In the e-coating line, traditional electrocoating conveyor systems often require frequent maintenance due to mechanical wear, contamination, and operational inefficiencies. It faces many challenges,such as component misalignment, dirt build-up, and downtime for repairs. However, the advent of maintenance-free electrocoating conveyor eliminates these challenges.
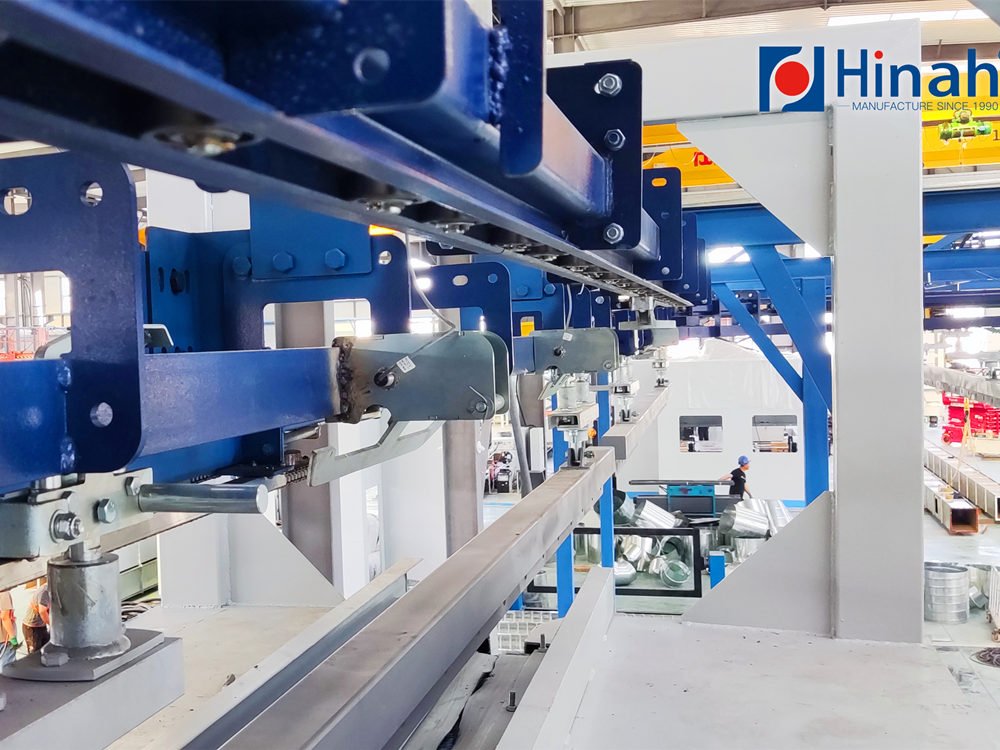
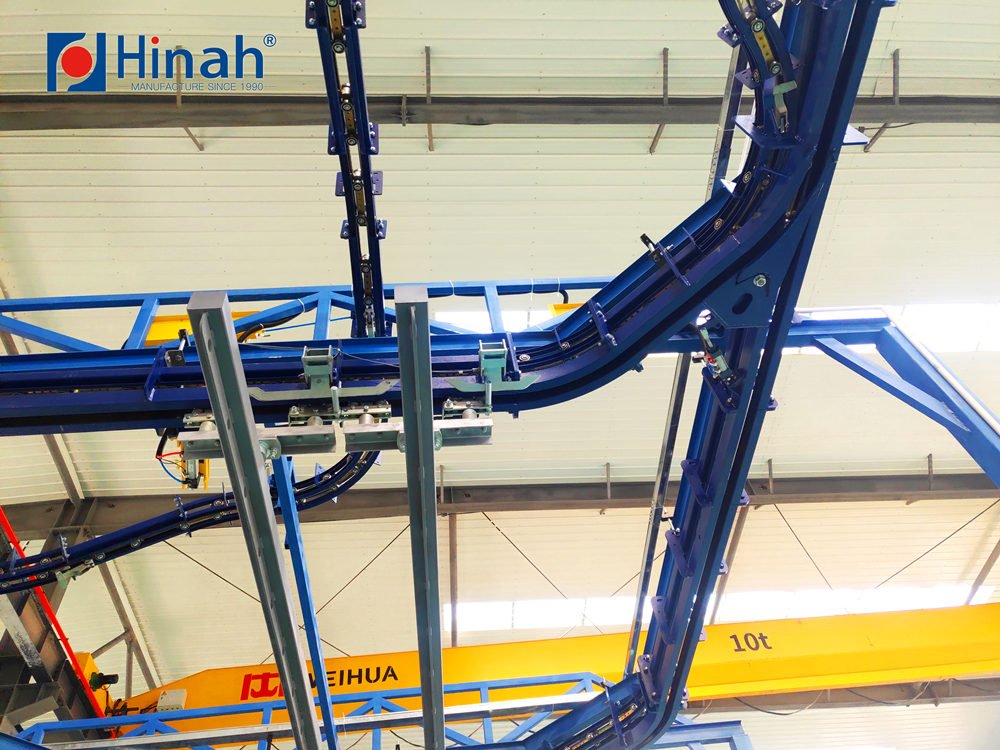
1. Overview of Electrocoating Conveyor
Electrocoating, or e-coating, is a process that involves the application of a protective coating to metal parts using an electrically charged bath. This method ensures uniform coverage, corrosion resistance, and durability. To facilitate the movement of parts through the various stages of electrocoating—pre-treatment, coating, curing, and drying—a specialized conveyor system is essential.
