Pre-sale Details
With over 30 years of experience in industrial finishing systems, we would be the one to choose when you need to work with a partner who can supply industrial finishing systems for electrophoresis, powder coatings, and liquid painting.
All of Hanna Technology’s coating solutions are customized to meet the needs of our customers. To ensure that customers get exactly what they need, our technical team will help them work through all the details right up to their goal. From initial design to delivery, installation, commissioning, and training, Hanna would take care of it all.
- GOAL: Create value for customers first。
- EXERT CAPABILITY: Unite people and jobs, self-motivation and teamwork.
- SERVICE PRINCIPLE: Help customers succeed! Satisfy customers’ needs in all aspects!
The company has excellent technology and a strict, perfect quality management system, 30+ years of experience in the industry, and gathered professional technical engineers, and a first-class research and development team. We make full use of new materials to ensure the stability and reliability of equipment.
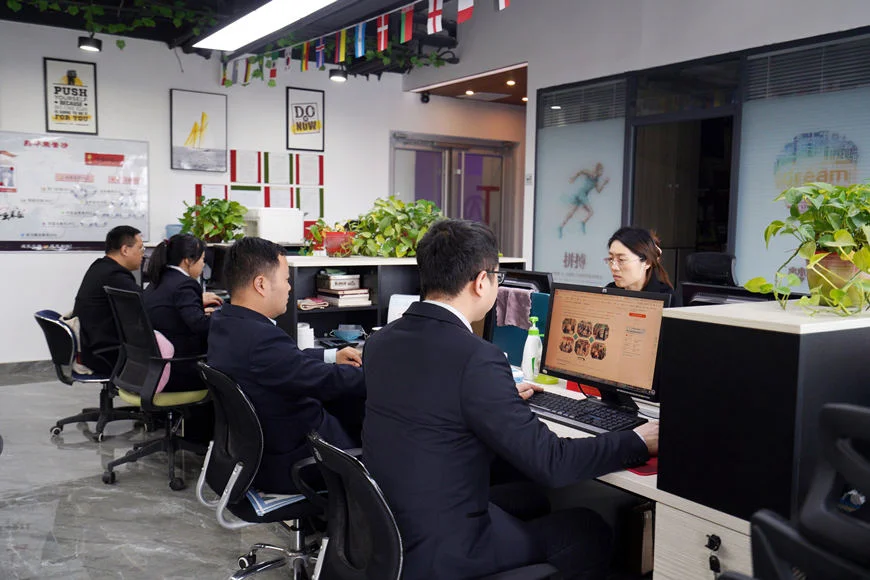
Team information
Never compromise on design safety, integrity, efficiency, and reliability, provide reasonable design, and never sell our customers more than what they need.
Never stop trying to perfect our solutions. Besides, we can offer you an additional maintenance agreement containing regular service check-ups to avoid costly stops and breakdowns.
Focus on design & solutions
Hinah provides clients with the most complete and reliable electrodeposition coating line with:
- Excellent coating quality, high precision, and high durability.
- Reasonable design plan, saving production cost.
- Easy-to-use design details offer a higher production efficiency.
- Environmental protection and energy saving.
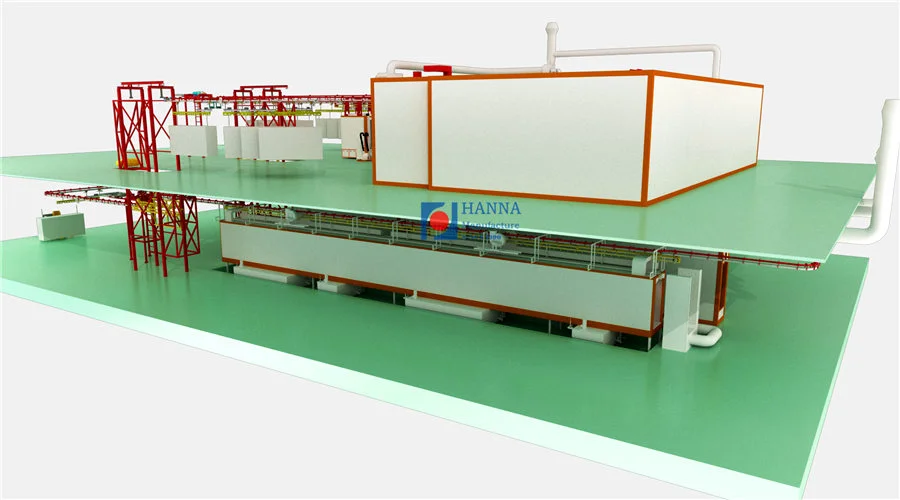
Inquiry and quotation
The customer’s message will be answered within 24 hours.
