When choosing a coating process, electrocoating and liquid coating each have advantages. Electrocoating has become the first choice for many demanding industries due to its excellent uniformity and durability. Liquid coating has also always occupied a place in various applications due to its flexibility and cost-effectiveness. When faced with these two technologies, how to make a choice depends on your needs and goals. This article will explore the characteristics of the two in-depth to help you find the most suitable coating solution.
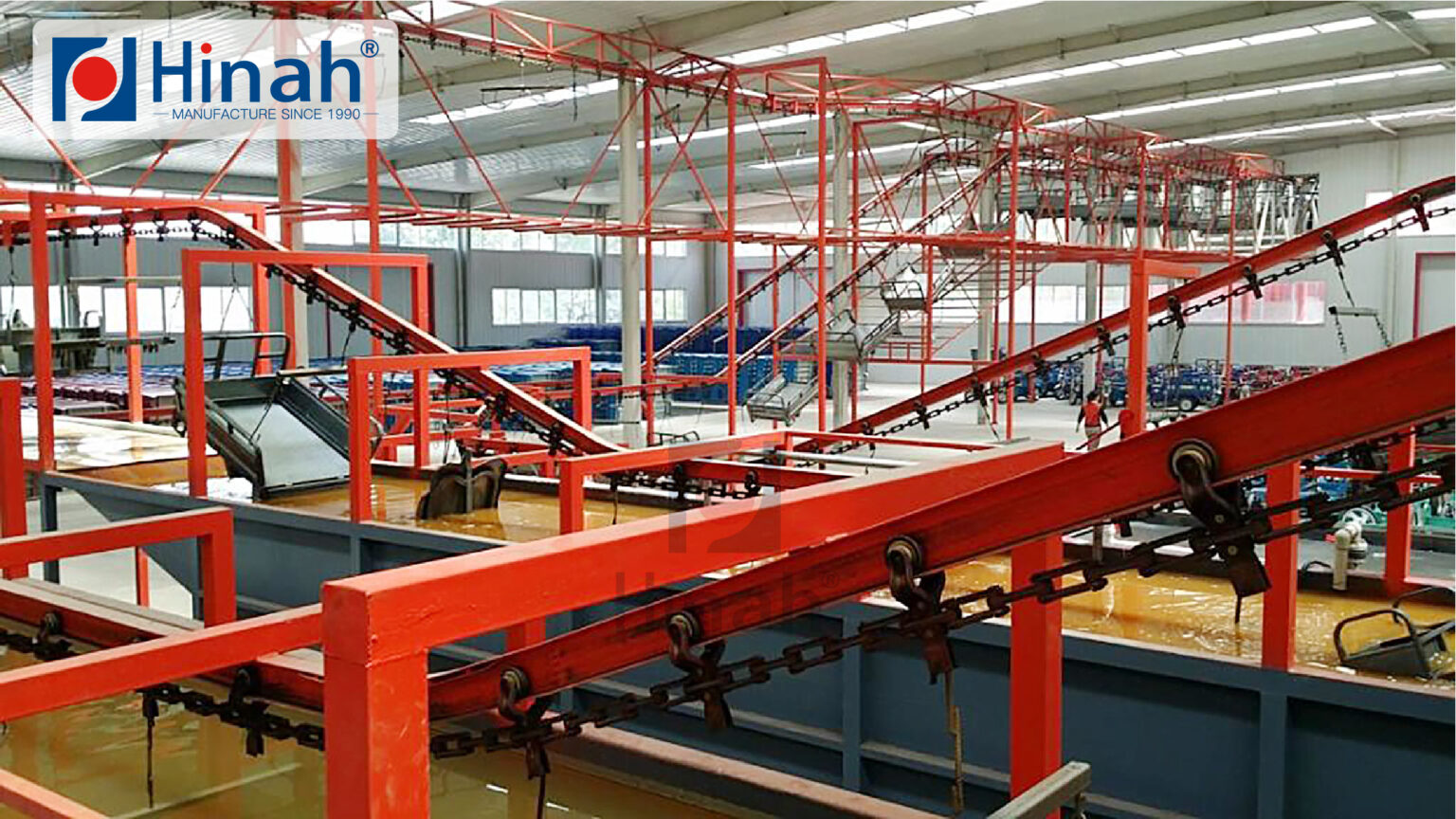
Introduction to electrocoating process
Electrocoating is a coating process that uses an electric field to deposit charged paint particles onto the surface of a workpiece. The basic principle is to immerse the workpiece in a coating solution, and through the action of the electric field, the paint particles migrate to the surface of the workpiece under the promotion of the electric field and form a uniform coating. Electrophoretic coating usually adopts cathode electrophoresis or anodic electrophoresis, and the coating thickness is uniform, the adhesion is strong, and it has excellent corrosion resistance and wear resistance.
