E-coating line is widely used in many industries. With excellent adhesion and corrosion resistance, it has become an important choice for metal surface protection. But to obtain high-quality coatings, the role of the pretreatment system is crucial. From decontamination and cleaning to surface activation, each step lays the foundation for the adhesion and uniformity of the coating. The precise control of pretreatment directly determines the final effect of coating, and any slight deviation may lead to coating defects.
So, why is the pretreatment system so important in e-coating lines?
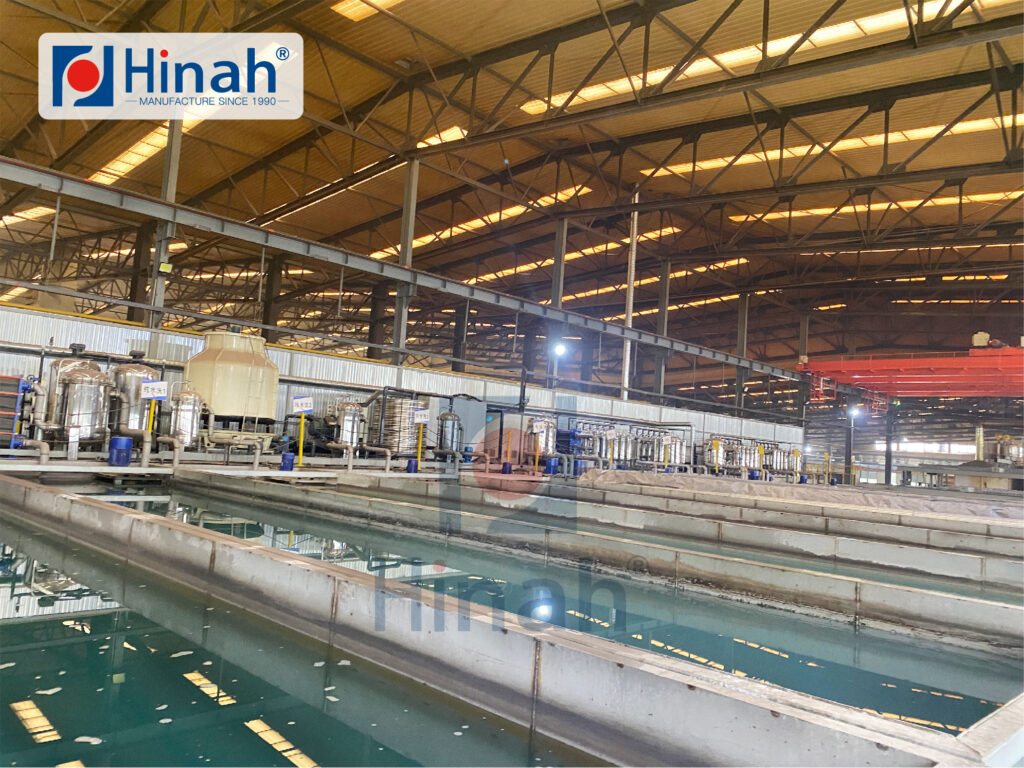
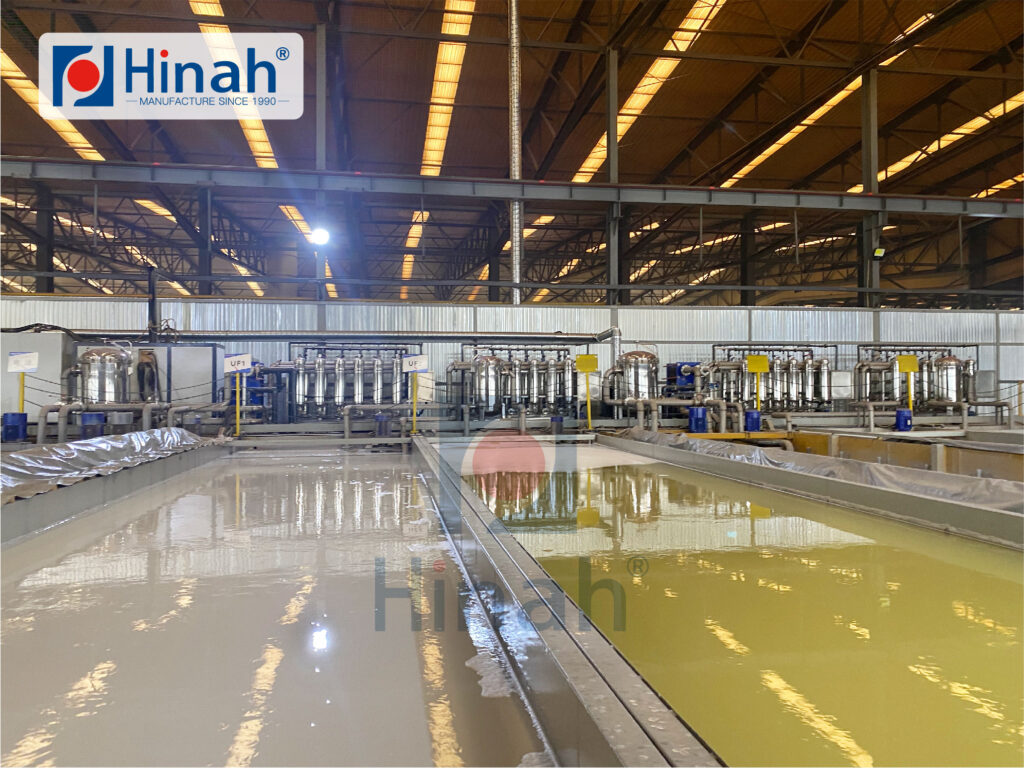
I. Overview of pretreatment system in e-coating line
The pretreatment system is a key link in the e-coating line. Its main function is to provide a clean and activated surface for the coating to ensure that the coating can adhere evenly and firmly. The pretreatment system usually includes multiple steps, such as cleaning, surface activation, phosphating, and passivation, which work together to create the best conditions for subsequent coating.
The quality of pretreatment directly affects the effect of electrophoretic coating. Next, we will explore in detail the main components and working principles of the electrophoretic coating pretreatment system.
