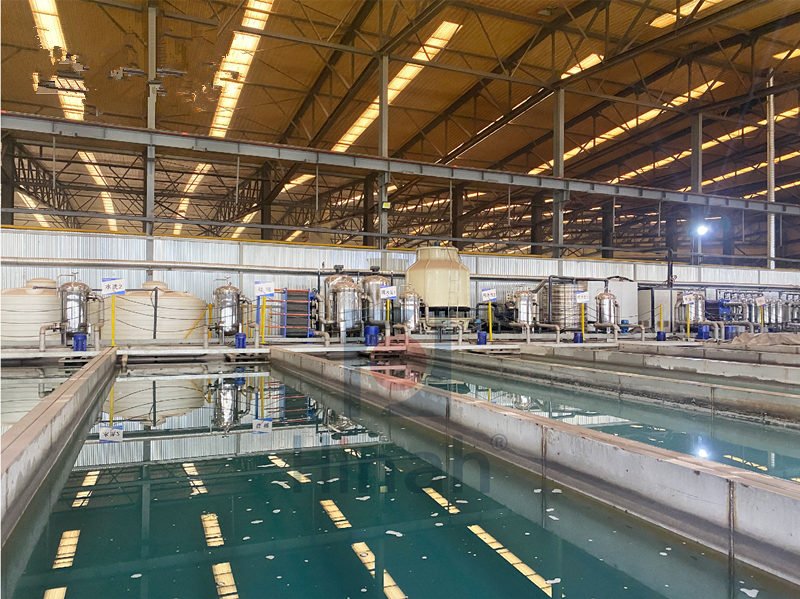
I. Basic Overview of A-Coating and E-Coating
A-coating (usually refers to traditional coating technology) and e-coating (electrocoating) are two major coating processes, each with different characteristics and applicable scenarios.
A-coating, as a traditional coating method, usually sprays powder coating onto the surface of the workpiece through a spray gun, using electrostatic adsorption to make the coating evenly adhere to the surface of the object. Then it is cured by heating to form a solid coating. The advantage of a-coating technology is that the equipment investment is relatively low and it is suitable for parts of various shapes. It is widely used in the coating of metal, plastic and other surfaces.