The process of electrophoretic coating includes the following key steps:
- Pretreatment systems: Clean the surface of the workpiece, remove impurities such as oil and rust, and prepare for coating.
- Electrophoretic deposition: Immerse the treated workpiece in a coating bath and apply an electric field to deposit the paint particles evenly.
- Curing Oven: Heat the coated workpiece to cure the coating to ensure the hardness and durability of the coating.
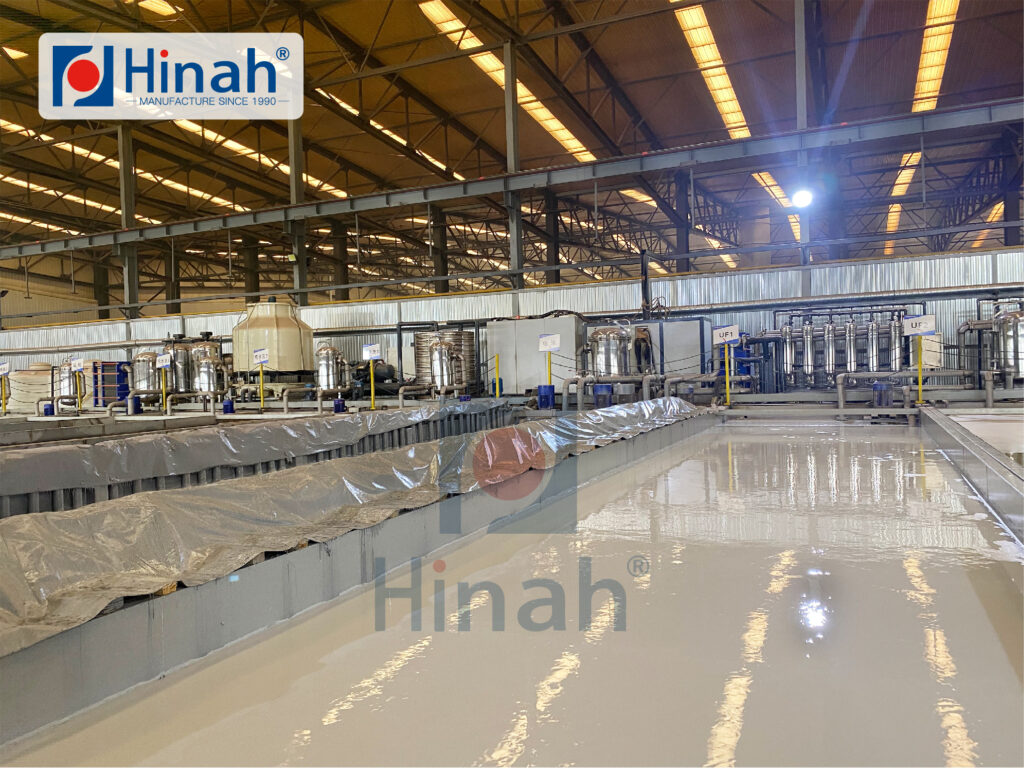
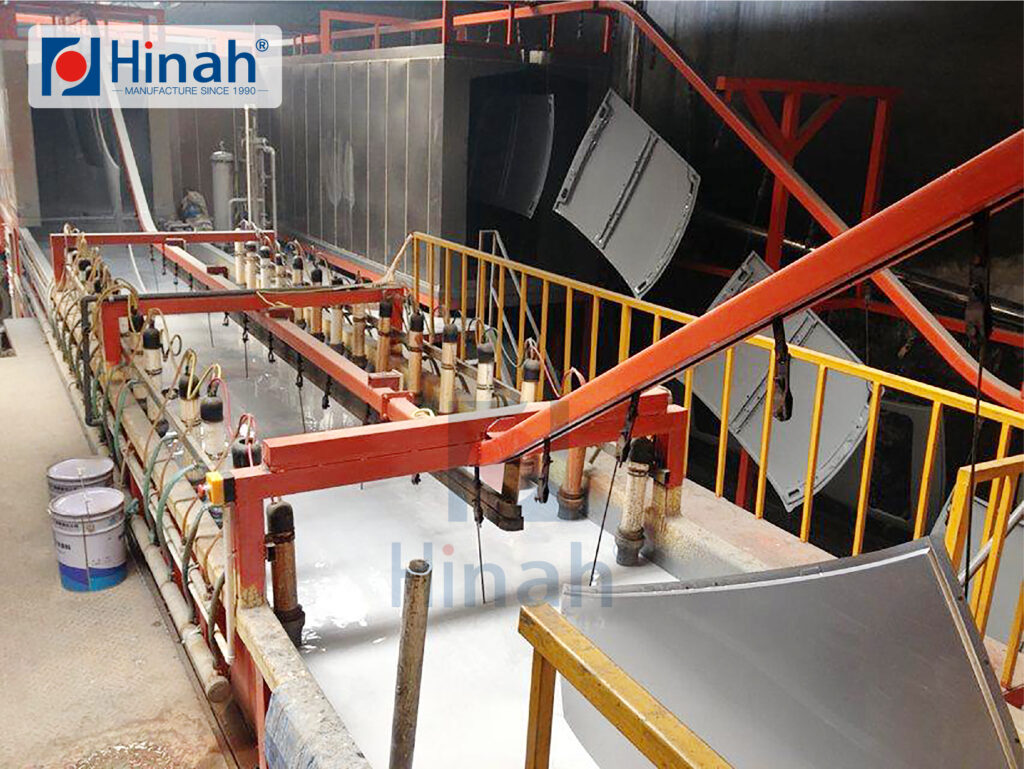
Introduction to Liquid Coating Process
Liquid coating is a process of forming a coating by applying liquid paint to the surface of an object. Its common application methods include spraying, brushing, and dipping, and it is suitable for a variety of materials and shapes.
The main feature of liquid coating is its flexibility, which can provide a wide range of color options and effects such as gloss, matte, or texture effects. In addition, liquid coating equipment has a low cost and is suitable for small batch production and fine coating needs. Although the uniformity of the coating may be affected by operating skills and environment, it is still widely used in industries such as construction, furniture, and home appliances, especially for the needs of simple shapes and diversified coating effects.
