I. What is electrocoating?
Electrocoating is a coating technology that uses an electric field to uniformly deposit charged particles in the paint onto the surface of a conductive workpiece.
The principle of electrocoating is to use the object to be coated as an electrode (usually a cathode) and immerse it in an aqueous coating solution containing charged paint particles. When direct current is applied, the charged particles in the paint will move under the action of the electric field and deposit on the surface of the workpiece to form a uniform coating film.
There are two main types of electrophoretic coating:
- Anodic Electrophoresis: The workpiece is the anode and the paint is anionic.
- Cathodic Electrophoresis: The workpiece is the cathode and the paint is cationic (currently more widely used).
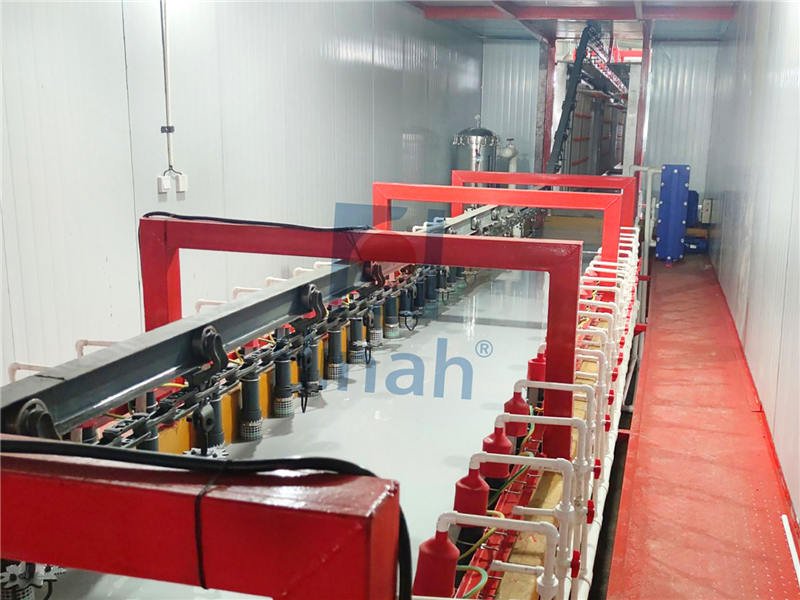
II. What parts does e-coating equipment include?
The main components of e-coating equipment are as follows:
1. E-coat tank
The e-coat tank holds electrophoretic coating solution and is the core component of the electrophoretic process.
2. E-coat power supply system
The e-coat power supply system provides a stable DC power supply to ensure that the charged particles are evenly deposited under the action of the electric field.
3. Stirring device
The stirring device maintains the uniformity of the coating solution and prevents particle precipitation.
4. Filter device
The filter device is used to filter out impurities, keep the coating solution clean, and improve the coating effect.
5. E-coat dosing system
The e-coat dosing system continuously replenishes the electrophoretic tank with paint to ensure the stability of the paint concentration.
These five core devices work together to ensure the efficiency and stability of the e-coating line.
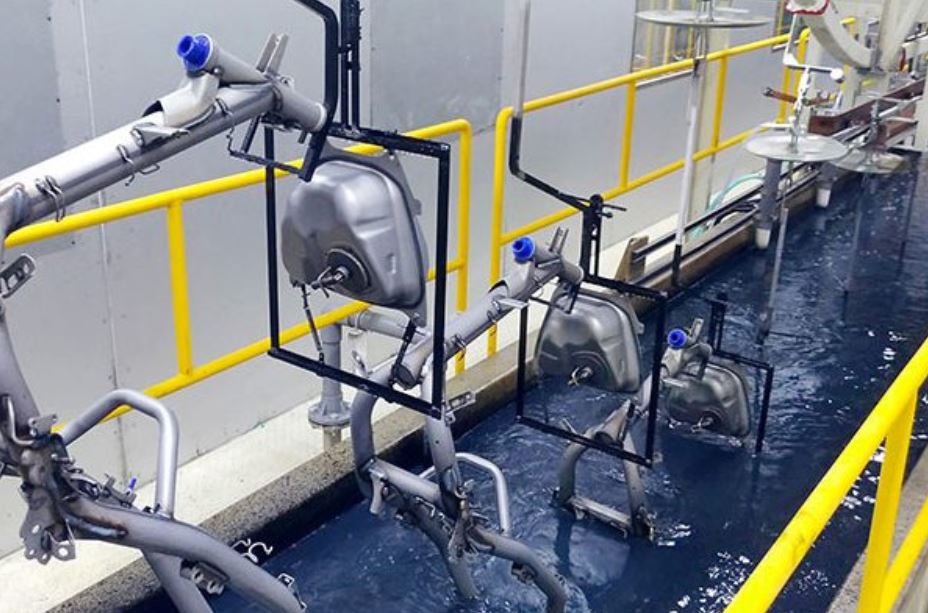
III. What are the advantages of an e-coating line?
1. Strong coating uniformity
Under the action of the electric field, the coating particles can be evenly attached to the surface of the workpiece, and even the parts with complex shapes or depressions can be fully covered.