Key Components of an Electrocoating Conveyor
- Conveyor Tracks and Chains – These components transport metal parts through the different electrocoating stages. They must be resistant to chemicals and corrosion.
- Load Bars and Hangers – Used to hold and position parts for uniform coating, ensuring that each item receives even coverage.
- Drive System – Includes motors, gears, and tensioners that regulate the movement and speed of the conveyor to maintain process efficiency.
- Control Panel – Integrates with automated systems to manage conveyor speed, direction, and monitoring for optimal operation.
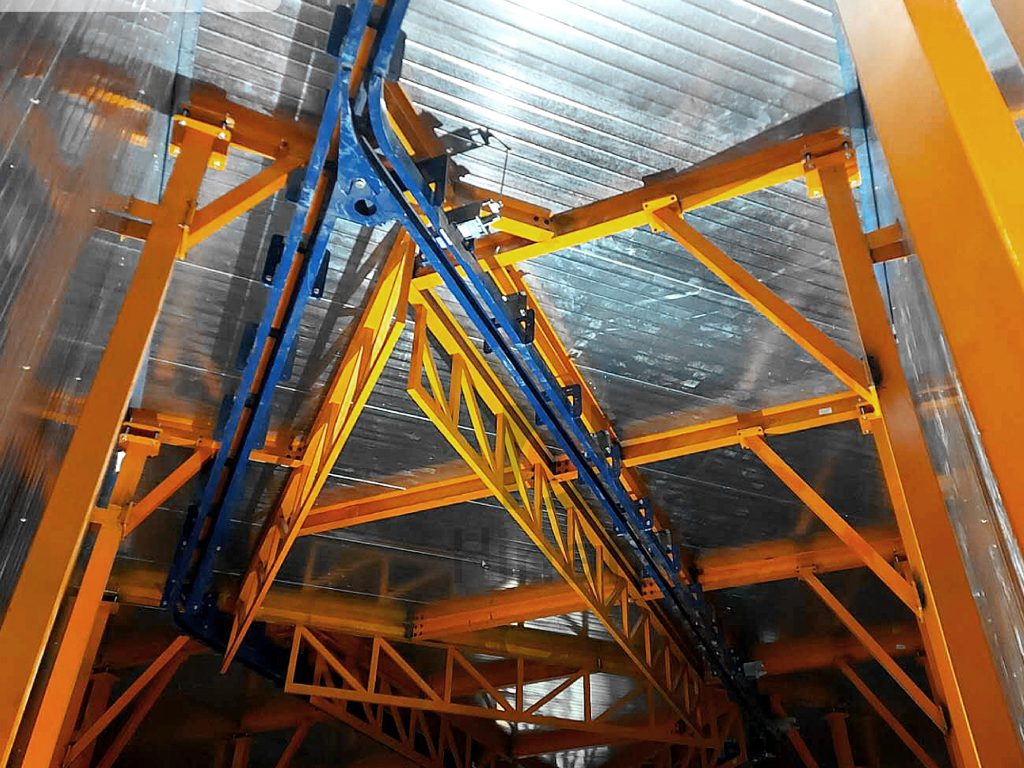
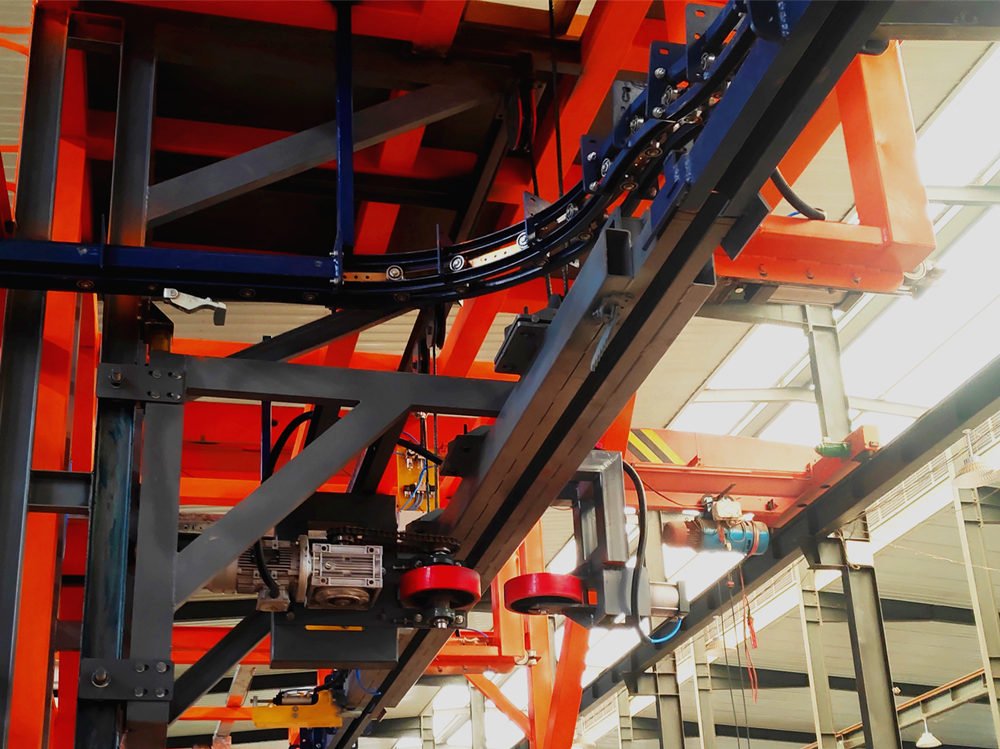
II. Why Choose theMaintenance-Free Electrocoating Conveyor
Maintenance-free electrophoresis conveyor systems avoid many of the challenges faced by traditional conveyors.
- Self-Lubricating Components – Advanced materials and coatings reduce the need for constant lubrication, extending component lifespan and minimizing manual maintenance.
- Corrosion-Resistant Materials – High-quality stainless steel, coated alloys, and composite materials ensure resistance to chemical exposure, reducing part replacement frequency.
- Automated Monitoring Systems – Smart sensors detect wear and misalignment in real-time, allowing for proactive adjustments without manual intervention.
- Self-Cleaning Mechanisms – Automated debris removal and wash systems keep the conveyor clean, reducing contamination risks and ensuring consistent coating quality.
- Extended Operational Lifespan – With fewer moving parts susceptible to wear and tear, maintenance-free systems operate longer with minimal downtime.