You can ask Hinah about specifications, performance, price, delivery time, etc., and learn about Hinah’s electrodeposition coating line, and you can request catalogs, technical parameters, quotations, etc.
Hinah will provide graphic design drawings and overall solutions according to the client’s needs, and mutually determine the solution that matches the customer’s needs.
Design solution
Hinah’s technical team will provide a very detailed design plan of the electrodeposition coating line according to the details of the client’s needs, including a layout plan, process flow diagram, equipment list, equipment parameters, equipment price, etc.
And take into account the workpiece type, size, quantity, quality requirements, factory space, environment, energy, and other factors to ensure the reasonableness, high efficiency, and energy saving of the plan. After the customer reviews and agrees to the solution, both parties agree and sign the sales contract.
Documents Download
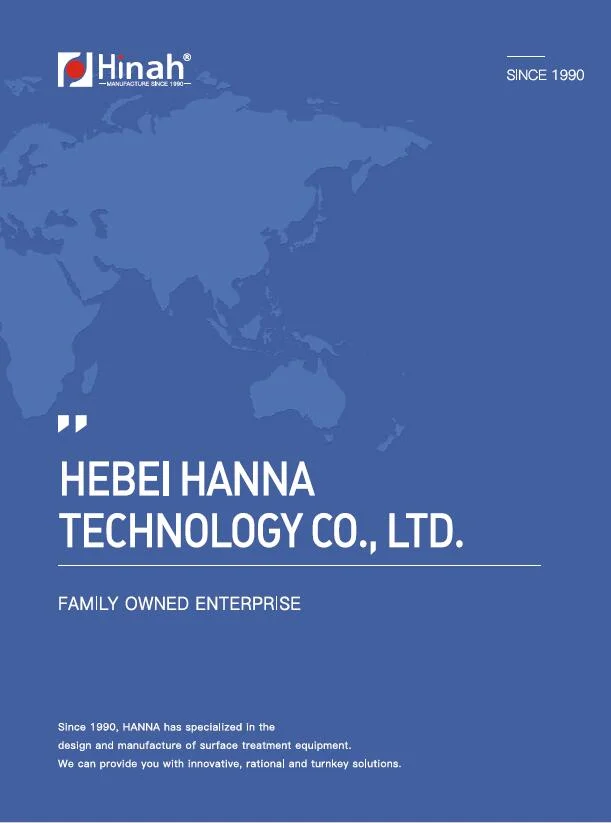
Hanna Company Profile
- Thirty years of production and design experience in shot blasting.
- Equipment gets the international certification: CE, ISO14001, ISO9001, TUV, BV.
- Get a government-granted endorsement of trust. ATHI is trustworthy.
- All designs adopt 3D Design.
- OEM&ODM factory, High-quality after-sales service
- All adopt general parts, easy to buy and replace.
- Domestic certificate: AAA corporate certificate (The first AAA enterprise in Qingdao).