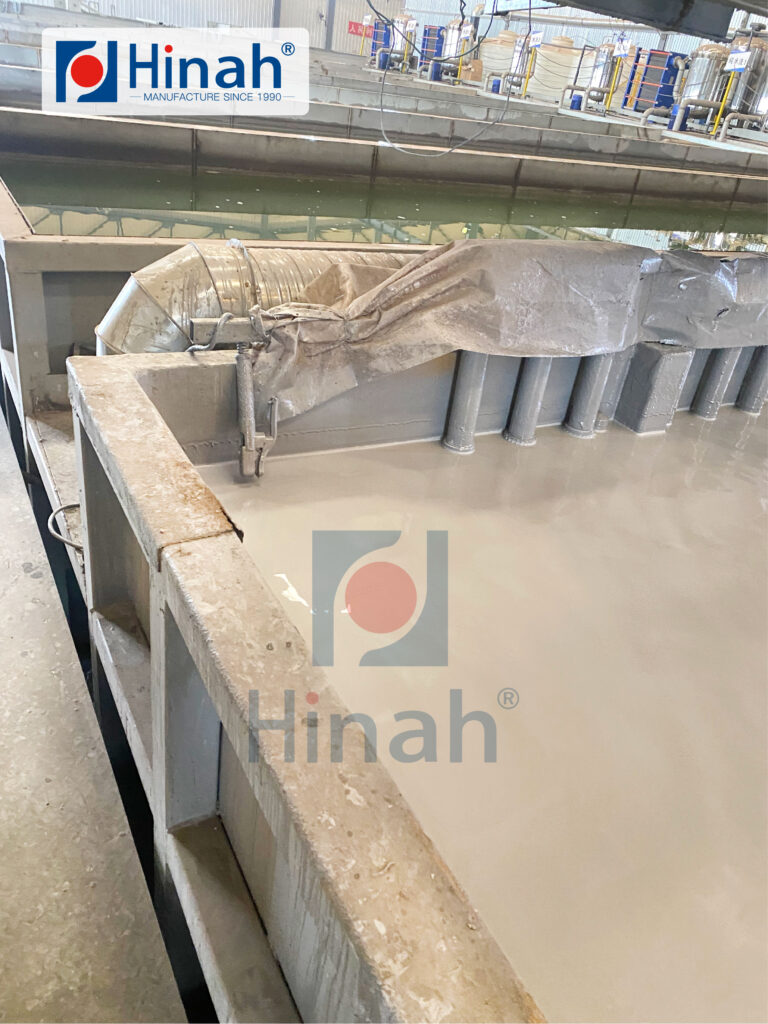
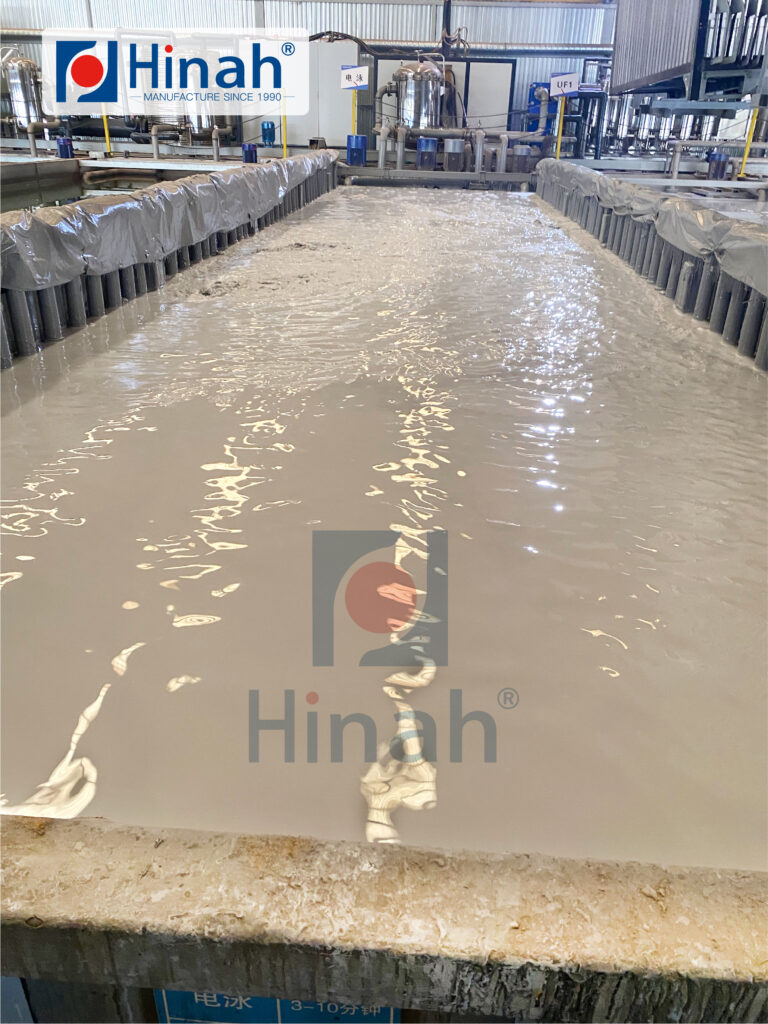
II. Common methods of pretreatment process
There are many ways to pretreat e-coating lines, each with its unique advantages, which can ensure the perfect coating effect according to different needs. Here, we will introduce two common pretreatment methods: spray pretreatment and dip tank pretreatment.
1. Spray pretreatment
Spray pretreatment is a treatment method that cleans and activates the surface of the substrate by spraying cleaning agents and chemical solutions at high pressure. The biggest advantage of this method is that it can evenly cover the surface of the substrate, remove oil, dust, and other contaminants, and is particularly suitable for workpieces with complex shapes or difficult-to-reach parts on the surface. The flexibility of the spray system makes the treatment process both efficient and energy-saving, and it is the first choice in many modern electrophoretic coating production lines.
However, although spray pre-treatment is efficient, it has high requirements for the accuracy of the equipment and the control of liquid flow. Therefore, it is necessary to ensure that the concentration, temperature, and pressure of the cleaning agent are kept in the optimal range during operation. Despite this, spray pre-treatment is still one of the key steps to ensure the quality of the coating, and it can achieve the ideal cleaning effect in a shorter time.
2. Dip tank pretreatment
Unlike spray pretreatment, dip tank pretreatment is a process of removing dirt and oxides by immersing the workpiece in a chemical solution and using the active ingredients in the solution. The dip tank method is particularly suitable for processing workpieces with flat surfaces and simple shapes and can be cleaned and activated for a long time under relatively mild conditions. The advantage of this method is the stability and efficiency of the solution, which can penetrate deep into the surface of the substrate to ensure the adhesion of the coating.
Dip tank pretreatment has a relatively low equipment investment and is relatively simple to operate, but because its cleaning process is relatively mild, it may be necessary to combine other methods to improve the cleaning effect for workpieces with complex shapes. Despite this, dip tank pretreatment is still an indispensable process in many production lines, especially in some small batches or customized coatings, where it can show its unique advantages.