- Cost Savings – Reduced labor, repair, and downtime costs contribute to significant long-term savings, making maintenance-free electrocoating conveyors a cost-effective solution for manufacturers.
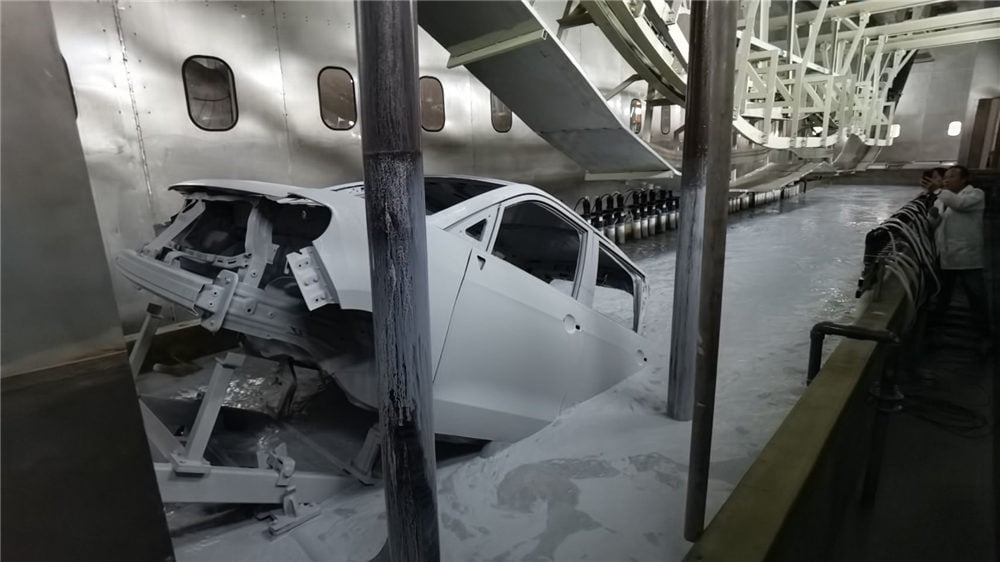
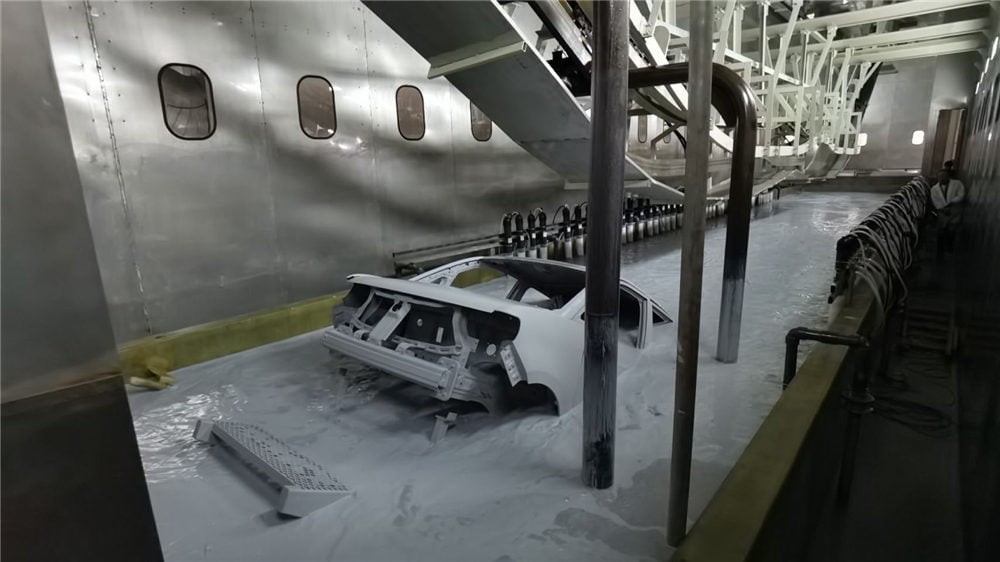
III. Key Features of a Maintenance-Free Electrocoating Conveyor
1. Advanced Materials and Design Innovations
Maintenance-free electrocoating conveyors leverage high-performance materials to enhance durability and reliability. Stainless steel alloys, polymer-coated components, and advanced composites reduce wear and eliminate the need for constant lubrication. Additionally, modular design features allow for easy component replacement, minimizing downtime and ensuring continuous operation.