E-coating, or electrophoretic coating, is a technology that deposits coating on the surface of a workpiece through an electrochemical process. In the e-coating process, the workpiece is usually placed in an electrolytic cell containing a coating solution as a cathode or anode, and the coating particles are evenly deposited on the surface through an electric current. This technology can produce a uniform and corrosion-resistant coating, which is particularly suitable for industries such as automobiles and home appliances that require long-term durability and environmental protection.
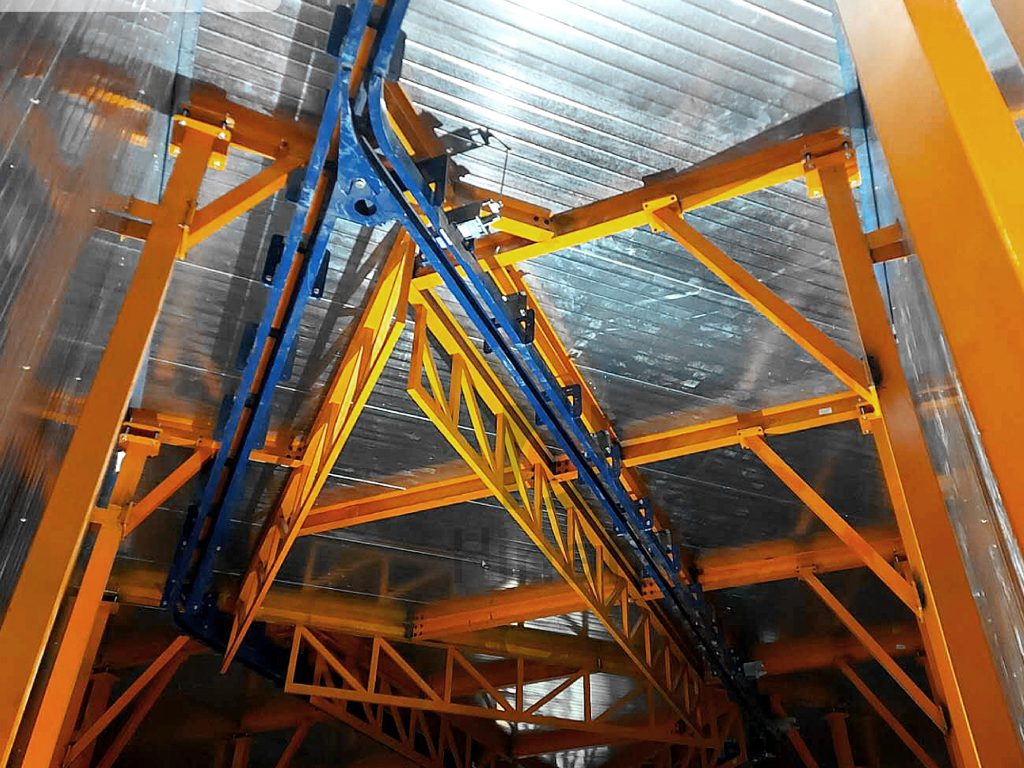
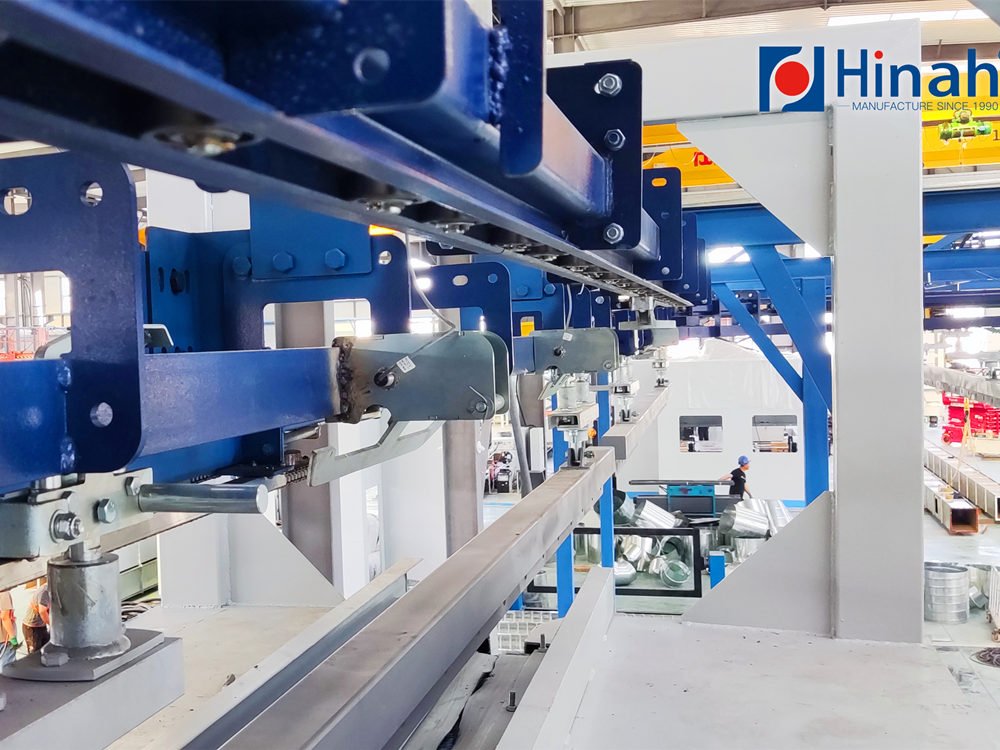
II. The Main Difference Between A-Coating and E-Coating
Although both a-coating and e-coating are coating technologies, they have significant differences in many aspects.