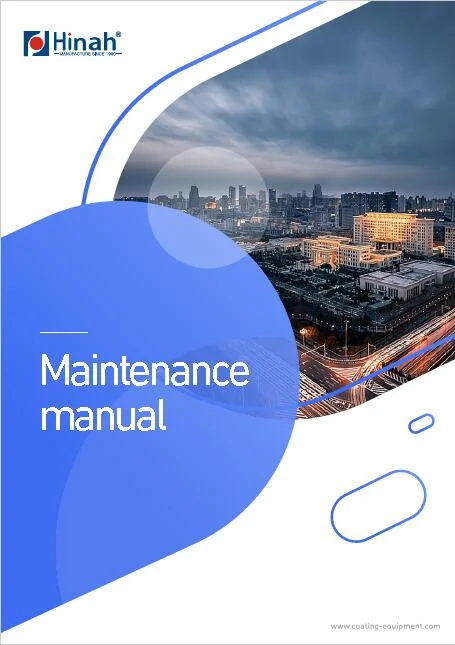
E-coating maintenance manual
- Thirty years of production and design experience in shot blasting.
- Equipment gets the international certification: CE, ISO14001, ISO9001, TUV, BV.
- Get a government-granted endorsement of trust. ATHI is trustworthy.
- All designs adopt 3D Design.
- OEM&ODM factory, High-quality after-sales service
- All adopt general parts, easy to buy and replace.
- Domestic certificate: AAA corporate certificate (The first AAA enterprise in Qingdao).
Need a design plan, now?
Loading & Shipping
Packaging and shipping are an important part of the export business, which ensures that our previous efforts are not lost.
A good packaging and shipping solution is very practical and safe.
- It ensures the safety and integrity of the equipment, without damaging or leaving parts behind.
- It cuts expenses and costs for the customer, resulting in a more economical input solution.
- It makes the shipping process, such as loading and unloading, smoother and ensures a smooth implementation without delays.
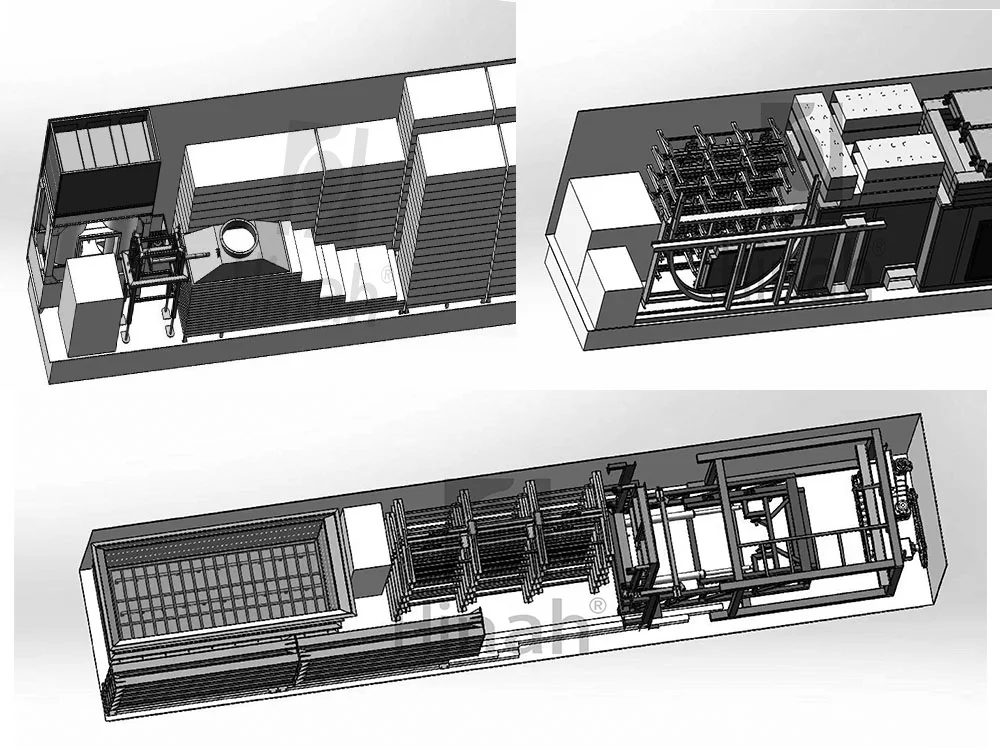
3D Pre-loading solutions
Based on our export experience, we can design the crating solution according to the equipment, from design to manufacturing, transportation, and installation.