2. Good coating adhesion
The coating film is firmly bonded to the surface of the workpiece, with excellent peeling resistance and impact resistance, which improves the durability of the product.
3. Excellent anti-corrosion performance
The electrophoretic coating is dense and pinhole-free, effectively preventing the intrusion of water, air, and corrosive substances, and is suitable for scenes with high anti-corrosion requirements.
4. Strong environmental protection
Electrophoretic coating uses water-based paint, with low VOC (volatile organic compound) emissions, reducing environmental pollution, and meeting modern environmental protection requirements.
5. High process stability
The electrophoretic coating line uses automated control equipment, and the coating parameters (such as voltage and temperature) are easy to adjust to ensure the consistency of product quality.
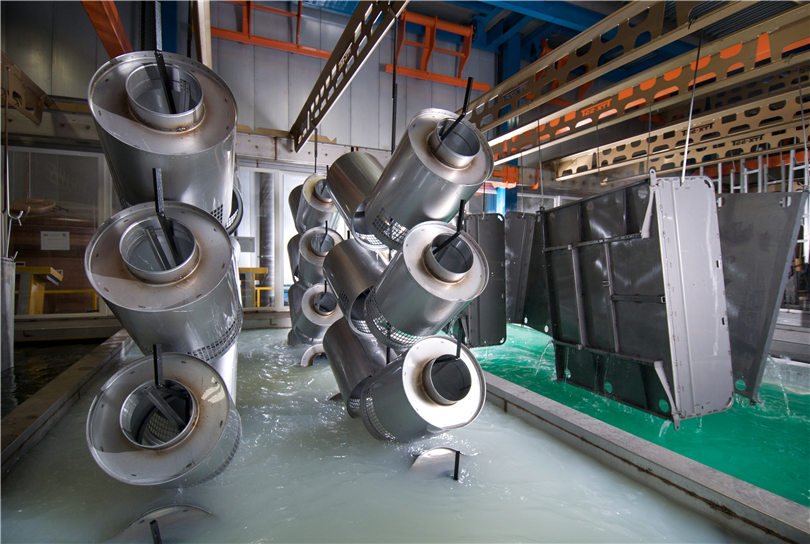
IV. Which workpieces are suitable for e-coating line?
1. Automotive Parts E-coating
Automotive parts are typical application areas for electrophoretic coating. These include large parts such as bodies, chassis, doors, and bumpers, as well as small parts such as brake discs and engine brackets that require high corrosion resistance. Electrophoretic coating can provide reliable protection for these parts and extend their service life.
2. Electric Appliances E-coating
Home appliances are also suitable for electrophoretic coatings, such as the outer shell parts of refrigerators, washing machines, and air conditioners. Through electrophoretic coating, these products not only have a uniform and beautiful appearance but also have a good anti-corrosion effect. In addition, metal brackets and panels inside home appliances are also often electrophoretic coated to improve durability.
3. Industrial and hardware products
In the field of industrial and hardware products, electrophoretic coating is widely used in metal furniture, lamp brackets, industrial equipment housings, guardrails and pipe connectors. These workpieces usually require wear-resistant and corrosion-resistant surface coatings, and electrophoretic technology can efficiently meet these needs.
4. Other complex-shaped workpieces
Electrophoretic coating is particularly suitable for coating complex-shaped workpieces, such as aluminum alloy window frames, irregular parts and small fasteners. Due to their uneven surfaces or special shapes, it is difficult to achieve uniform coating coverage with traditional spraying methods, but electrophoretic coating can easily achieve this.