1. Process flow
A-coating usually uses electrostatic spraying or airflow spraying to evenly spray powder or liquid coating onto the surface of an object. The sprayed coating is cured by heating to form a solid coating. The whole process is relatively simple and flexible to operate.
Electrocoating uses an electrochemical process to deposit charged coating particles on the surface of the workpiece through an electric current. The workpiece is placed in the coating solution as one of the electrodes, and the current causes the coating to be deposited evenly. Electrophoretic coating can more accurately control the coating thickness and has better coating uniformity.
2. Coating performance
The sprayed a-coating usually has strong wear resistance, good aesthetics and good covering ability, and is suitable for general corrosion protection. However, it is slightly inferior in terms of corrosion resistance and durability in extreme environments.
E-coating usually havs stronger corrosion resistance, high temperature resistance and chemical resistance, and is suitable for environments that require long-term durability, especially in the fields of automobiles and home appliances. Its coating is uniform, has strong adhesion, and is environmentally friendly.
3. Application fields
Due to its simple process and low cost, a-coating is widely used in the fields of home appliances, furniture, mechanical parts, and auto parts. It is suitable for mass production, especially in milder environments, and can provide effective surface protection.
E-coating technology is particularly suitable for automobiles, heavy equipment, home appliances, etc. due to its excellent anti-corrosion performance. It performs particularly well in occasions that require long-term durability and high anti-corrosion requirements (such as automobile chassis, automobile engine parts, etc.).
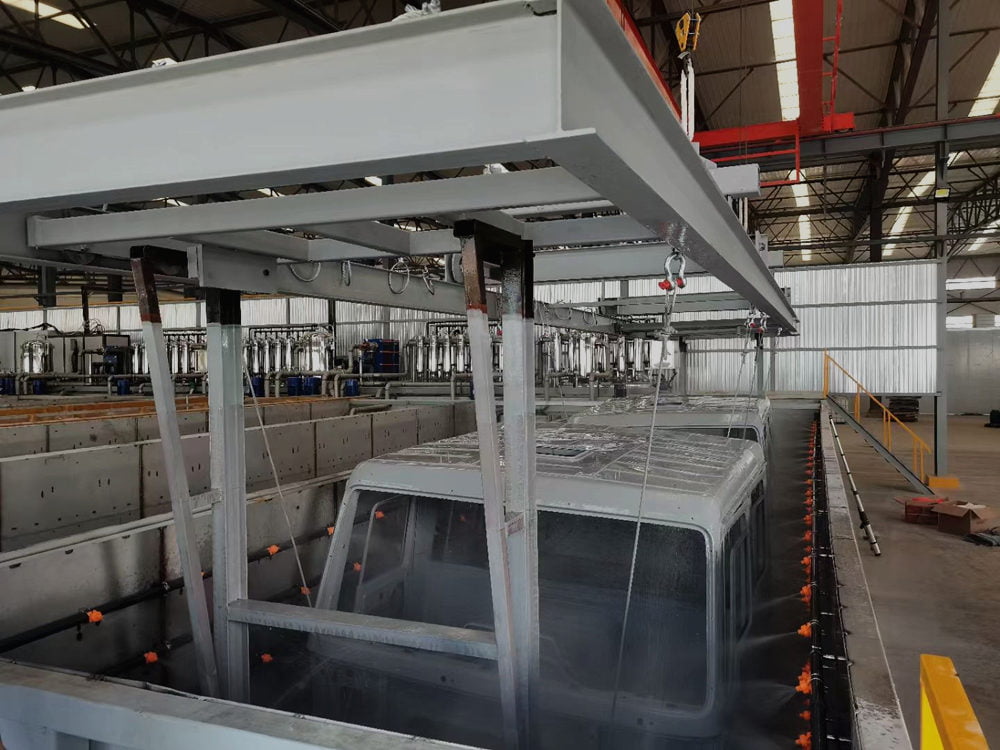
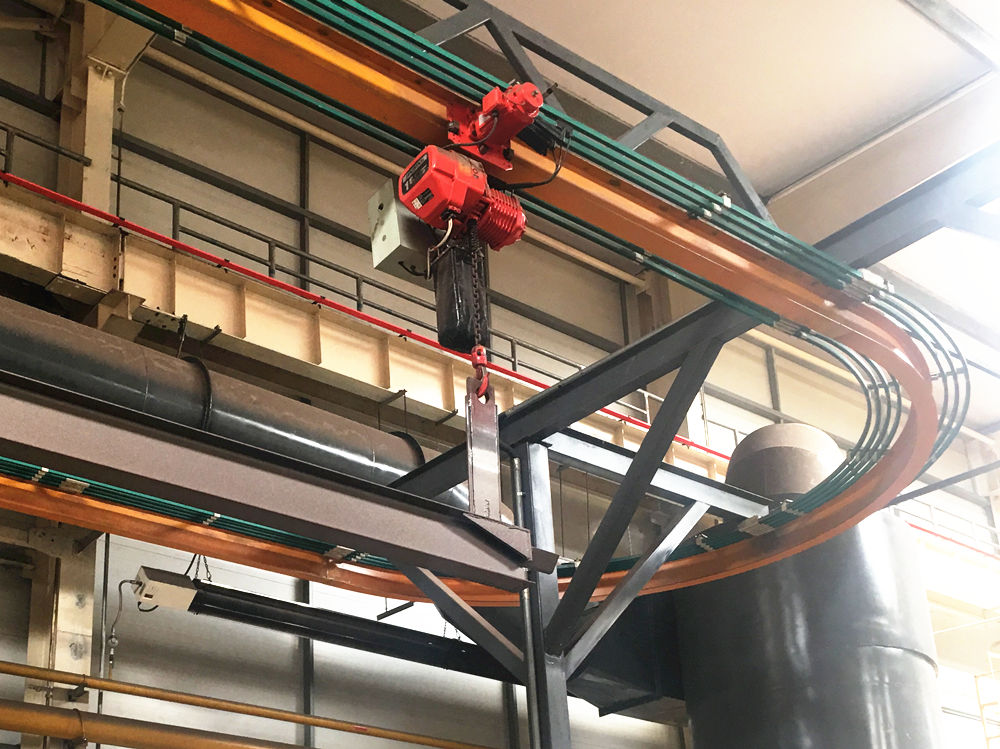
III. Advantages and limitations of A-Coating
