Electrocoat paint is a widely used technology for metal surface treatment. Its core advantage is that it can provide uniform, durable, and high-quality coatings. However, during the electrocoat paint process, temperature changes will directly affect the stability and adhesion of the coating and thus affect the quality of the final coating. To ensure the consistency and stability of the coating quality, thermostatic equipment plays a vital role in this process. This article will explore the key role of thermostatic equipment in electrocoat paint and how they help maintain temperature control in the production process to optimize the coating effect.
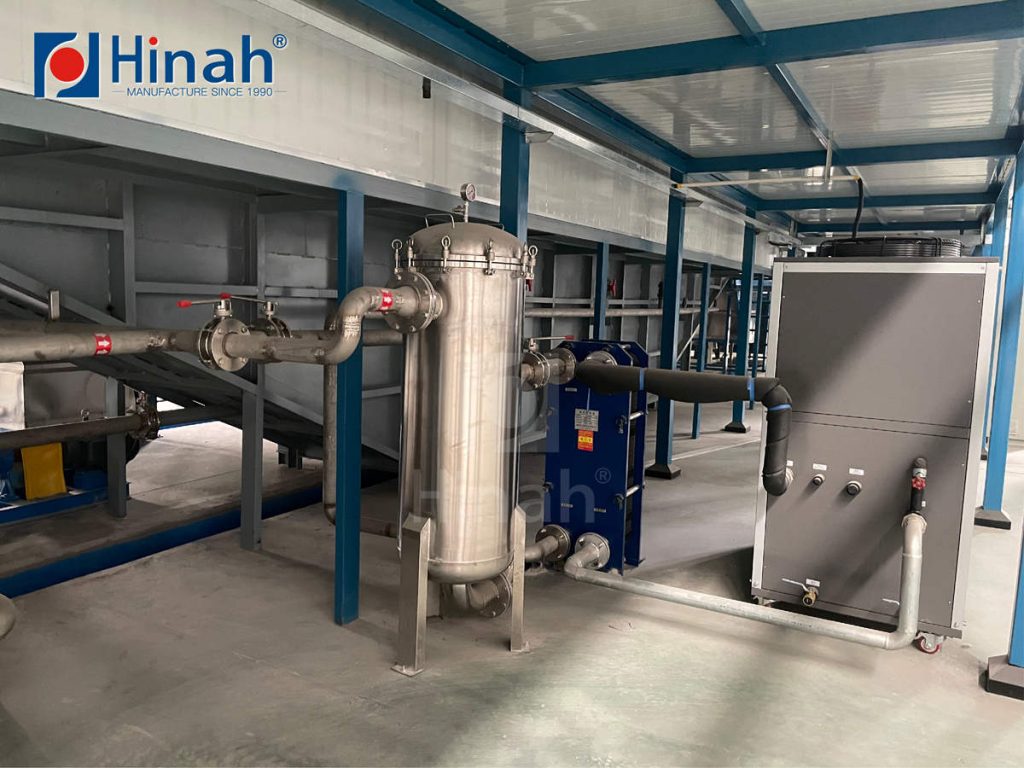
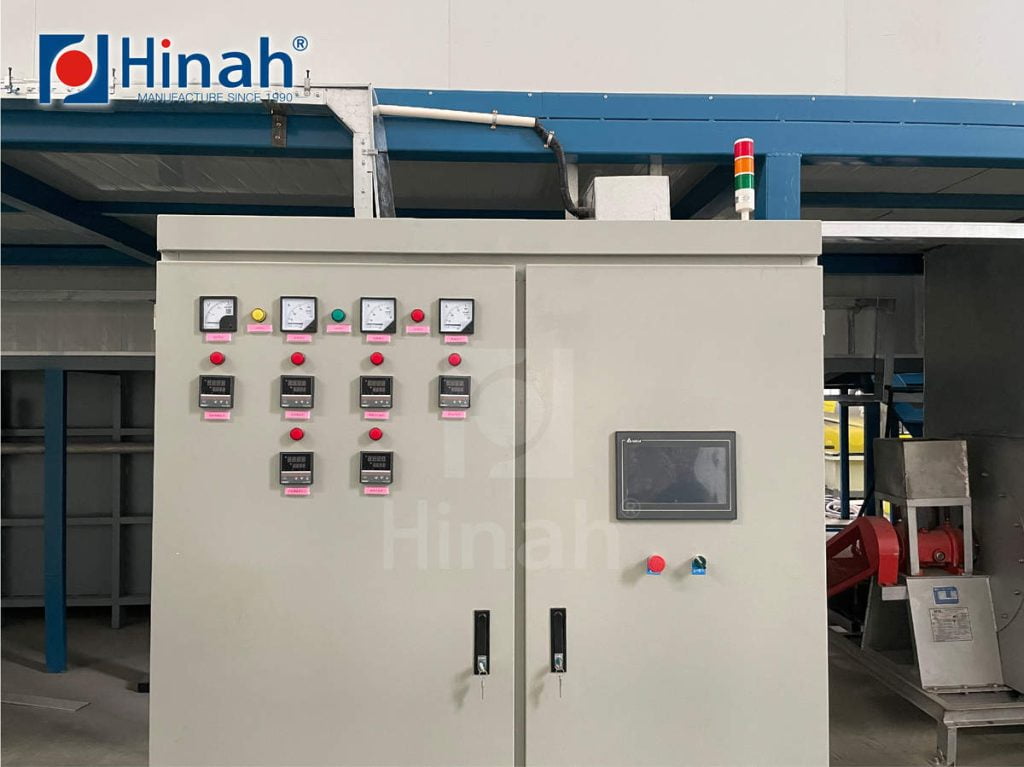
I.Why is electrocoat paint quite sensitive to temperature?
The basic principle of electrocoat paint is to deposit paint particles on the surface of the workpiece through an applied current in the e-coat tank to form a coating. This process involves chemical and physical reactions of the paint and is extremely sensitive to temperature. The temperature of the coating liquid directly affects the movement speed of the paint particles, the deposition process, and the uniformity of the coating. When the temperature is too high or too low, the paint particles will be deposited unevenly, which will in turn affect the thickness, flatness and adhesion of the coating, resulting in instability in the final coating quality.