Compact packing solutions can reduce the freight cost, which is a very important way to reduce the cost.
At the same time, good packaging and protection of the equipment can avoid or reduce the damage or surface scratches caused by transportation.
Perfect packaging
We have made proper arrangements for packing materials and methods. The use of thick cartons or wooden boxes, foam, crash pads, corner guards, and other materials can improve the safety of the cargo.
Through our pre-assembled model simulation, we can make the most cost-effective choice of container type.
Reasonable distribution of cargo weight and space, to avoid uneven weight distribution, while reducing the difficulty of unloading and picking up the goods.
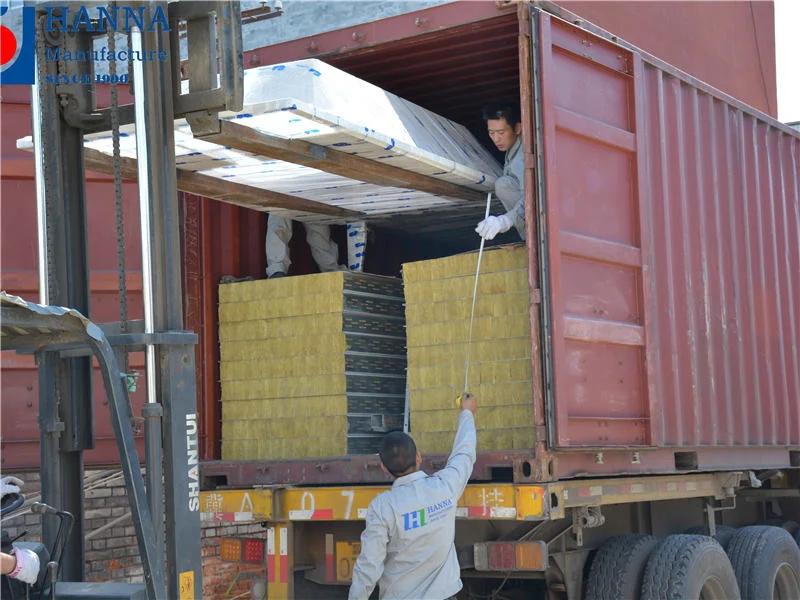
Ocean transportation is a common mode of equipment transportation, especially for large equipment or transportation across oceans, and it offers the advantages of efficiency, economy, and reliability. However, ocean transportation also involves several considerations and critical points to ensure the safe and smooth delivery of equipment. The following are some of the important things to consider when shipping by sea:
- Packaging and securing: Challenges faced by equipment in marine transportation include waves, wind, and bumps. Therefore, equipment must be properly packaged and secured to prevent damage or tilting during transport. Use appropriate packing materials and cushioning materials, and use solid lashing and securing equipment to ensure that the equipment can withstand the conditions of transport.
- Transportation method selection: Choosing the appropriate transportation method for the equipment is critical. Depending on factors such as the size, weight, and destination of the equipment, a container ship, bulk carrier or dedicated vessel can be selected. Proper choice of transportation mode can minimize transportation costs and ensure the safety of the equipment.
- Contract of carriage and insurance: it is very important to ensure that a detailed contract of carriage is signed with the carrier before carrying out sea transportation. The contract should agree on the matters of liability, insurance responsibility, compensation, and claims. At the same time, the purchase of proper cargo transportation insurance can provide necessary protection in case of accidents.
- Route and port selection: Choosing the right route and port is the key to ensuring the timely arrival of equipment at the destination. Consider factors such as transit time, traffic conditions, port facilities, and service quality to choose the best route and port to minimize delays and uncertainty.
- Safety and compliance: It is important to ensure that equipment meets relevant safety standards and regulatory requirements. In international maritime transportation, International Maritime Organization (IMO) regulations and conventions must be followed. Equipment must be inspected and certified and have the necessary safety equipment and markings.
