E-Coating and Electroplating are two common metal surface treatment technologies. Although they both use electric current to deposit coatings on metal surfaces, there are obvious differences in process, application, and effect. With environmental protection and production efficiency requirements being improved, choosing the right process has become particularly important. This article will compare the main differences between the two technologies and introduce the key functions of e-coating equipment to help you better understand their advantages and applicable scenarios.
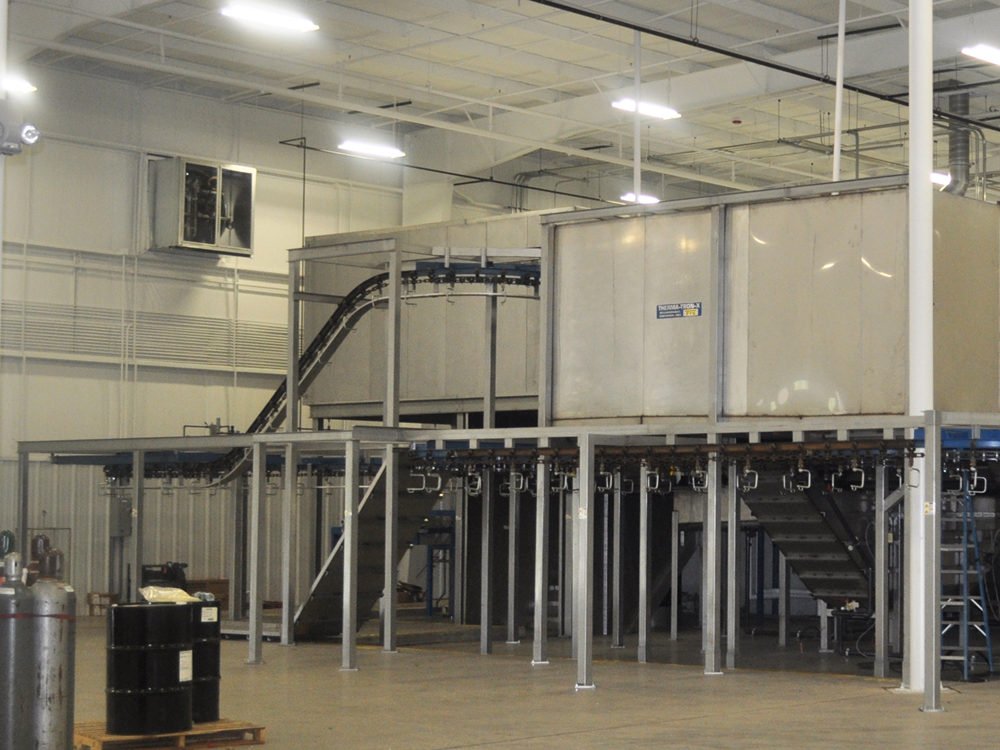
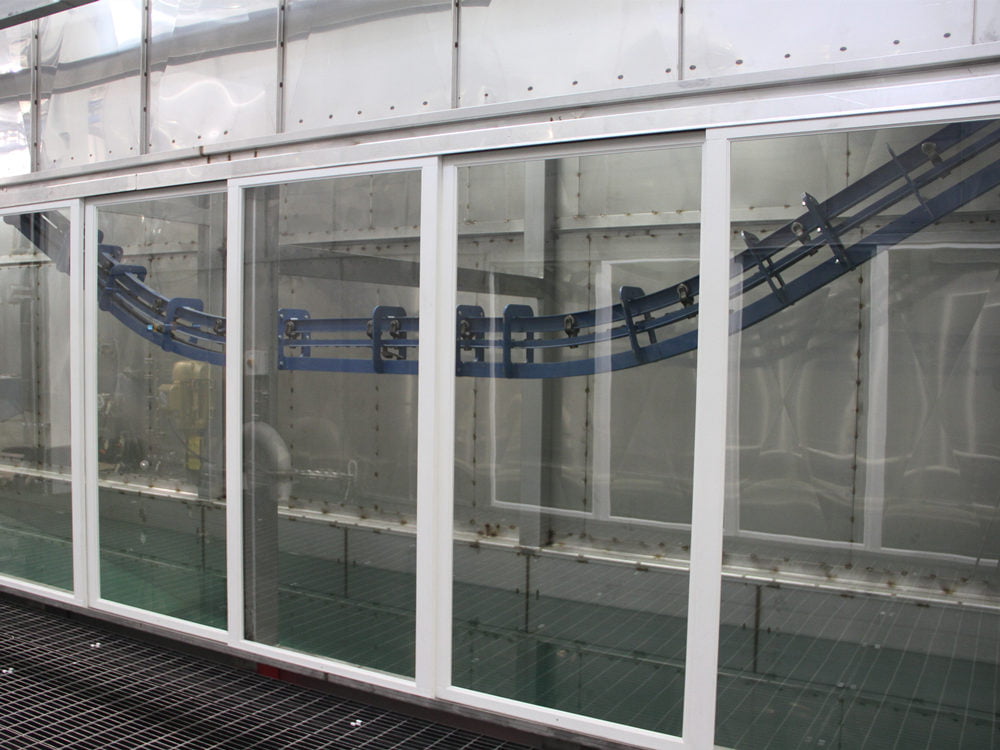
I. What is e coating?
E coating is a surface treatment technology that uses an electric field to deposit charged paint particles onto the surface of a workpiece. Through e coating equipment such as an electrophoretic tank, a power control system, and a paint circulation system, electrophoretic coating can accurately control the uniformity and thickness of the coating. Under the action of the current, the paint particles in the electrophoretic coating