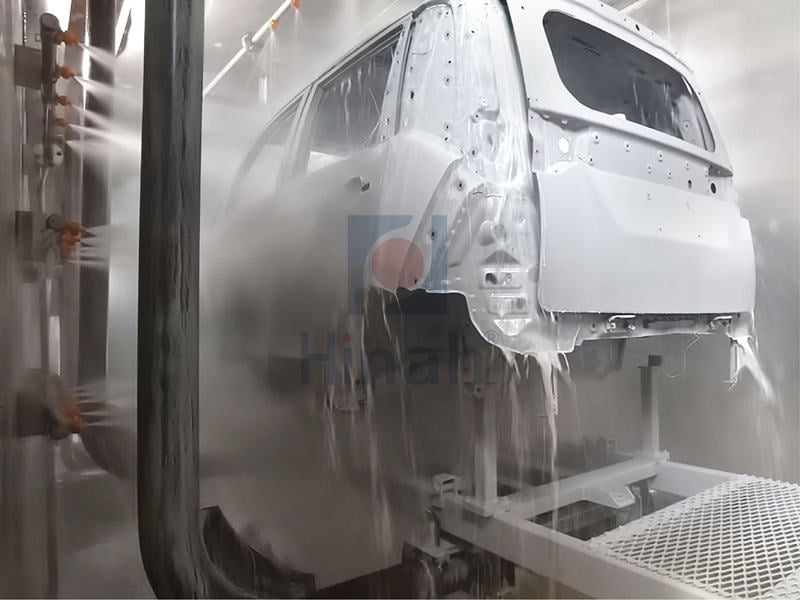
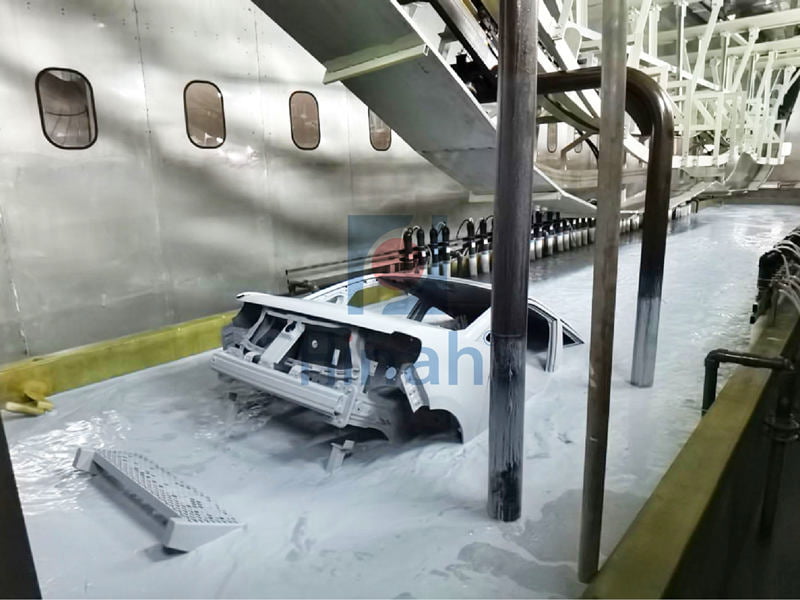
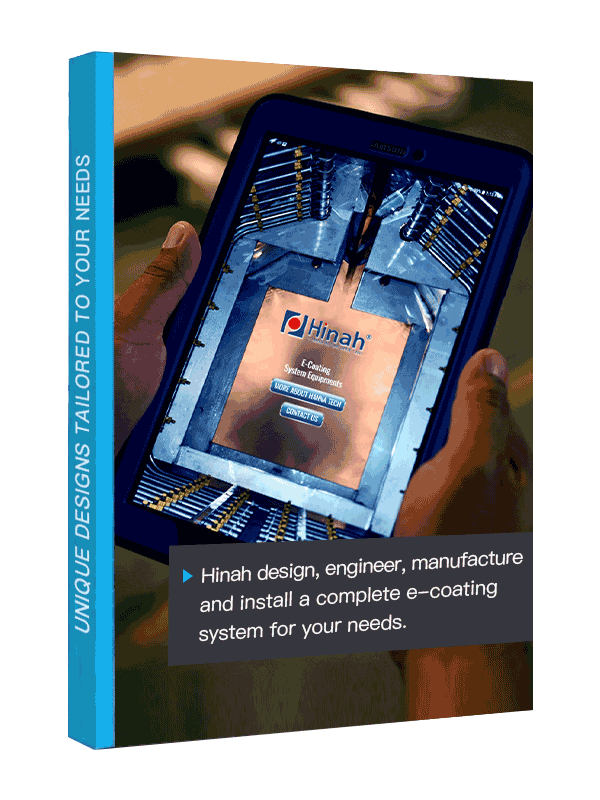
Let's Have A Chat
Get An E-coating Line Planning !
Match Your Products, Get The Solution & Price..
V. Conclusion
The e-coating line has become the preferred solution in the field of metal surface treatment due to its uniform coating, strong adhesion, excellent anti-corrosion performance, environmental protection, and high efficiency. Electrophoretic coating not only meets the high requirements of modern manufacturing industry for product quality and performance, but also conforms to the development trend of environmental protection and energy saving. For enterprises seeking efficient and stable coating processes, electrophoretic coating is undoubtedly an ideal choice.