Temperature fluctuations can cause a series of coating problems. First, when the temperature is too low, the deposition speed of the paint particles slows down, which may lead to uneven coating thickness and even paint precipitation. If the temperature is too high, the stability of the coating liquid may be affected, resulting in a decrease in the adhesion of the particles on the surface of the workpiece, making the coating weak and easy to peel off. In addition, temperature fluctuations may also cause instability of the current during the electrocoat paint process, further exacerbating the fluctuation of the coating quality. Therefore, maintaining a stable temperature is essential to ensure the smooth progress of the electrocoat paint process and improve the uniformity and adhesion of the coating.
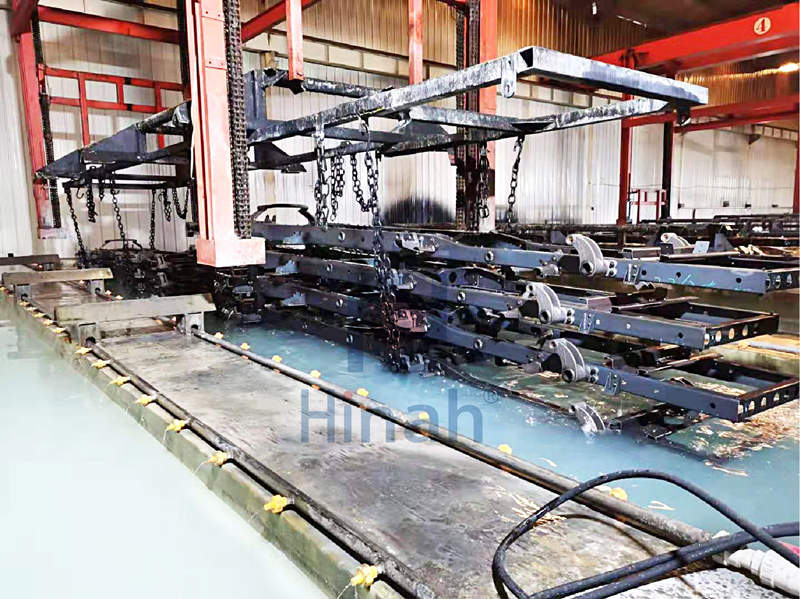
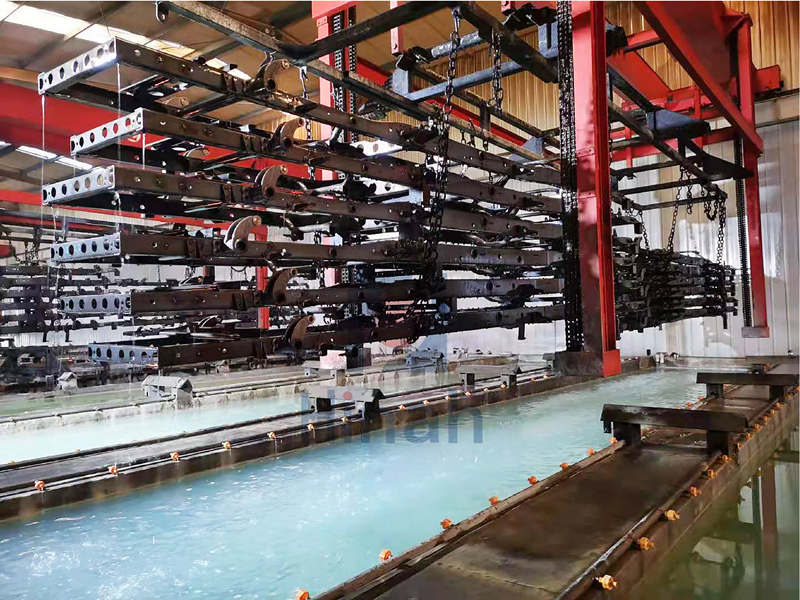
II.The role of thermostatic equipment
Thermostatic equipment plays a vital role in the e coat paint line, which is mainly reflected in the following three aspects:
1.Maintaining a stable temperature to avoid the influence of temperature fluctuations
Thermostatic equipment accurately controls the temperature of the coating tank liquid to prevent temperature fluctuations from causing uneven coating thickness or decreased adhesion, ensuring stable coating effects.
2.Control the chemical properties of the coating liquid and the electrophoretic process