process will be deposited toward the surface of the metal workpiece with the opposite charge, forming a uniform and dense coating, which is widely used in the anti-corrosion and decoration of metal surfaces.
II. What is electroplating?
Electroplating is a surface treatment technology that reduces metal ions and deposits them on the surface of metal workpieces through an electrolytic reaction to form a layer of metal coating. Electroplating is mainly used to improve the corrosion resistance, hardness, and decorativeness of workpieces, and is widely used in automobile, electronics, hardware, and other industries.
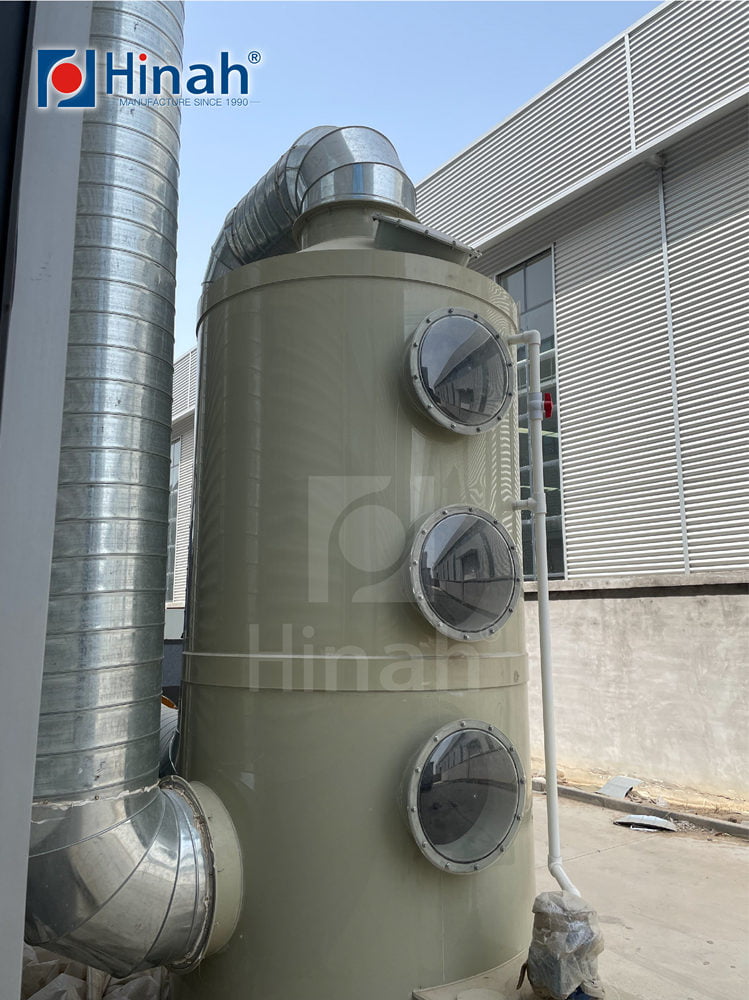
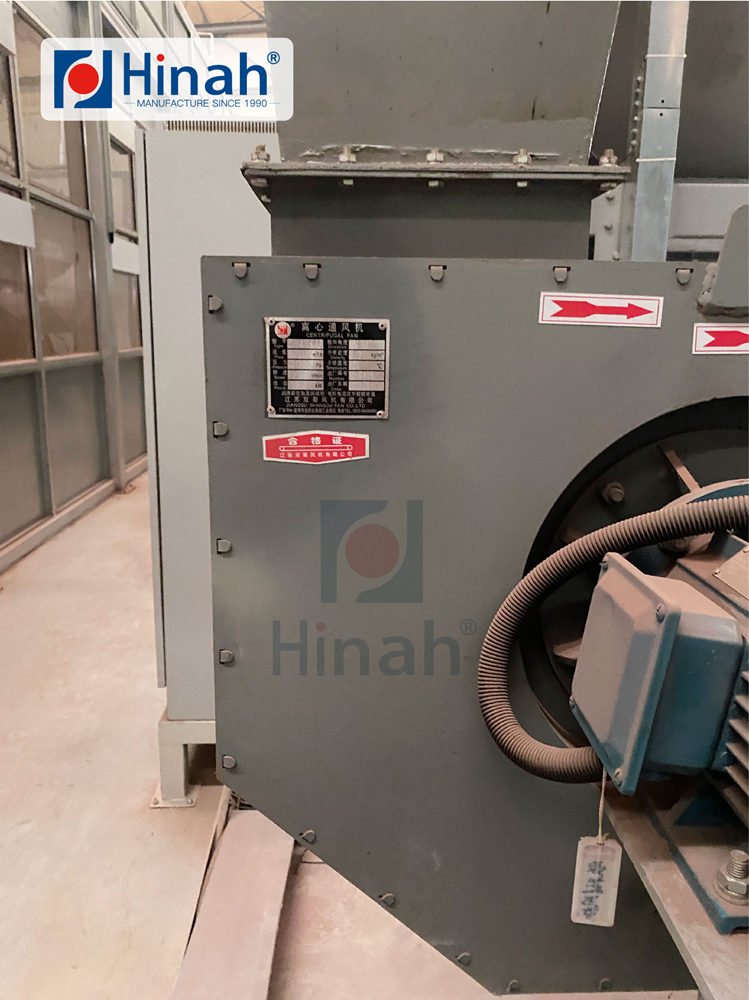
III. E-coating vs electroplating: main differences
1. E-coating vs electroplating: Process principle
- Electrophoretic coating: Electrophoretic coating uses the effect of an electric field to make charged paint particles adhere to the surface of the workpiece. The paint particles are guided by the current in the electrophoretic tank and deposited on the surface of the workpiece with opposite charges to form a uniform coating. The key to electrophoretic coating is the charge property of the paint particles and the effect of the electric field strength on the coating thickness.
- Electroplating: Electroplating is achieved through an electrolytic reaction, reducing metal ions from the electrolyte and depositing them on the surface of the substrate. The power supply controls the flow of current, and the metal ions are gradually deposited under the action of the electric field to form a metal coating. The focus of electroplating is the metal ion concentration of the electrolyte, the current density, and the time it contacts the substrate surface.
2. E-coating vs electroplating: Application field
- Electrophoretic coating: Electrophoretic coating is widely used in industries that require strong corrosion resistance, wear resistance, and aesthetics, such as automobiles, home appliances, building materials, etc. Due to its uniform coating and controllable thickness, it is particularly suitable for workpieces with complex shapes and mass production, such as automobile bodies, home appliance housings, steel structures, etc.