2. Automation and Self-Cleaning Capabilities
Automation plays a crucial role in making electrocoating conveyors maintenance-free. Key automation features include:
- Automated Chain Tensioning – Reduces the need for manual adjustments and ensures optimal conveyor performance.
- Smart Monitoring Systems – Real-time data collection and predictive maintenance alerts help prevent unexpected failures.
- Self-Cleaning Tracks and Hangers – Integrated cleaning systems remove contaminants and debris, maintaining a smooth and consistent electrocoating process.
These automation features not only reduce labor costs but also improve process efficiency by minimizing interruptions due to maintenance requirements.
3. Energy Efficiency and Cost Savings
Energy efficiency is a key advantage of maintenance-free electrocoating conveyors. High-efficiency motors, regenerative braking systems, and optimized power usage contribute to lower energy consumption. Additionally, variable speed drives enable precise control over conveyor movement, reducing unnecessary power expenditure.
By eliminating frequent maintenance and repairs, manufacturers benefit from significant cost savings over time. Reduced downtime, fewer replacement parts, and improved operational efficiency make these conveyors a smart investment for any electrocoating facility.
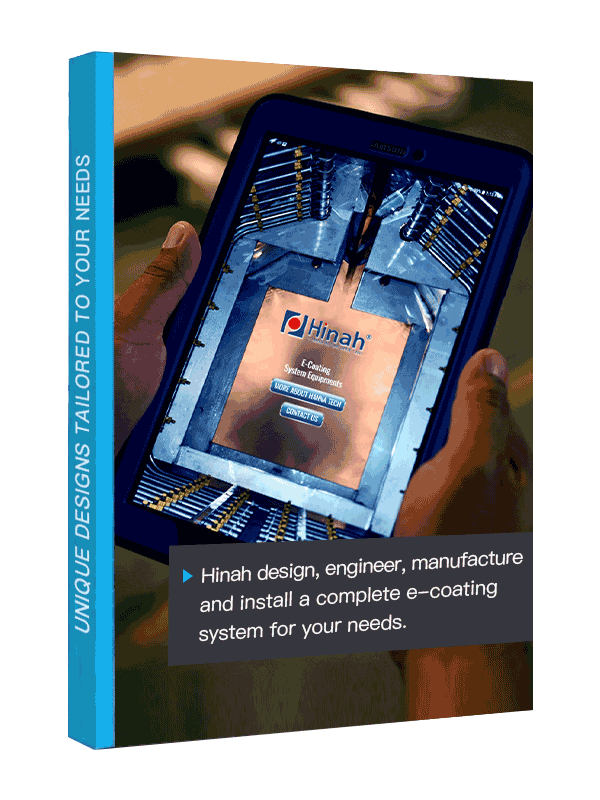
Let's Have A Chat
Get An E-coating Line Planning !
Match Your Products, Get The Solution & Price..