- Loading and unloading operations: Equipment is easily damaged during loading and unloading, so special attention should be paid to the safety of loading and unloading operations. Reasonable arrangements for lifting equipment, use of professional loading and unloading teams, and appropriate protective measures, such as the use of lifting devices and protective materials, to prevent damage to equipment in the loading and unloading process.
Learn more about the details ?
Installation guidance
Installing electrophoresis coating line equipment is a complex process that requires careful planning and specialized technical knowledge. The following are some general guidelines for installing electrophoresis coating line equipment:
- Create a construction plan: Before installing electrophoresis coating line equipment, it is critical to create a detailed construction plan. This plan should include consideration of equipment layout, workflow, required resources, and schedule. Ensure adequate communication and coordination of efforts with the supplier and installation team.
- Equipment layout design: Based on the space and process requirements of the plant, carry out equipment layout design. Consider the flow sequence of the painting line and rationalize the location of each part to achieve an efficient production process. Make sure there is enough spacing and access between equipment for easy operation and maintenance.
- Foundation and support structure: Electrophoresis coating line equipment needs a strong foundation and support structure to ensure stability and safety. Design and construct the foundation and support structure according to the equipment specifications and requirements provided by the supplier. Make sure the foundation and support structure meet the specifications and can withstand the weight and vibration of the equipment.
- Power and gas supply systems: Electrophoretic coating line equipment usually requires a large amount of power and gas supply. Ensure that the power and gas supply systems meet the needs of the equipment and comply with safety standards. Coordinate with suppliers and relevant departments to ensure that the equipment is properly connected to the power and gas supply to ensure proper operation.
- Piping and piping layout: Electrophoretic coating line equipment requires liquid delivery systems, including water, paint, and cleaning agents. Properly design and lay out piping and piping to ensure smooth flow of liquids and avoid leakage and pressure loss. Use appropriate pipes and connections, and conduct rigorous inspection and testing to ensure the reliability and safety of the piping system.
- Control systems and automation: Electrophoresis coating line equipment is usually equipped with control systems and automation equipment to monitor and control the production process. Install and commission the control system to ensure it matches the proper operation of the equipment, and perform the necessary programming and commissioning. Ensure that the operator is familiar with the operation and maintenance of the control system.
- Safety features and precautions: When installing the electrodeposition line equipment, ensure that the necessary safety features and precautions are installed. It is very important to ensure that the necessary safety features and precautions are installed. These include emergency stop buttons, safety gates, guardrails, warning signs, and emergency evacuation routes. Ensure that the installation meets the relevant safety standards and conduct the necessary training to raise the safety awareness of operators and staff.
- Testing and commissioning: After completing the installation of the equipment, carry out the necessary testing and commissioning work. This includes electrical system testing, piping system testing, control system testing, and functional verification of the equipment. Ensure that equipment is thoroughly checked and adjusted before operation to ensure it is working properly and performing as expected.
- Training and documentation: After the equipment is installed, conduct operator and maintenance personnel training to ensure they are familiar with the operation and routine maintenance of the equipment. Also, establish a comprehensive documentation system, including technical specifications of the equipment, installation records, operation manuals, and maintenance logs. This will help in the management and maintenance of the equipment and provide necessary reference materials.
- Monitoring and maintenance: After the installation is completed, regular monitoring and maintenance of the equipment is necessary. Regularly check the operating status of the equipment, fluid supply, electrical system, and control system to ensure that the equipment remains in good working condition and performance. Timely handling of equipment malfunctions and abnormalities and preventive maintenance are performed to extend the equipment’s service life and ensure the continuity of production.
Installation guidance
- Detailed installation manual.
- Installation instructors.
- Installation site guidance.
- Remote support.
- Training and training materials.
- After-sales support.