Thermostatic equipment helps maintain the chemical stability of the coating and prevents temperature changes from affecting the viscosity and conductivity of the coating liquid, thereby maintaining the stability of the current and voltage during the electrophoretic process.
3.Improving coating consistency and quality
By stabilizing the temperature, the thermostatic equipment ensures uniform deposition of coating particles, improves the uniformity and adhesion of the coating, and thus improves the overall quality of the coating.
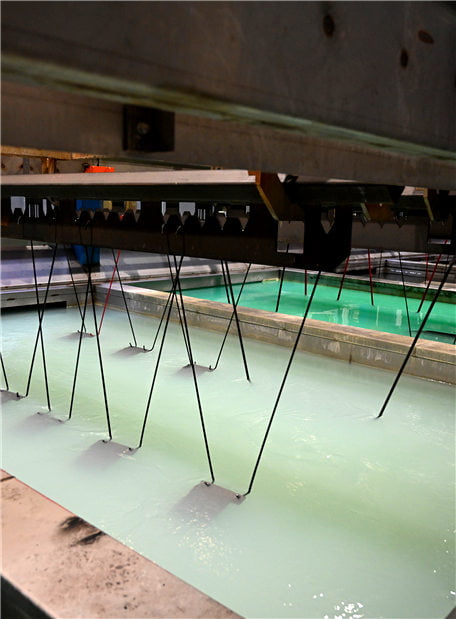
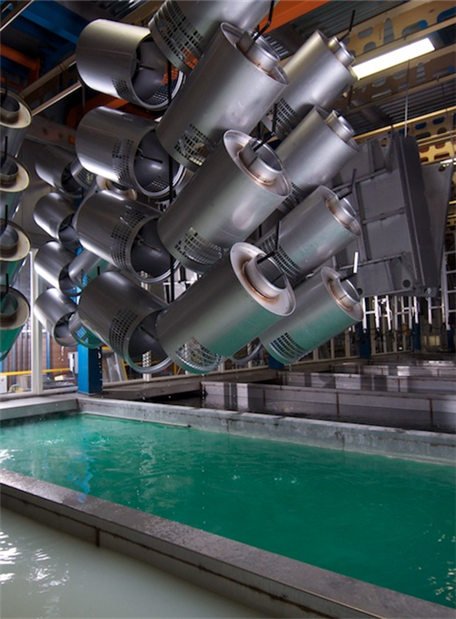
III. Types of constant temperature equipment
There are three main types of constant temperature equipment, each of which plays a different role in maintaining the temperature stability of the coating liquid:
1. Heating constant temperature equipment
The heating constant temperature equipment heats the coating liquid to a set temperature through a heating device to ensure that the coating maintains a suitable temperature during the electrophoretic coating process. Usually, the equipment transfers heat to the coating liquid through a heat exchanger or electric heating element to keep its temperature within the optimal range. This type of equipment is particularly important for environments with low temperatures, and can effectively avoid problems such as uneven coating or poor adhesion caused by low temperatures.