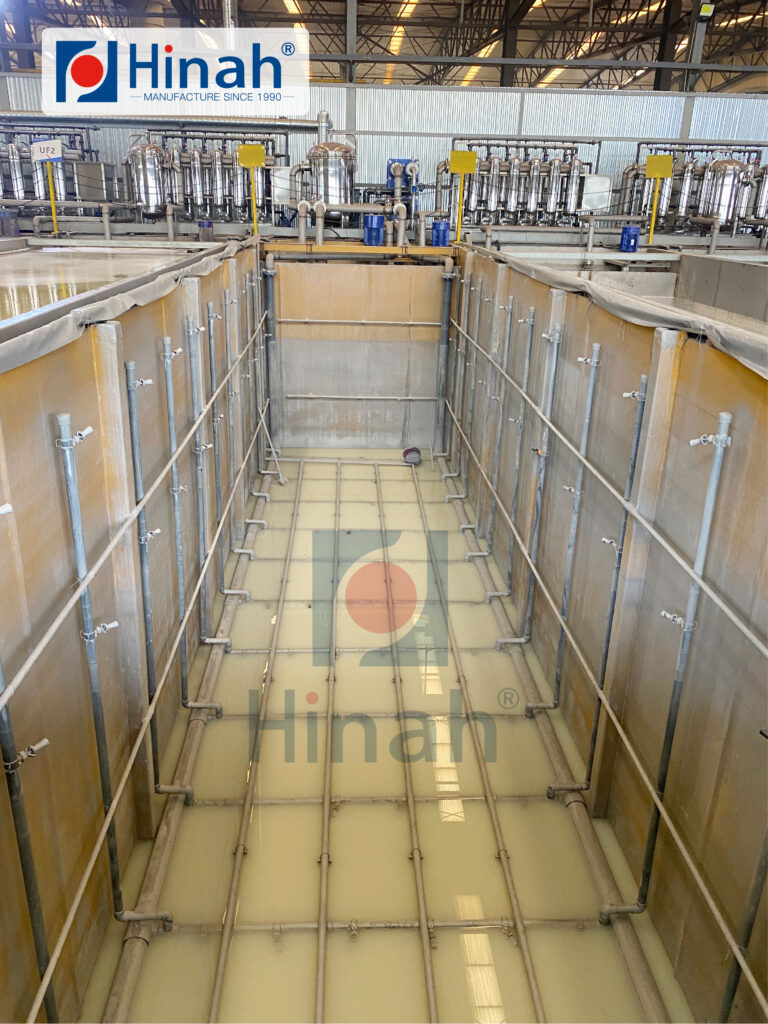
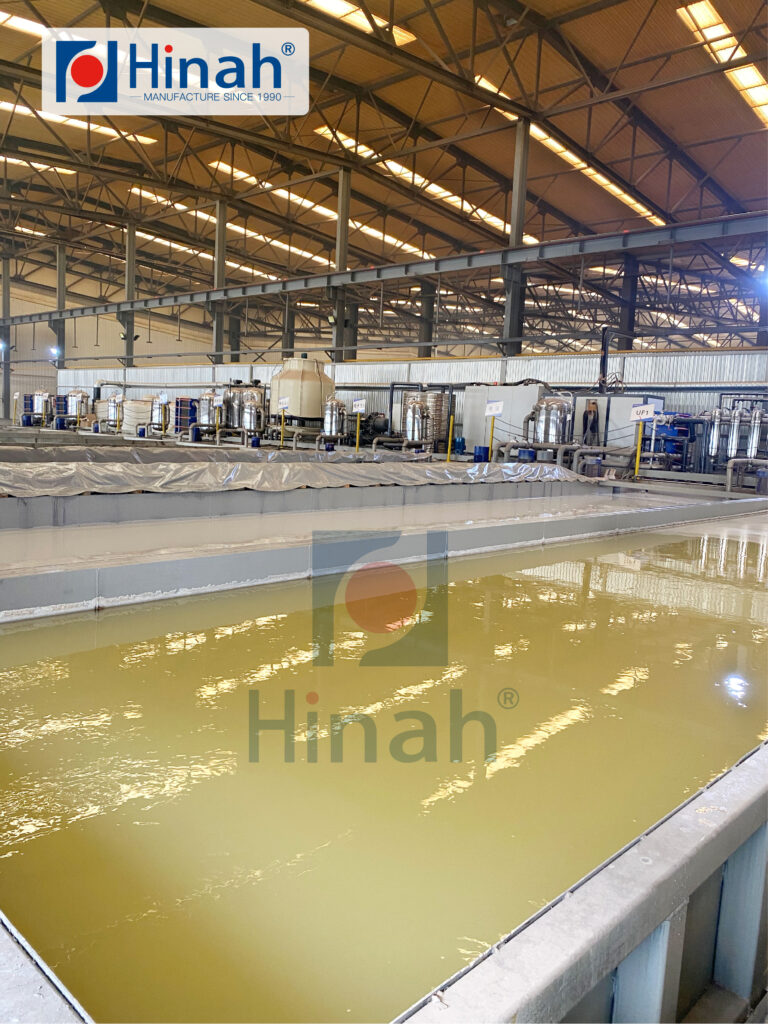
Comparison between electrocoating and liquid coating
1. Coating uniformity
- One of the biggest advantages of e-coating is the uniformity of its coating. Since the coating is deposited through the action of an electric field, the electrophoretic coating can cover the surface of workpieces with complex shapes and ensure that the coating thickness is uniform.