Equipment Maintenance
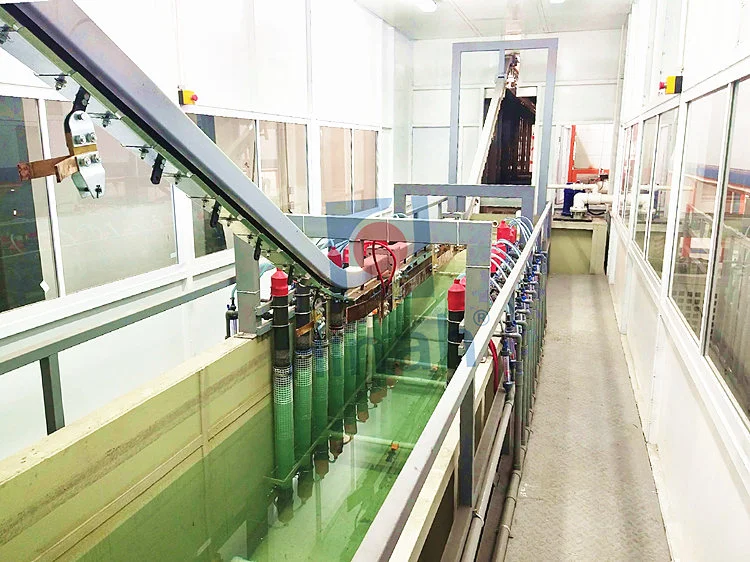
Regular cleaning and maintenance
Regular cleaning includes cleaning equipment components such as coating tanks, spray systems, filters, and piping to remove adherents and dirt.
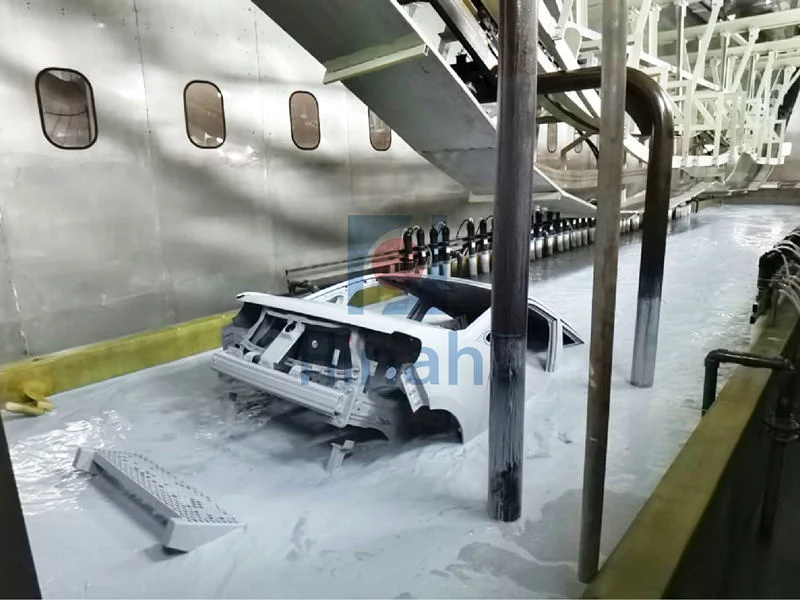
Monitoring and adjusting coating parameters
The coating parameters of the electrodeposition coating equipment are critical to the quality and performance of the coating.
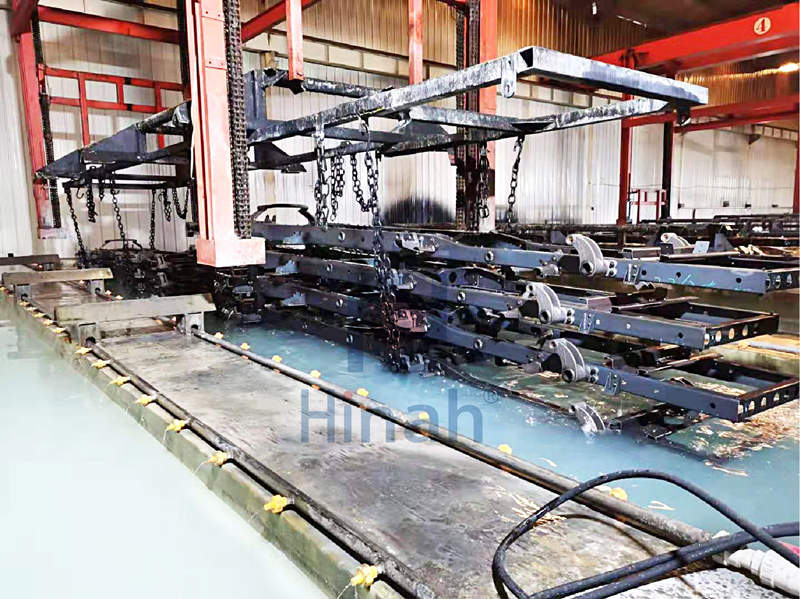
Regular inspection and maintenance of equipment
Regular inspection of various parts and systems of the equipment is the key to preventing failures and problems.