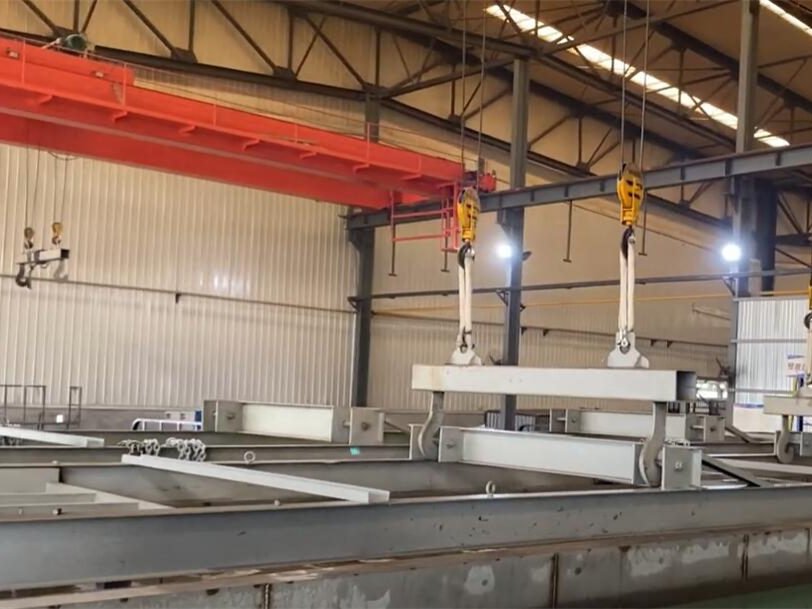
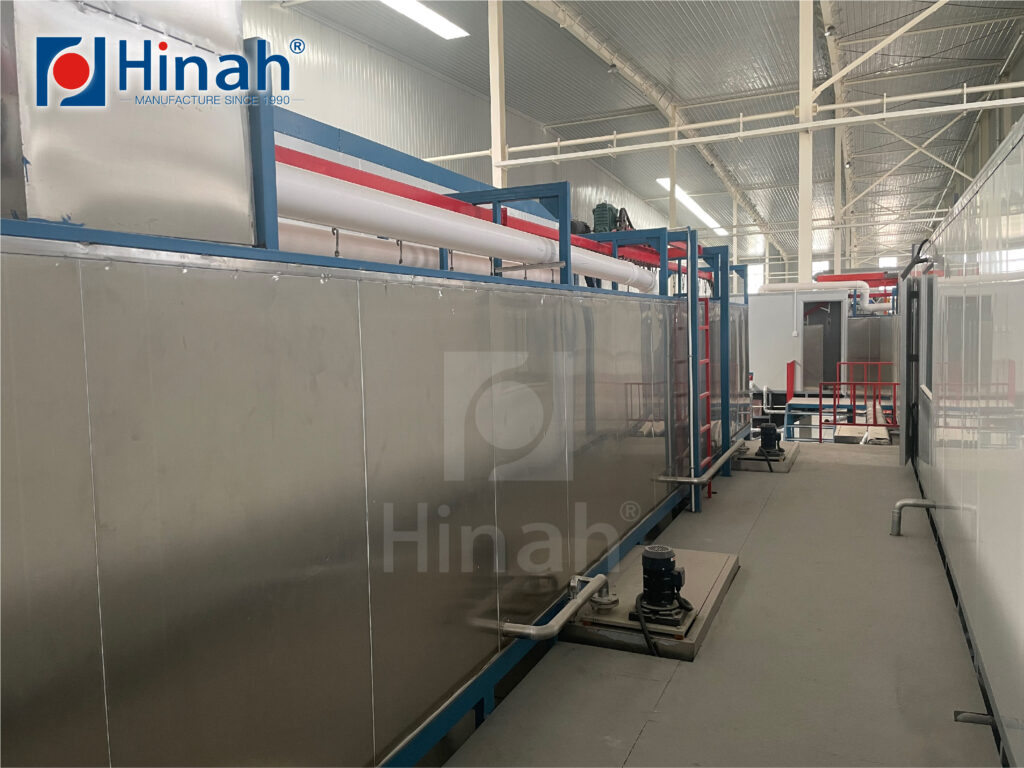
III. The critical importance of pre-treatment to e-coating line
Electrophoretic coating is a technology with extremely high process requirements. As a key link, the pre-treatment system directly affects the efficiency of the entire production line and the quality of the product. Whether it is the stability of the coating effect or cost control, pre-treatment plays a vital role in it.
