Electrophoretic coating is a common surface coating process, which is widely used in various industries. In the process of electrophoretic coating, the penetration of electrophoretic paint is one of the key factors affecting the quality of the coating film and the coating effect.
It is very important to understand and control the key factors that affect the swimming power of electrophoretic paint to get a uniform and dense coating film.
In this article, we will introduce several key factors that affect electrophoretic paint penetration.
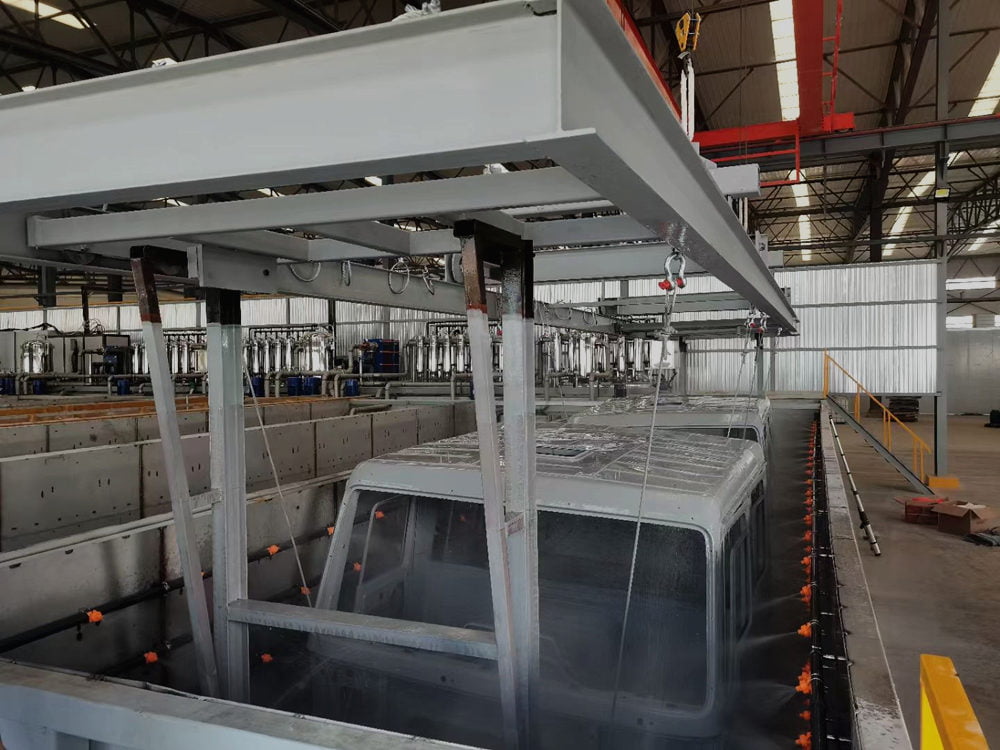
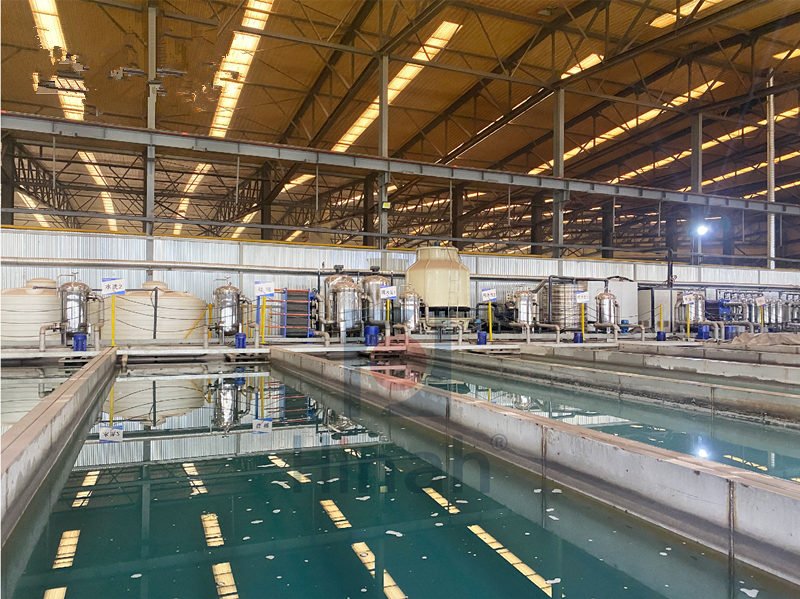
I. Viscosity of electrophoretic paint:
The viscosity of electrophoretic paint refers to the fluidity and viscosity of the paint.