2. Cooling constant temperature equipment
When the temperature of the coating liquid is too high, the cooling constant temperature equipment reduces the temperature of the coating liquid through the cooling system to protect the stability of the coating liquid. Common cooling methods include water cooling systems or refrigeration equipment, which reduce the temperature of the coating liquid through heat exchange or circulating water flow to prevent problems such as paint precipitation, excessive particle deposition, or weakened coating adhesion due to excessive temperature.
3. Integrated temperature control system
The integrated temperature control system integrates heating and cooling functions and can automatically adjust the temperature of the coating liquid according to actual needs. These systems are usually equipped with intelligent temperature control equipment, which can monitor the temperature of the coating liquid in real-time and adjust it automatically. Whether it is heating up or cooling down, the system will automatically turn on the corresponding heating or cooling device to ensure that the temperature of the coating liquid remains within the set range, thereby improving the stability of the production process and the coating quality.
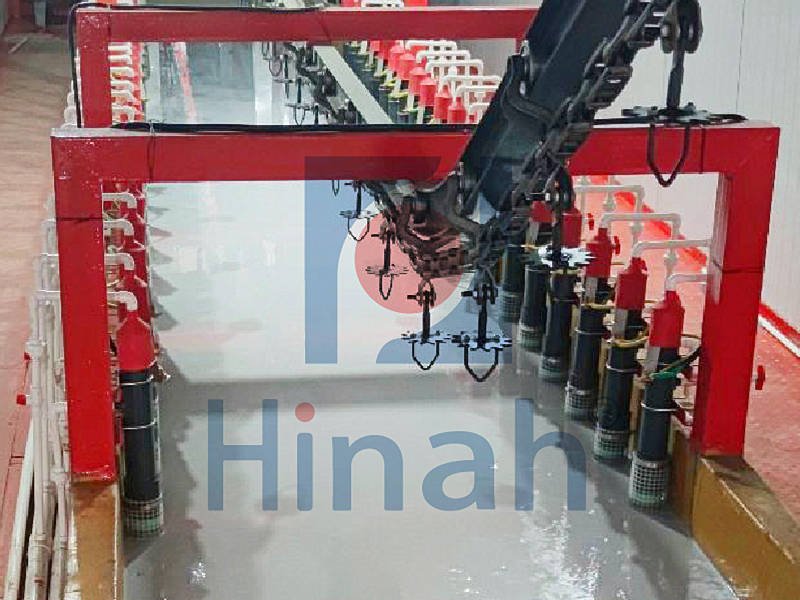
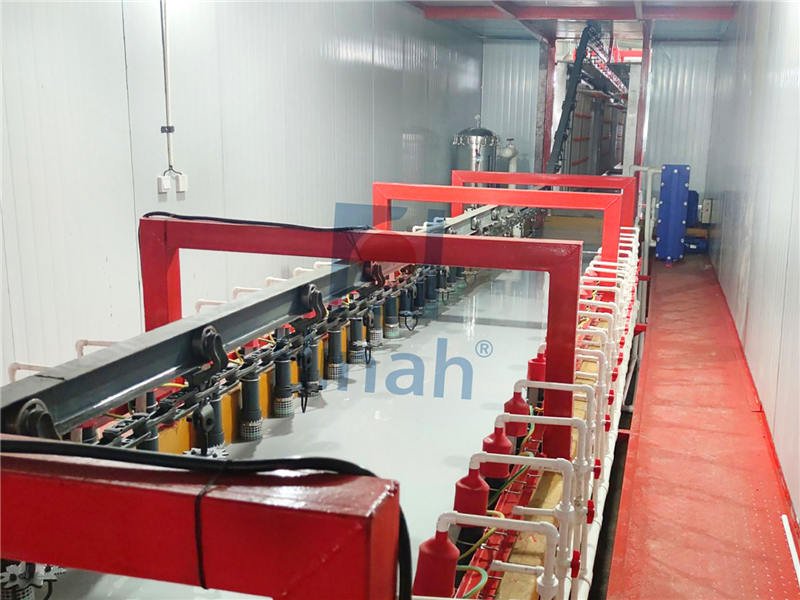
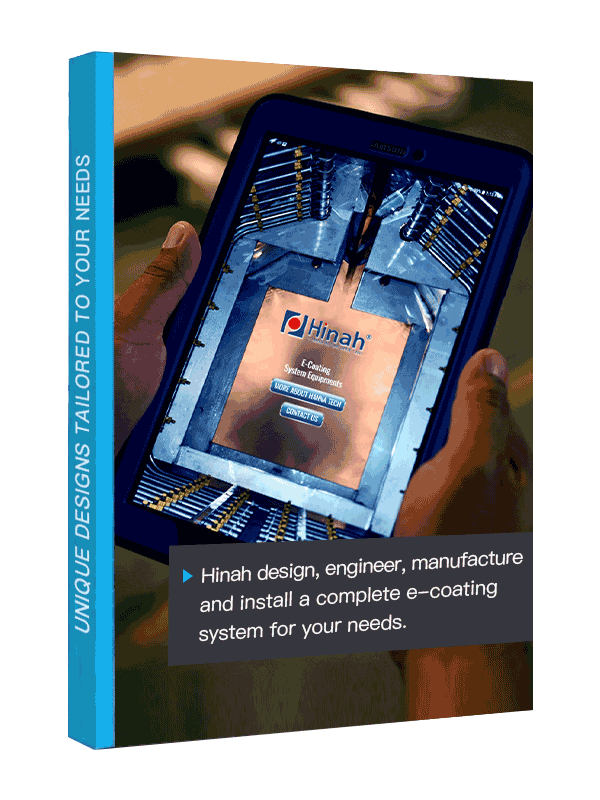
Let's Have A Chat
Get An E-coating Line Planning !
Match Your Products, Get The Solution & Price..
IV.Application of thermostatic equipment in different coating lines
1.Role in monorail e-coating line
In the monorail e-coating line, thermostatic equipment ensures that the temperature of the coating liquid is always in a stable state to avoid the impact of temperature fluctuations on the coating quality. Stable temperature helps maintain uniform deposition of paint particles, thereby ensuring the uniformity and adhesion of the coating. Too high or too low temperature may lead to uneven coating thickness or poor adhesion, so thermostatic equipment plays a key role in temperature regulation in the monorail e-coating line to ensure the quality consistency of the coating.
2.Role in dual-rail e-coating line