1. Influence on the quality of electrophoretic paint
Electrophoretic paint is one of the most important materials in the electrophoretic coating process. However, it is expensive and very sensitive. Improper pre-treatment, especially when contaminated workpieces enter the electrophoretic tank, will cause the electrophoretic paint to be contaminated by impurities, and it cannot be used anymore. Due to the high cost of electrophoretic paint treatment, once contaminated, it often means that the electrophoretic paint of the entire electrophoretic tank needs to be replaced, and even the coating work of the entire batch of production lines may be forced to stop. Such accidents not only increase production costs but may also lead to a significant decrease in production efficiency.
Therefore, ensuring that the workpiece is thoroughly cleaned and effectively pre-treated before entering the electrophoretic tank is the key to maintaining the quality of the electrophoretic paint and the normal operation of the production line. Precise control of pretreatment can effectively prevent impurities from entering the electrophoretic solution, thereby reducing unnecessary losses and costs.
2. Impact on coating quality
Pretreatment is not only to clean the surface of the workpiece but more importantly, it provides an ideal base for subsequent electrophoretic coating. Surface activation, decontamination, phosphating, and other treatment steps directly affect the adhesion, uniformity, and durability of the coating.
- Adhesion: Insufficient pretreatment will lead to poor adhesion of the coating and even peeling of the coating. Only on a clean and activated surface can the paint adhere firmly to ensure the long-term stability of the coating.
- Uniformity: Pretreatment is crucial to the uniformity of the coating. If the surface is not effectively treated, the paint may gather or appear weak in certain areas, resulting in uneven thickness of the coating, and affecting the appearance and performance of the product.
- Durability: Good pretreatment can not only enhance the adhesion of the coating but also improve the corrosion resistance and wear resistance of the coating. Especially in industries such as automobiles and home appliances that have extremely high requirements for coatings, pretreatment directly determines the durability of the coating and its ability to resist environmental factors.
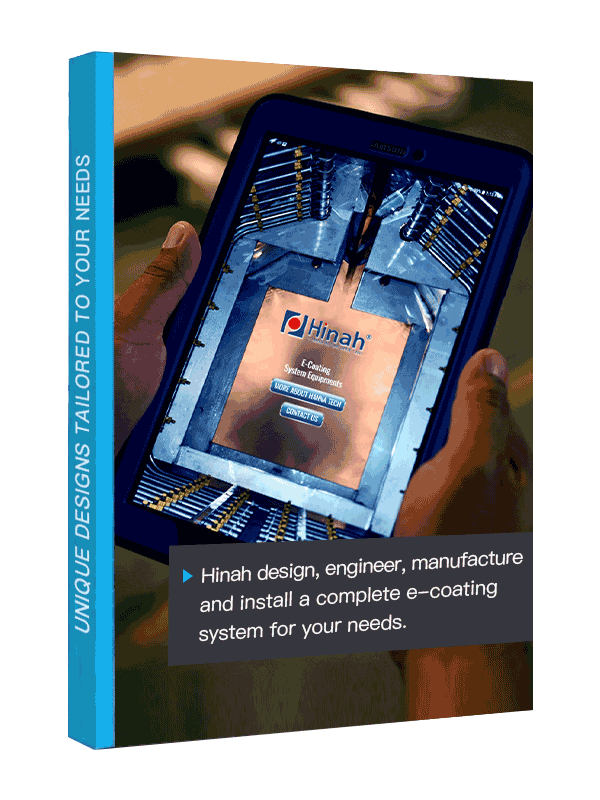
Let's Have A Chat
Get An E-coating Line Planning !
Match Your Products, Get The Solution & Price..