- Electroplating: Electroplating is mainly used to improve the hardness, wear resistance, corrosion resistance, or decorative effect of workpieces. Common applications include automotive parts, electronic equipment, hardware tools, jewelry, etc. Electroplating is often used for decorative coatings (gold, silver, nickel, chromium, etc.) and products with special requirements for hardness and conductivity.
3. E-coating vs electroplating: Equipment and technology
- Electrophoretic coating: Electrophoretic coating requires special e coating equipment, including an electrophoretic tank, power control system, paint circulation system and temperature control system. These equipment can help control the deposition process, coating thickness, and quality of the coating. E coating equipment can realize automatic and intelligent operation, improve production efficiency, and reduce manual intervention.
- Electroplating: The equipment required for electroplating includes an electroplating tank, power controller, filtration system, etc., and the electroplating process requires strict control of current, voltage, and electrolyte concentration. The metal salt solution needs to be continuously replenished in the electroplating tank to maintain a stable coating quality. Electroplating equipment is generally suitable for the production of smaller batches or precision parts, and the process control is more complicated.
4. E-coating vs electroplating: Environmental protection and safety
- Electrophoretic coating: Electrophoretic coating is more environmentally friendly than electroplating. Paint is usually water-based and can be recycled through the paint circulation system to reduce paint waste. Since electrophoretic coating generates less wastewater and waste gas, it has relatively little impact on the environment. There are relatively few chemicals in the process, so the health hazards to personnel during operation are relatively low.
- Electroplating: The chemicals used in the electroplating process are relatively complex, and the electroplating tank contains a large amount of toxic metal ions and chemicals (such as cyanide, acid solution, etc.). Wastewater and waste gas treatment is difficult and has a high risk of environmental pollution. The safety risk in the electroplating process is relatively high, so strict safety operating procedures and waste treatment systems are required to ensure safety and environmental protection during the production process.
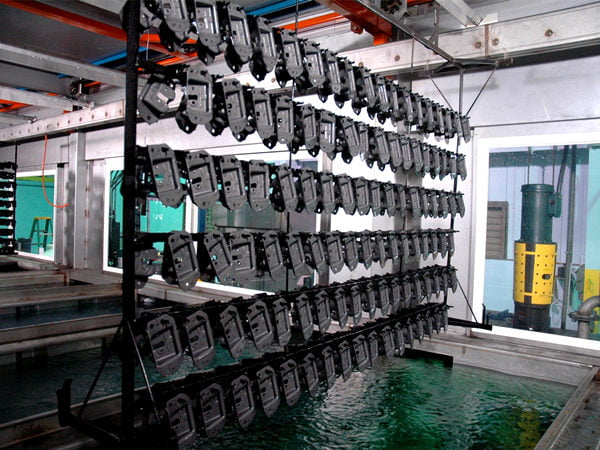
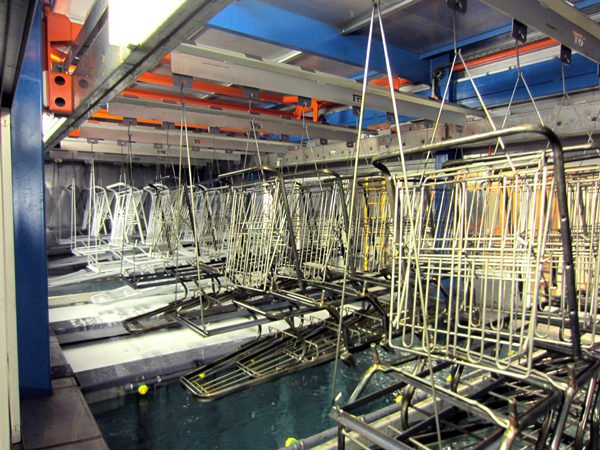
IV. Advantages of e coating equipment
E coating equipment has obvious advantages over electroplating equipment in many aspects.
First, electrophoretic coating provides a more uniform and dense coating, which is especially important for workpieces with complex shapes or difficult to achieve spraying effects. Compared with electroplating, electrophoretic coating can handle more types of substrates, even plastics, and can better cover the dead corners and gaps of workpieces.