Maintenance of electrophoretic coating equipment is essential to ensure long-term stable operation and improve production efficiency. The following are three key points for the maintenance of electrophoretic coating equipment:
- Regular cleaning and maintenance: Regular cleaning is one of the key steps in maintaining electrophoretic coating equipment. This includes cleaning equipment components such as coating tanks, spray systems, filters, and piping to remove adherents and dirt. It also involves inspecting and replacing damaged or aged parts such as seals, nozzles, and filters. Regular maintenance of equipment, such as lubricating moving parts and adjusting equipment for proper operation, can prevent breakdowns and extend the life of the equipment.
- Monitoring and adjusting coating parameters: The coating parameters of the electrodeposition coating equipment are critical to the quality and performance of the coating. Regular monitoring and adjustment of coating parameters, such as voltage, current, coating time, and paint concentration, can ensure consistency and stability of coating quality. According to the coating effect and product requirements, adjust the parameters in time to optimize the coating process and maintain the uniformity and adhesion of the coating.
- Regular inspection and maintenance of equipment: Regular inspection of various parts and systems of the equipment, as well as key electrical and control systems, is the key to preventing failures and problems. Check the equipment’s electrical connections, valves, pumps, drive systems, and sensors to ensure proper operation and safety. Repair and replace any problems found promptly to avoid equipment downtime and production interruptions.