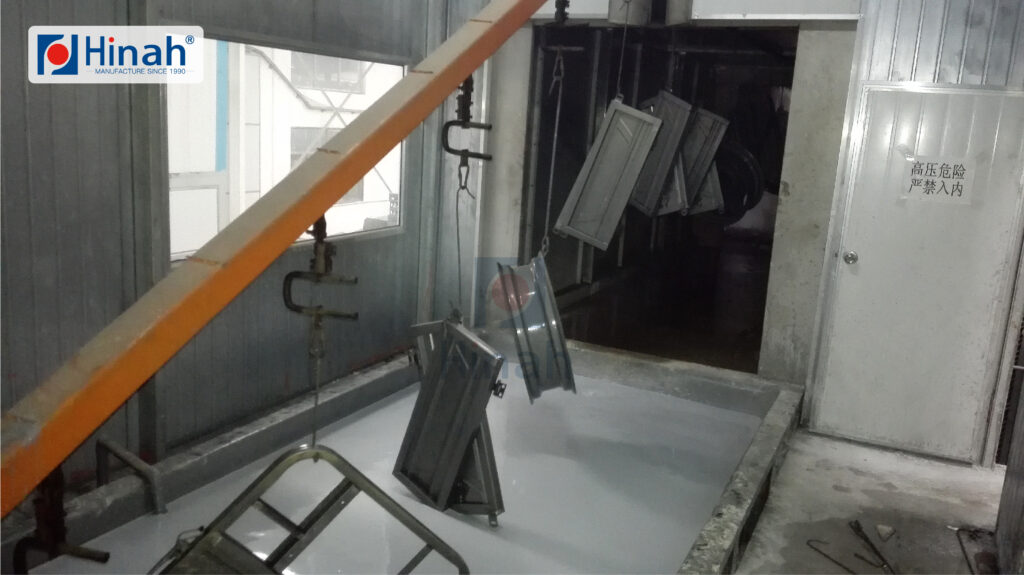
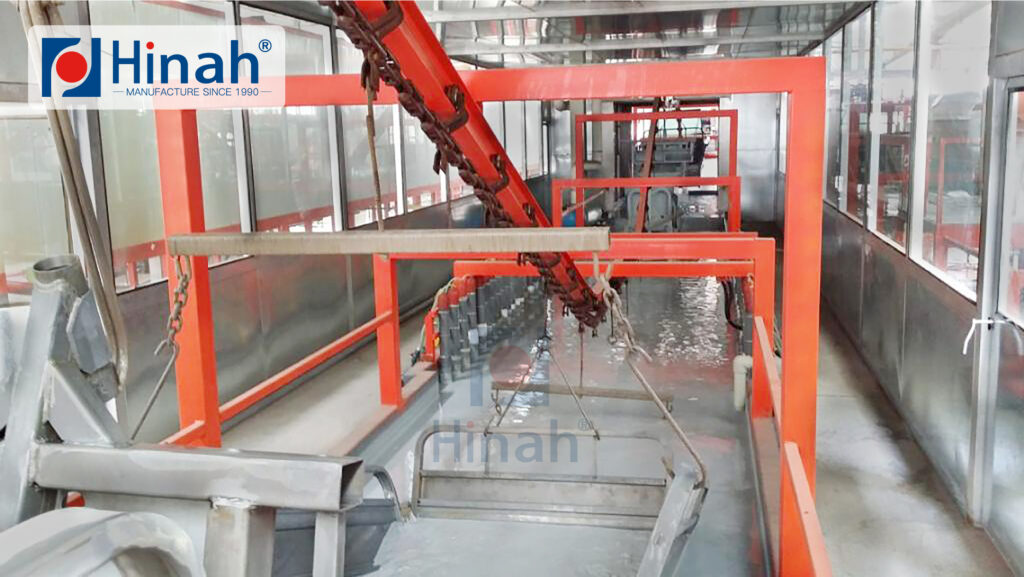
IV. Potential problems in the pre-treatment process
1. Improper management and use of chemicals
The pre-treatment process relies on a variety of chemicals, such as cleaning agents, pickling solutions, phosphating solutions, etc. Improper selection or improper use of chemicals may result in substandard surface treatment of the workpiece or even damage the workpiece. Long-term use of inappropriate chemicals may also lead to corrosion or contamination of equipment and reduce production efficiency.
2. Time control issues in the pre-treatment process
Each step of the pre-treatment has a certain time requirement. Too long or too short a time may affect the quality of the workpiece surface. For example, too long a soaking time may cause corrosion on the workpiece surface, and too short a time may not be thoroughly cleaned.
3. Environmental protection and waste management issues
The chemicals and water resources used in the pre-treatment process consume a lot of resources, and wastewater and exhaust gas emissions need to meet environmental protection requirements. If the waste is not handled properly, it will not only pollute the environment but also cause the production line to stop working or be fined.