Second, the water-based paint used in electrophoretic coating is highly environmentally friendly and recyclable, thus reducing the waste of paint and pollution to the environment. This advantage is especially important under today’s increasingly stringent environmental regulations. Electroplating usually uses chemical solutions containing metal salts, which require complex waste treatment procedures to avoid pollution.
In addition, electrophoretic coating equipment is usually highly automated, which can achieve more precise coating control, reduce manual intervention, and improve production efficiency. Relatively speaking, electroplating equipment requires more manual operation, chemical management in the process is more complicated, and the production cycle and cost may also be higher.
Finally, e coating equipment has lower maintenance costs in long-term operation. Due to the high utilization rate of coatings and the simple maintenance of equipment, enterprises can reduce overall operating costs while ensuring production efficiency. In contrast, electroplating equipment has high maintenance requirements for electrolytes and chemicals in long-term use, and the equipment replacement cycle is relatively short.
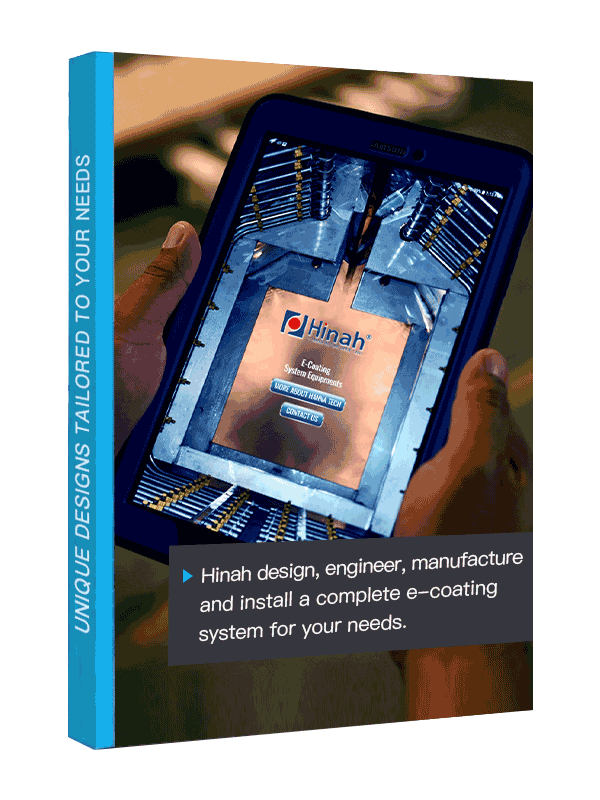