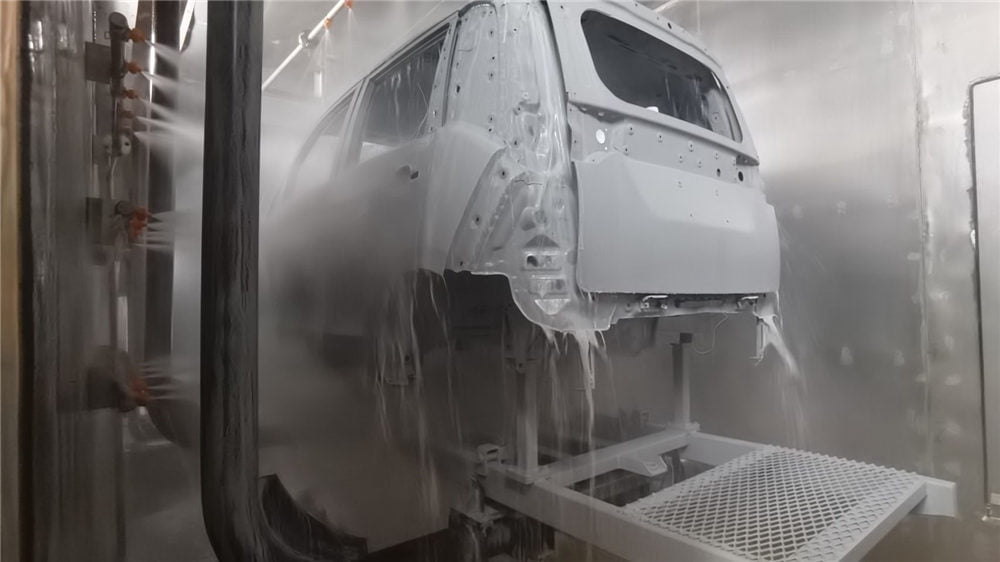

IV. How to Optimize Your Electrocoating Conveyor for Longevity
Best Practices for Installation and Operation
To maximize the lifespan and efficiency of a maintenance-free electrocoating conveyor, consider the following installation and operational best practices:
- Proper Alignment During Installation – Ensuring correct alignment of tracks and drive systems prevents premature wear and operational inefficiencies.
- Optimized Load Distribution – Distributing weight evenly across the conveyor minimizes strain on components and reduces mechanical stress.
- Environmental Control – Maintaining a clean and controlled environment around the conveyor system prevents contamination and prolongs system integrity.
- Regular System Calibration – Periodic checks on automated settings, such as chain tensioning and speed controls, enhance performance and longevity.
Strategies to Minimize Wear and Tear
- Use of Non-Abrasive Coatings – Applying specialized coatings to key components reduces friction and wear over time.
- Scheduled Preventive Inspections – While maintenance-free systems require minimal upkeep, periodic inspections can catch potential issues before they escalate.