As a traditional coating technology, a-coating has been widely used in many industries due to its unique advantages. However, it also has some limitations that need to be considered when making actual choices.
Advantages of A-Coating
1. Cost-effectiveness
A-coating has relatively low equipment investment, simple process, and is suitable for mass production, so the overall production cost is relatively economical. It is especially suitable for small enterprises with limited budgets or application scenarios that require fast and efficient production. The flexibility of the spraying process and low operating costs make it popular in many industries.
2. Process flexibility
A-coating technology is very adaptable and can be applied to workpieces of various shapes and sizes, and can even coat some complex geometries. Spraying technology allows high operational flexibility and can adjust the coating thickness and effect according to demand. For the coating of some small and medium-sized parts, a-coating is a very suitable choice.
3. Fast production cycle
Compared with other coating methods, a-coating has a shorter production cycle and can complete the application and curing of the coating in a shorter time. This makes it particularly suitable for large-scale production and can effectively improve production efficiency.
Limitations of A-Coating
1. Poor coating uniformity
Although a-coating can provide strong adhesion, due to the limitations of its spraying method, the uniformity of the coating is sometimes difficult to fully guarantee. Especially in the coating of some small and complex parts, uneven coating thickness or missing coating may occur.
2. Environmental protection issues
The spray coating used by a-coating is usually solvent-based, which may release volatile organic compounds (VOCs), causing certain harm to the environment and the health of operators. Although there are improved technologies to reduce VOC emissions, there are still challenges in environmental compliance, especially in some countries and regions with strict environmental protection requirements.