Too high viscosity may cause the paint not to flow easily under the electric field, which affects the uniformity of the coating and the swimming power; while too low viscosity may cause the paint to be lost during the coating process, resulting in waste and uneven coating film.
Therefore, it is crucial to control the viscosity of electrophoretic paint, which can be achieved by adjusting the paint formulation, temperature and the use of thinner.
II. Electric field strength in the electrophoresis bath:
The electric field strength in the electrophoresis bath is one of the important factors affecting the swimming power of the electrophoretic paint.
The electric field strength determines the speed and direction of the electrophoretic paint movement in the electric field.
Too high electric field strength may lead to over-swimming of electrophoretic paint in the coating process, forming thin film or leakage; while too low electric field strength may lead to insufficient coating of electrophoretic paint, forming uneven coating.
Therefore, in the process of electrophoretic coating, reasonable adjustment and control of electric field strength is the key to ensure the swimming power of electrophoretic paint.
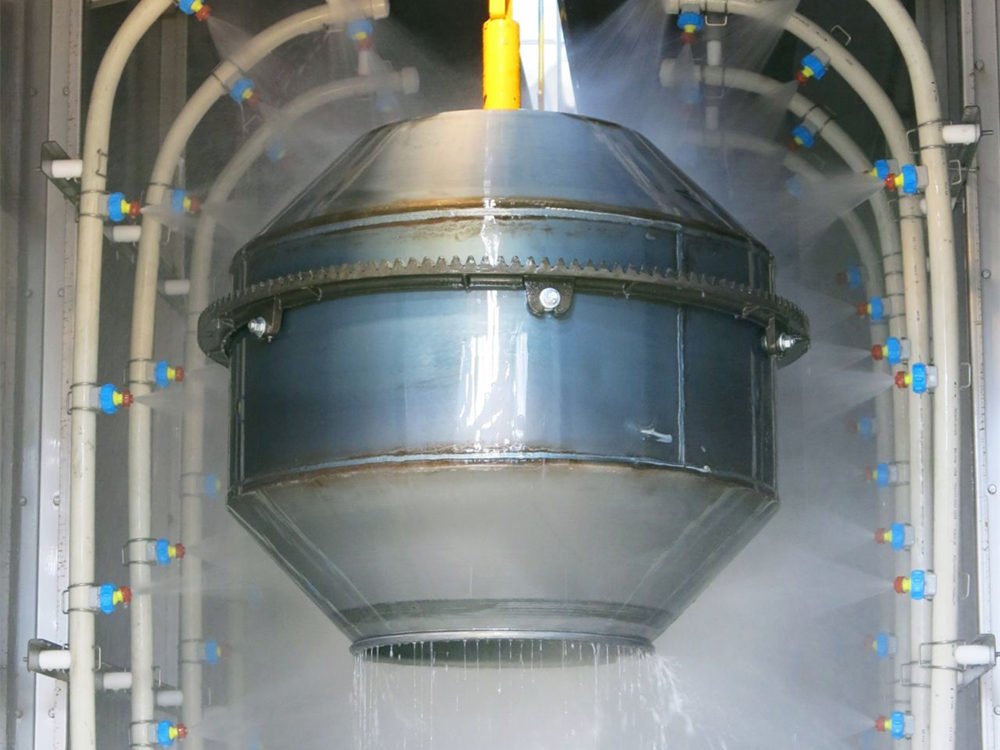
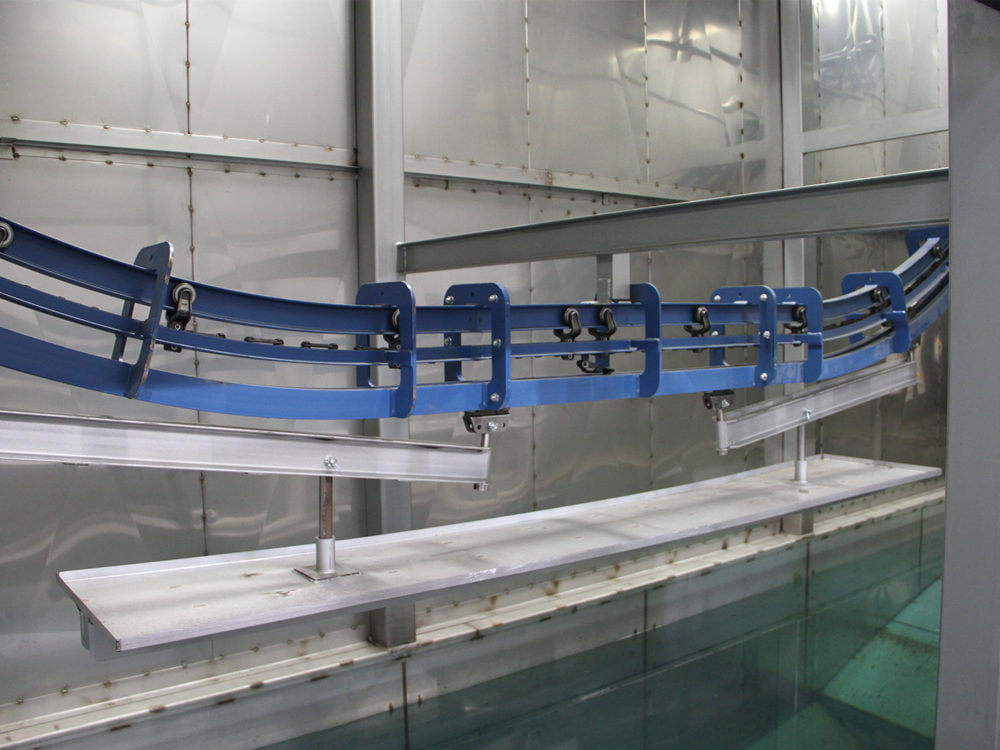
III. Concentration of electrophoretic paint:
The concentration of electrophoretic paint also has an important influence on the quality and swimming power of the coating film.
Too high concentration may lead to over-swelling of electrophoretic paint in the process of coating, forming too thick coating; while too low concentration may lead to insufficient coating of electrophoretic paint, forming uneven coating.
Therefore, the concentration of electrophoretic paint should be accurately controlled before painting to ensure the stability of painting quality.
IV. pH and conductivity of electrophoresis solution:
The pH and conductivity of the electrophoresis solution have some influence on the swimming power of the electrophoresis paint and the quality of the coating film.
Proper pH and conductivity can promote the stable dispersion of electrophoretic paint particles and maintain good paint fluidity and stability of the electrophoretic solution.
Different electrophoretic coating processes and electrophoretic fluid formulations have different requirements on pH and conductivity, so they need to be adjusted and controlled according to specific conditions.