- Temperature and Humidity Monitoring – Maintaining stable environmental conditions prevents material degradation and enhances conveyor performance.
- Training for Operators – Educating staff on proper handling and usage practices ensures that the conveyor operates within optimal parameters.
- By implementing these best practices and strategies, manufacturers can further extend the lifespan of their electrocoating conveyor systems while maintaining high productivity and efficiency.
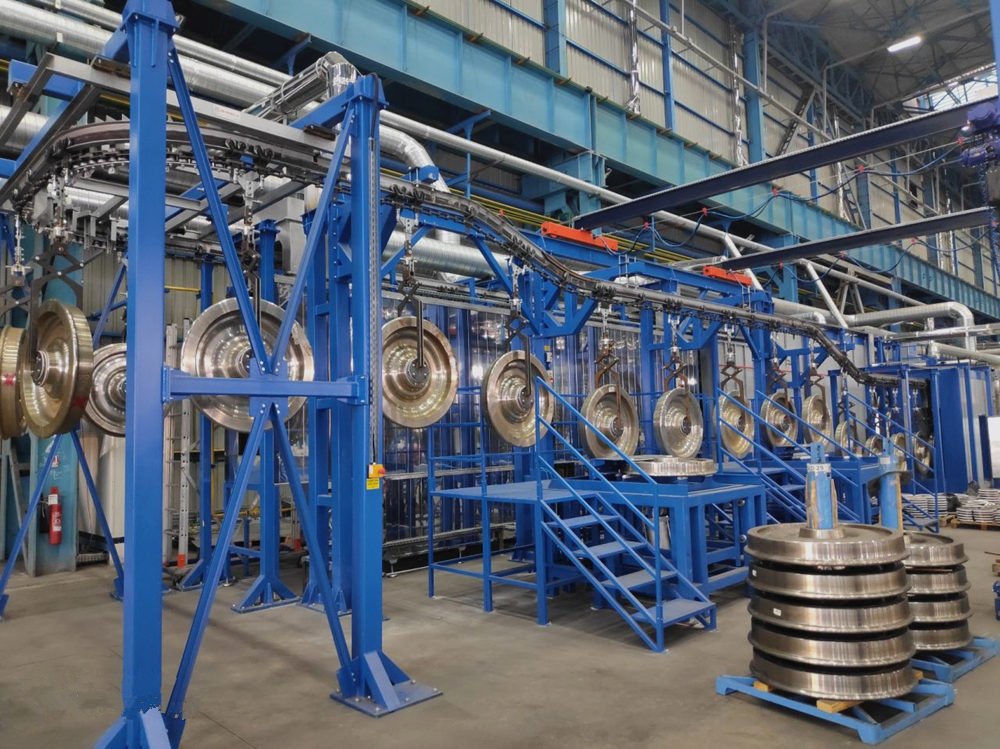
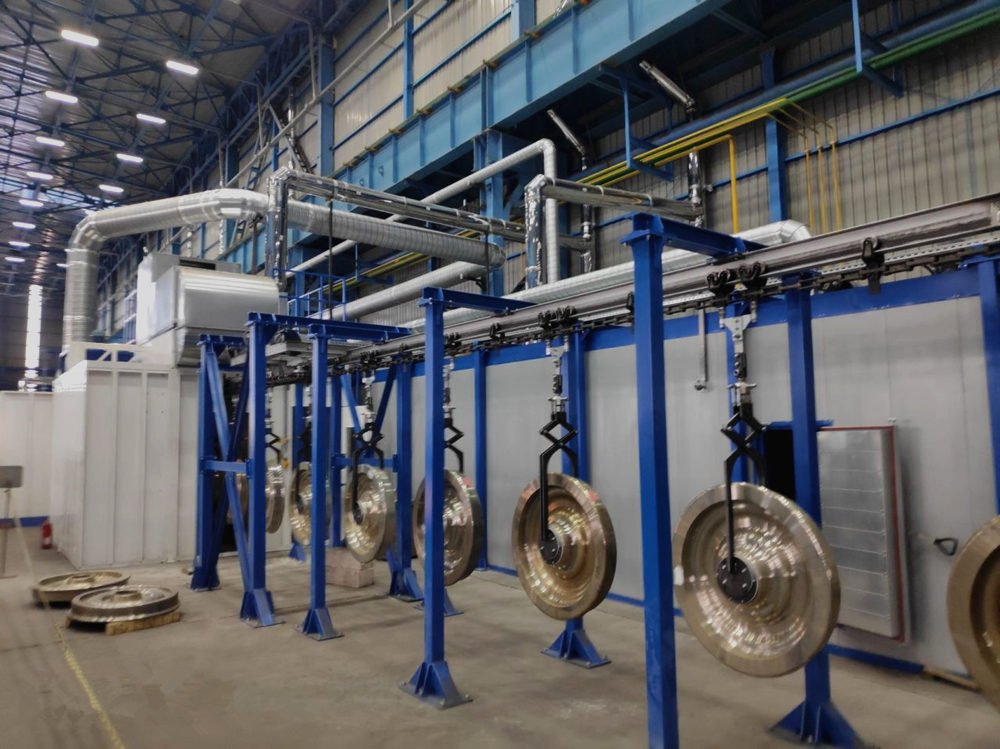
V. Conclusion
A maintenance-free electrocoating conveyor system is a game-changer for manufacturers seeking efficiency, reliability, and cost savings. By eliminating the frequent maintenance challenges of traditional conveyors, these advanced systems provide long-term durability and operational stability.
For manufacturers looking to enhance their electrocoating process, investing in a maintenance-free conveyor system is a strategic decision that improves productivity, ensures consistent coating quality, and ultimately maximizes profitability.