- The uniformity of liquid coating is relatively poor, especially on workpieces with complex shapes. The liquid coating may have an uneven coating, especially during the spraying process. If the operation is improper or the coating is not sprayed evenly, the coating may have inconsistent thickness.
2. Durability and environmental protection
- The coating of e-coating has extremely high durability, especially in terms of corrosion resistance and wear resistance. It also meets increasingly stringent environmental protection standards due to its water-based coating and efficient resource utilization and is less polluting and in compliance with environmental regulations.
- The durability of liquid coating is worse than that of electrophoretic coating, especially in highly corrosive environments, where the coating is easily damaged. Although liquid coating can also provide some protection, its corrosion resistance and wear resistance are usually not as good as electrophoretic coating. In terms of environmental protection, traditional liquid coatings (especially solvent-based coatings) may contain volatile organic compounds (VOCs), which pose certain risks to the environment and the health of operators. Although there are now environmentally friendly liquid coatings such as water-based coatings, overall, liquid coating is less environmentally friendly than electrophoretic coating.
3. Cost
- The initial investment in electrophoretic coating is relatively high, mainly reflected in the investment in equipment and facilities. Electrophoretic coating requires a dedicated electrophoretic tank, control system, and efficient paint recovery system, so the equipment cost is relatively high.
- The cost of liquid coating is low, mainly reflected in the investment in coatings and equipment. The liquid coating process is simple and the equipment cost is low.
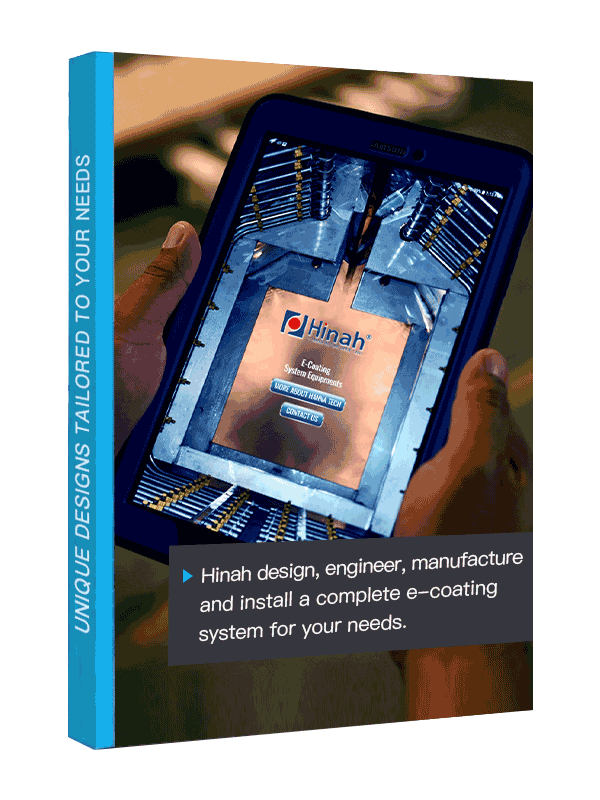
Let's Have A Chat
Get An E-coating Line Planning !
Match Your Products, Get The Solution & Price..