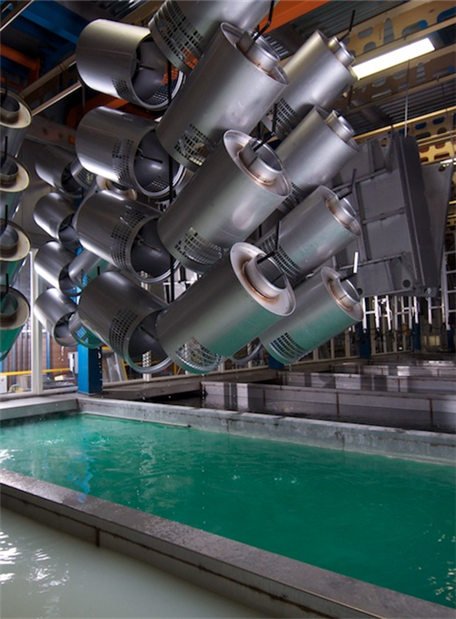
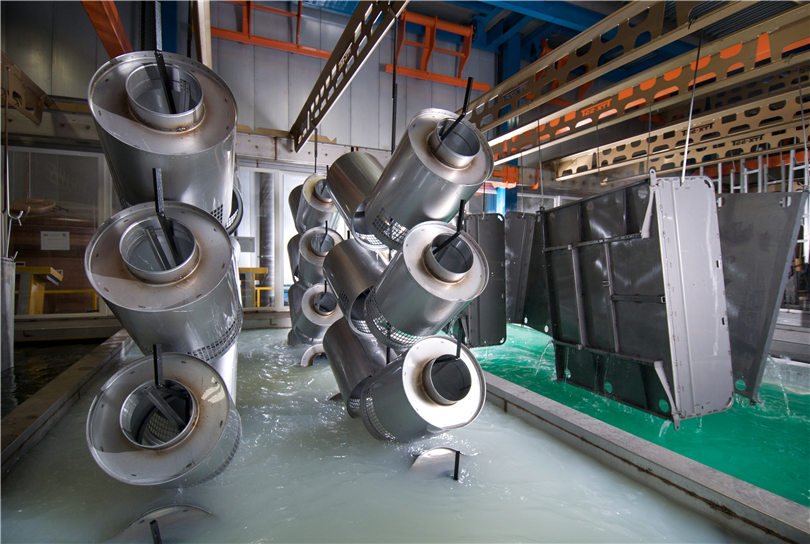
V. Pre-treatment of workpiece surface:
The pretreatment of workpiece surface is one of the important factors affecting electrophoretic paint penetration and coating film adhesion.
Proper pretreatment can remove the surface pollutants and oxidation layer, improve the wettability and adhesion of the workpiece surface, and facilitate the coating and adhesion of electrophoretic paint.
Common pretreatment methods include oil removal, rust removal, phosphating, etc.
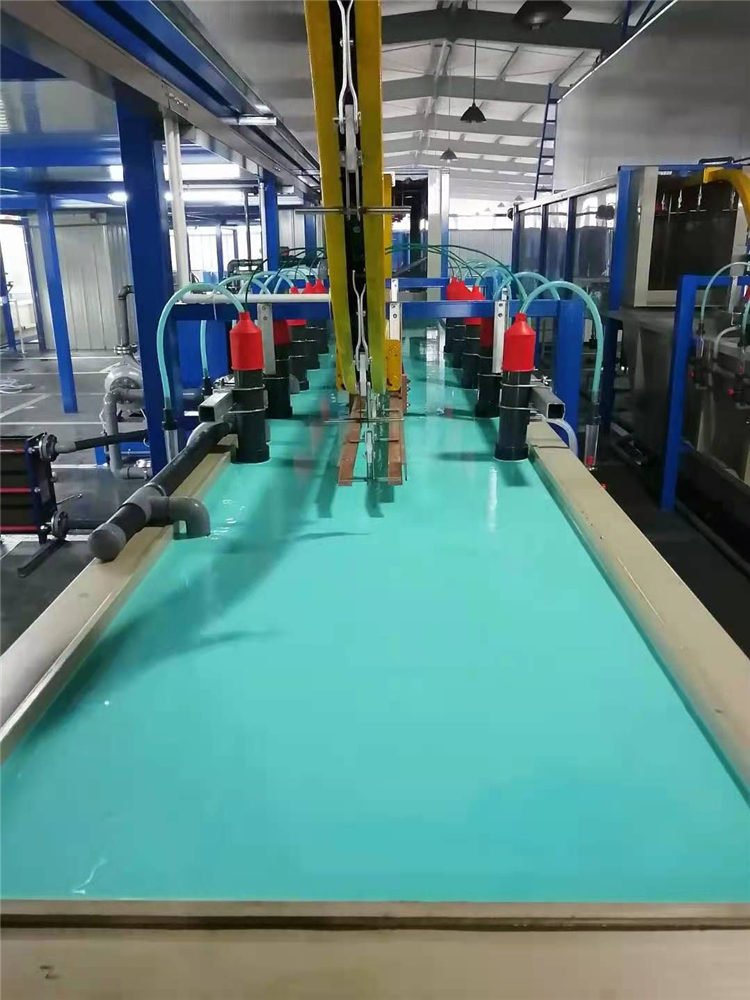
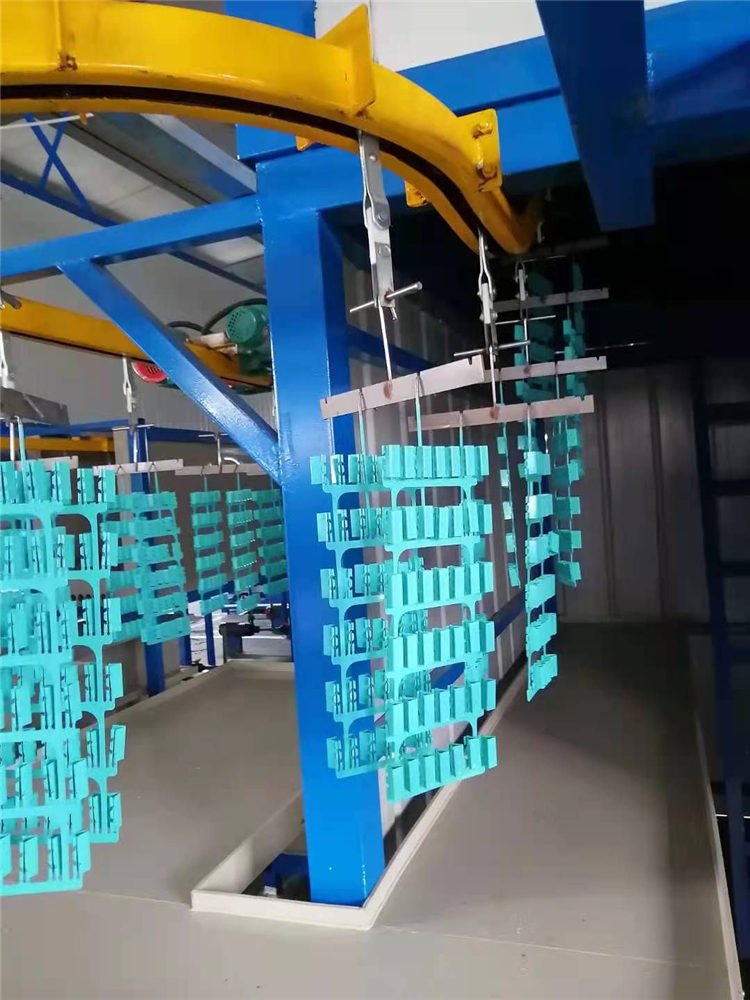
V. Conclusion
To sum up, the key factors affecting the swimming power of electrophoretic paint include viscosity of electrophoretic paint, electric field strength, concentration of electrophoretic paint, pH and conductivity of electrophoretic solution, and pretreatment of workpiece surface.
Reasonable control and adjustment of these key factors can achieve uniform and dense coating film and improve the quality and efficiency of electrophoretic coating.
In practical application, it needs to be adjusted and optimized according to the specific situation to obtain the best coating effect.