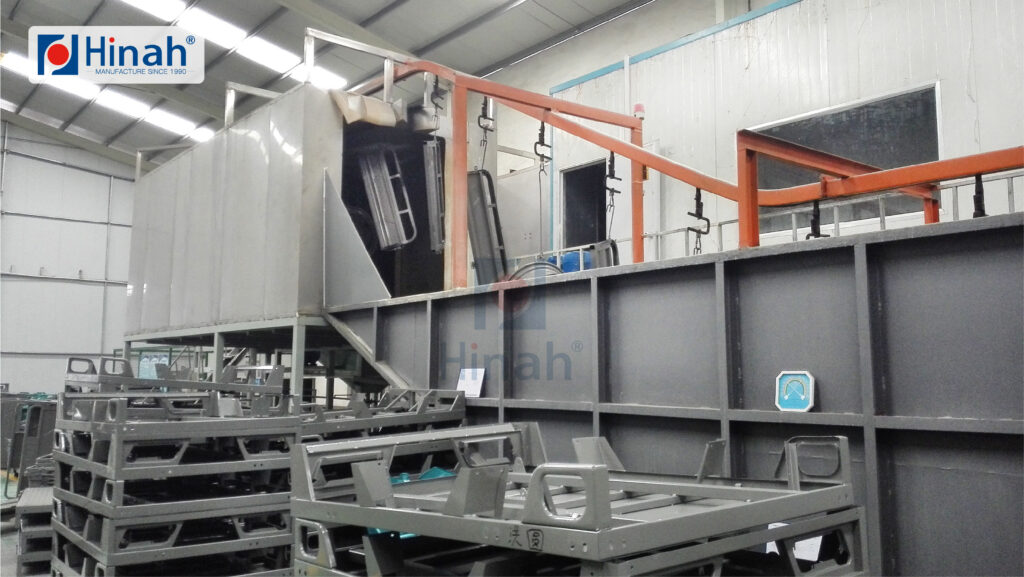
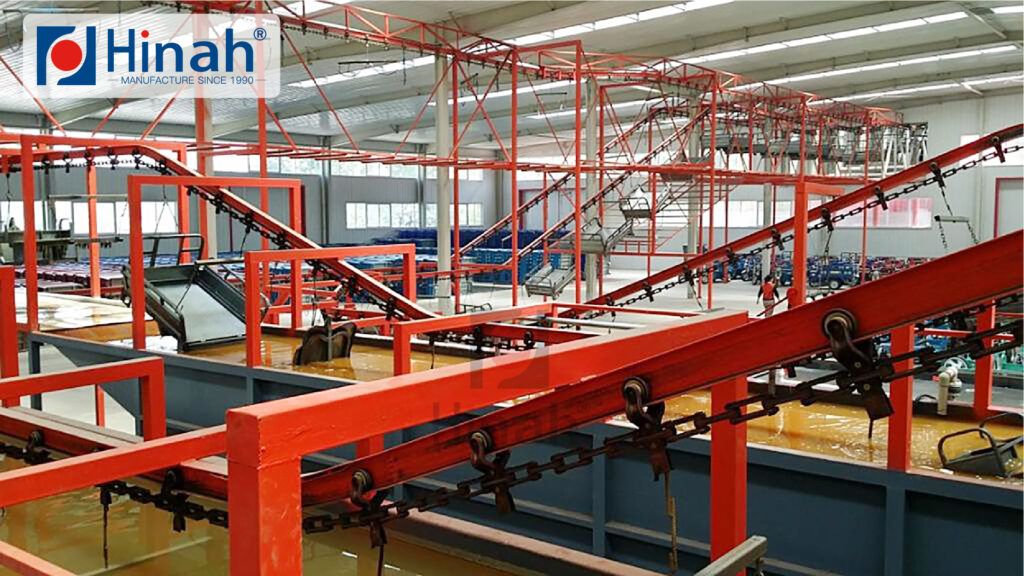
V. Conclusion
The pretreatment system plays a vital role in the entire e-coating line. From ensuring the coating quality to protecting the electrophoretic paint and improving production efficiency, the design and implementation of the pretreatment system cannot be ignored.
In general, pretreatment is not just a simple cleaning step, it directly determines the coating effect and the stable operation of the production line. Fine management and continuous optimization of the pretreatment process will bring higher quality assurance and lower operating costs to the electrophoretic coating production line.