3. Weak corrosion resistance
Compared with e-coating, a-coating has poor corrosion resistance, especially in harsh environments such as humidity and chemical erosion, the coating is easily damaged. Therefore, a-coating is generally not suitable for application scenarios that require extremely high corrosion resistance.
4. Difficulty in controlling coating thickness
Since a-coating is applied by spraying, it is difficult to accurately control the thickness of the coating. This can result in a coating that is too thin and does not provide adequate protection, or too thick and affects the appearance and performance of the product.
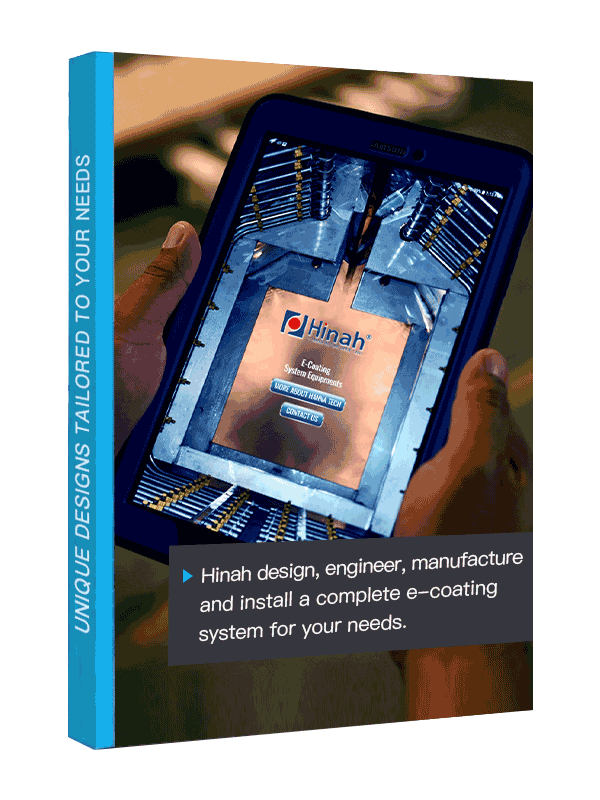
Let's Have A Chat
Get An E-coating Line Planning !
Match Your Products, Get The Solution & Price..
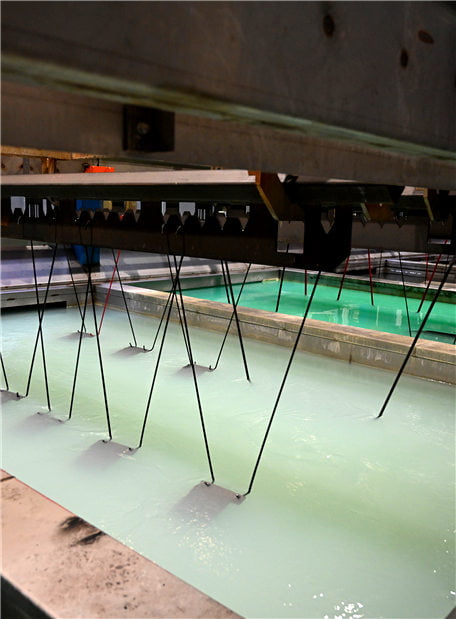
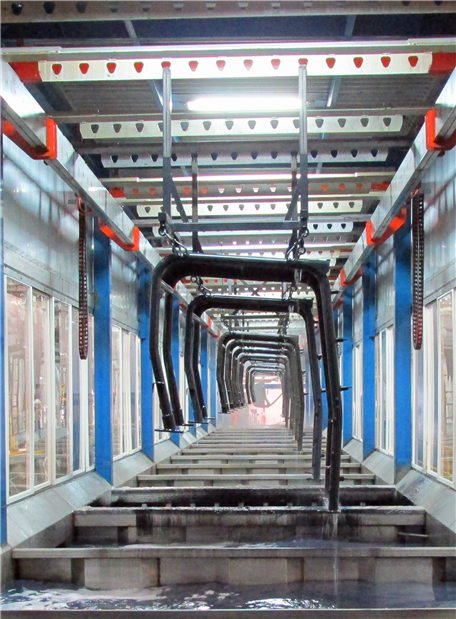
IV. Advantages and limitations of E-Coating
E-coating, as an advanced coating technology, has gradually become the first choice for many high-demand industries with its excellent coating performance and environmental advantages. However, it also has certain limitations, and various factors need to be considered comprehensively when choosing.