Let's Have A Chat
Get An E-coating Line Planning !
Match Your Products, Get The Solution & Price..
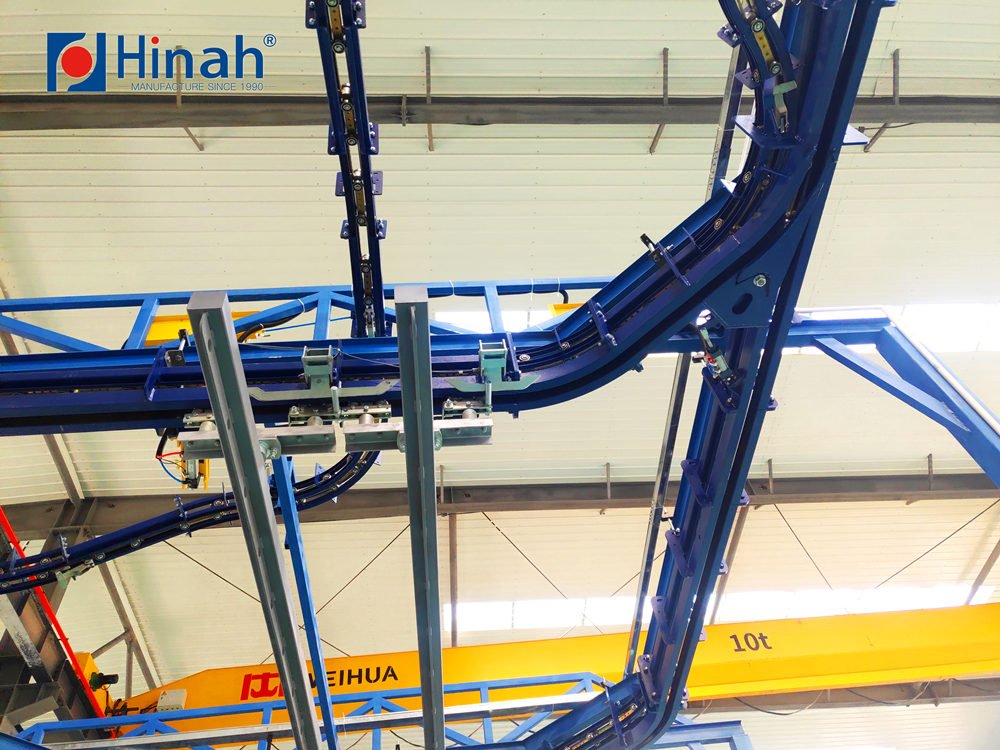
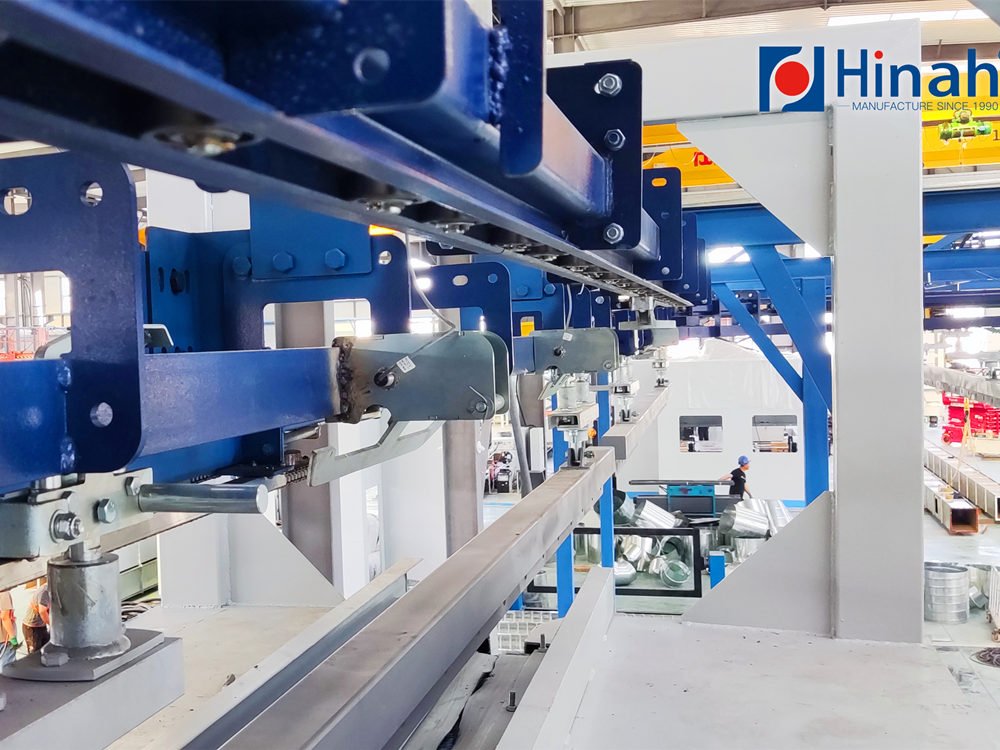
V. Conclusion
Electrophoretic coating and electroplating are two commonly used surface treatment technologies, each with its own characteristics and application advantages. Electrophoretic coating deposits paint through the action of an electric field, which can provide a uniform and dense coating. It is especially suitable for workpieces with complex shapes and is widely used in automobiles, home appliances, building materials, and other fields. Electroplating deposits metal ions on the surface through an electrolysis reaction, which is often used to provide metallic luster and decoration, and is used in electronic components, jewelry, and other fields. Electrophoretic coating has the advantage of being environmentally friendly, using water-based paint, and being recyclable, while electroplating involves more complex wastewater treatment and chemical management.
Compared with electroplating, electrophoretic coating equipment has significant advantages. It has lower maintenance costs and higher operating efficiency over long periods of use.