During the dual-rail e-coating line, the workpiece usually needs to go through two different electrophoretic stages: cathode electrophoresis and anodic electrophoresis, and each stage has different temperature requirements. Thermostatic equipment can automatically adjust the temperature of the coating liquid according to the requirements of different stages. For example, the cathode electrophoresis stage may require a lower temperature, while the anodic electrophoresis stage may require a slightly higher temperature. By precisely controlling the temperature, the thermostatic equipment ensures that the coating effect of each stage can reach the best state, thereby ensuring the coating quality and efficiency of the dual-rail e-coating line.
3.Impact on the coating of complex or large-sized workpieces
For complex or large-sized workpieces, the temperature control system provided by the thermostatic equipment can meet the special needs of different workpiece coating. The coating liquid volume of large-sized workpieces is large, and the temperature is not easy to be evenly distributed. The thermostatic equipment can ensure the temperature uniformity of the coating liquid through stronger heating and cooling capabilities, thereby avoiding problems such as uneven coating or poor adhesion. In addition, for workpieces with complex shapes, the thermostatic equipment can also maintain the stability of the coating particles in the liquid, ensure uniform and smooth coating, and improve the coating quality of the workpiece.
V.Conclusion
The thermostatic equipment is not only a tool to maintain the temperature stability of the coating liquid in electrophoretic coating, but also a key component to ensure coating quality and production efficiency. They ensure the uniformity, adhesion, and durability of the coating by accurately controlling the temperature of the coating liquid. For every link in the coating line, the thermostatic equipment plays a vital role, thereby helping enterprises to improve production stability and reduce coating defects. In the future, with the continuous advancement of temperature control technology, thermostatic equipment will better serve the electrophoretic coating industry and lay the foundation for a more efficient and environmentally friendly production model.