Advantages of E-Coating
1. Excellent environmental protection
Electrocoating uses water-based paint, and the waste and solvent emissions of the paint are low, which meets strict environmental standards. Compared with traditional solvent-based paints, e-coating produces almost no volatile organic compounds (VOCs), so it has a small burden on the environment and can help companies meet increasingly stringent environmental regulations.
2. Excellent corrosion resistance
E-coating can form a uniform and dense protective layer in the coating, and has excellent corrosion resistance. It is particularly suitable for products that require long-term durability, such as automobiles and home appliances, and can effectively prevent oxidation and corrosion of metal surfaces and extend the service life of products.
3. Coating uniformity and adhesion
Since the paint is evenly deposited under the action of the electric field during the electrophoretic coating process, the coating uniformity of e-coating is extremely high, and there is almost no leakage. This highly uniform coating can ensure the integrity of surface protection, and at the same time has excellent adhesion and is not easy to peel off, which improves the durability and wear resistance of the product.
4. Excellent high temperature resistance
Electrocoating has good high temperature resistance, can maintain the stability of the coating in a high temperature environment, and is not easily affected by temperature changes. Therefore, e-coating is widely used in products that need to withstand high temperature environments, such as automotive engine parts and home appliance housings.
Limitations of E-Coating
1. High initial equipment investment
Compared with a-coating, the initial equipment investment of electrocoating is more expensive. Electrophoretic tanks, current control systems, drying equipment, etc. all require a large capital investment, and for small and medium-sized enterprises, they may require a higher initial cost. This is a major challenge in its application and promotion.
2. High requirements for pre-treatment of coating
E-coating has high requirements for the surface treatment of workpieces. It must ensure that the surface is clean and oil-free, otherwise it will affect the adhesion and uniformity of the coating. The pre-treatment process is relatively cumbersome, which increases the complexity of the production process, especially when dealing with complex shapes or difficult-to-clean workpieces, which may require more time and cost.
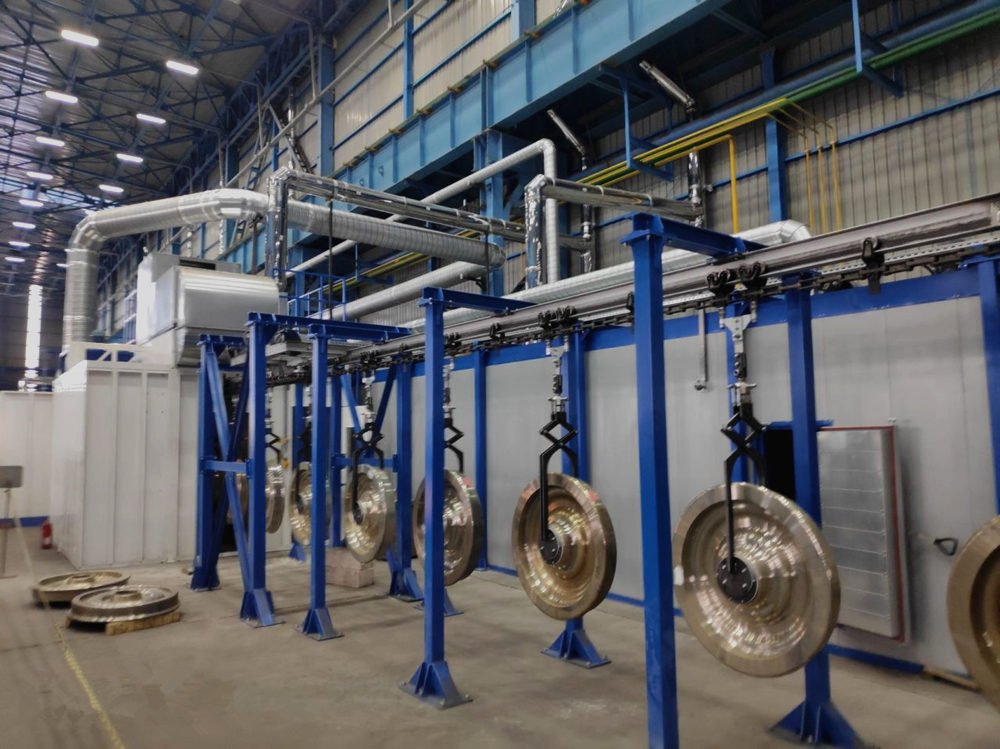
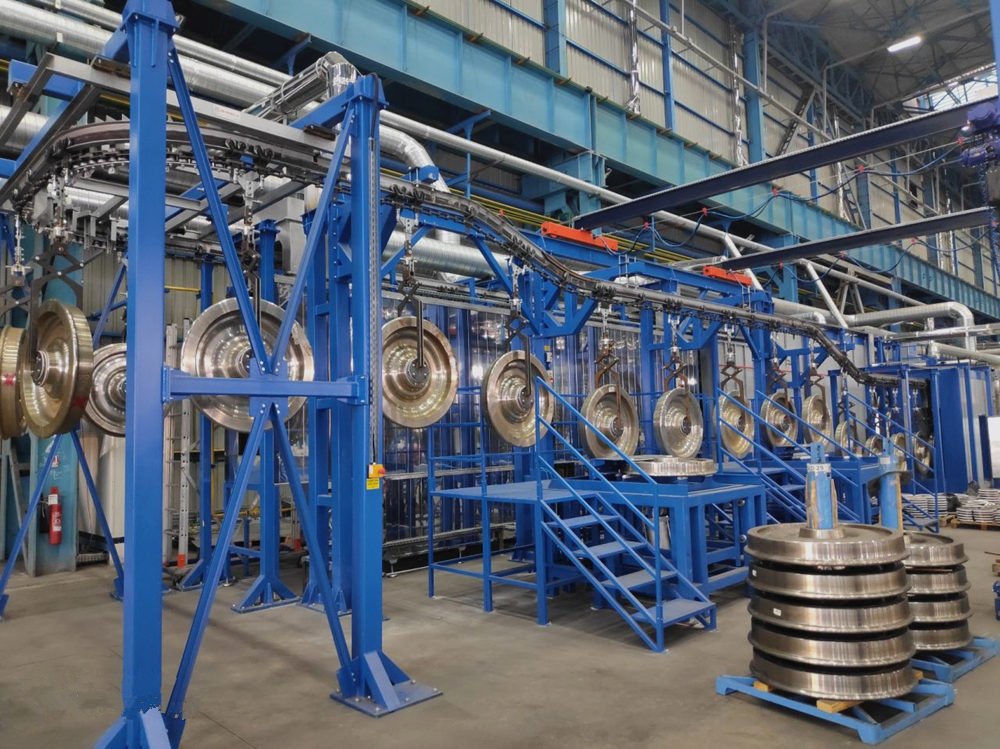
V. Which coating technology is more suitable?
Depending on your needs, choosing a-coating or e-coating depends on several key factors. If you are cost-sensitive, have a large production volume, and do not require high corrosion resistance of the coating, a-coating is an economical and practical choice. On the other hand, if you need higher coating quality, environmental protection and corrosion resistance, and can accept higher equipment investment, electrocoating is more suitable, especially for high-demand industries such as automotive and heavy equipment manufacturing.