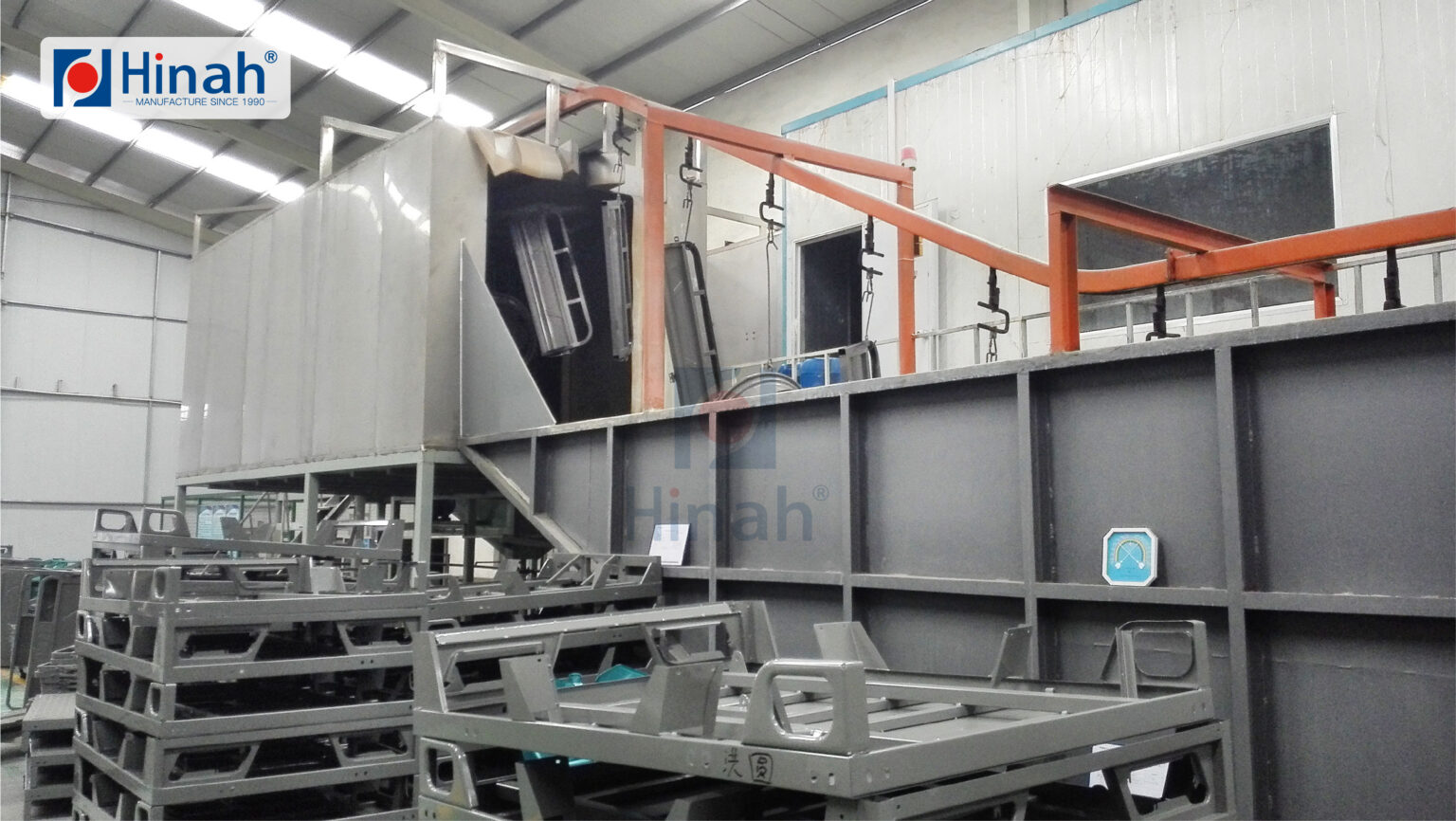
Choose the right coating process
Choosing the right coating process depends on multiple factors, including the type of product, the functional requirements of the coating, the scale of production, and environmental and cost requirements. Electrophoretic coating and liquid coating each have their advantages. Understanding the differences and applicable scenarios between them can help you make the best choice.
At Hinah Coatings, we focus on providing customers with high-quality coating solutions customized to specific needs. Whether you are considering electrocoating or liquid coating, our professional team can help you make an informed choice based on your project needs to ensure that your products achieve optimal performance. Contact us today to learn how we can provide professional support for your next project.