- In summary, regular cleaning and maintenance, monitoring and adjusting coating parameters, and regular inspection and repair of equipment are the three key points of electrodeposition coating equipment maintenance. Through reasonable maintenance measures, the reliability of the equipment can be improved, the service life extended, and the stability and consistency of the coating quality ensured.
Need an electrophoresis line planning?
After-sales Service
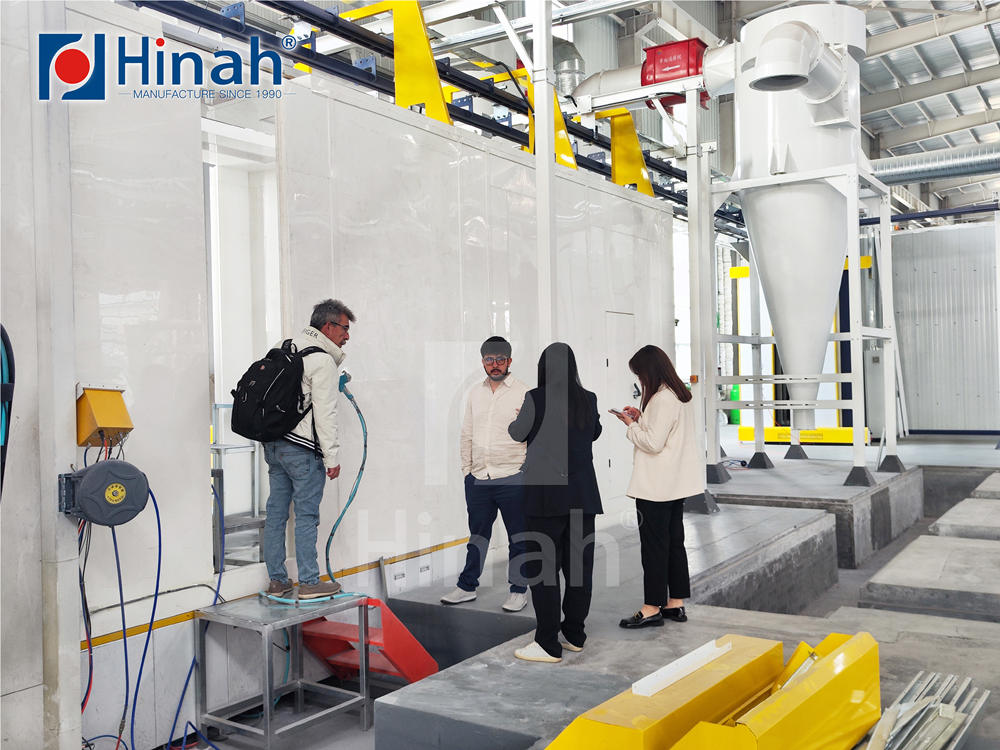
After-sales technical support
Timely and professional technical support. This includes equipment operation guidance, troubleshooting, maintenance advice, and technical consultation. Suppliers should provide a variety of communication channels, such as telephone support, online support, and on-site support, to help customers solve problems encountered during the use of the equipment.
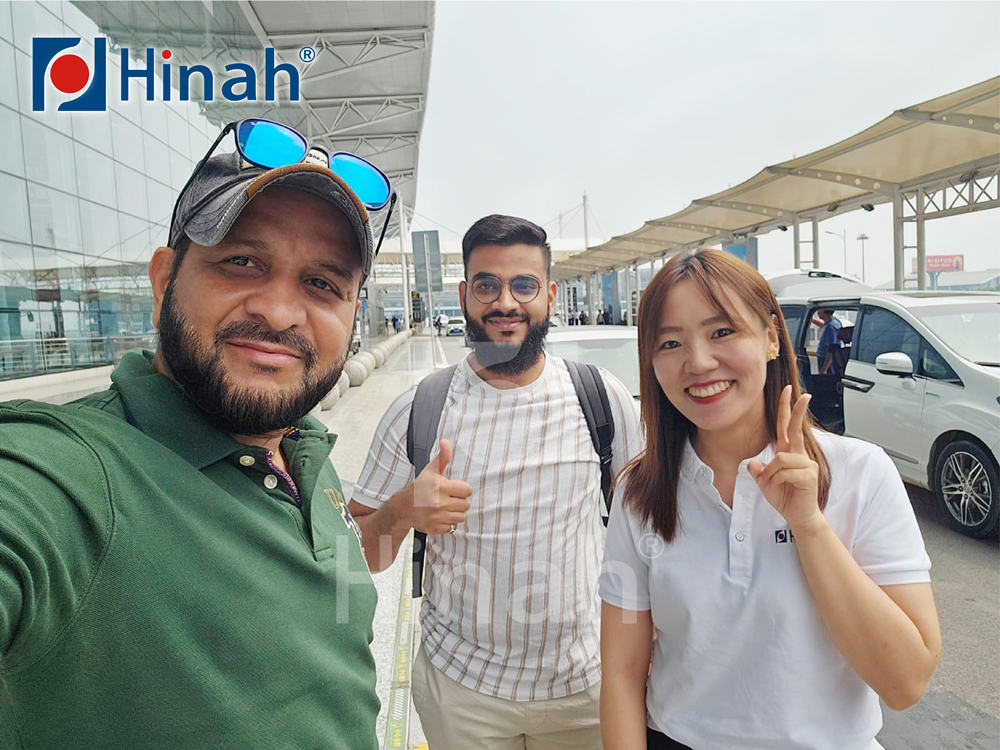
Quick response and maintenance
Respond quickly when equipment failures occur and provide timely maintenance services. Suppliers should establish a sound after-sales service system to ensure that they can dispatch maintenance personnel to the customer’s site promptly to carry out repairs. Quick response and repair will reduce production downtime and improve the customer’s productivity.
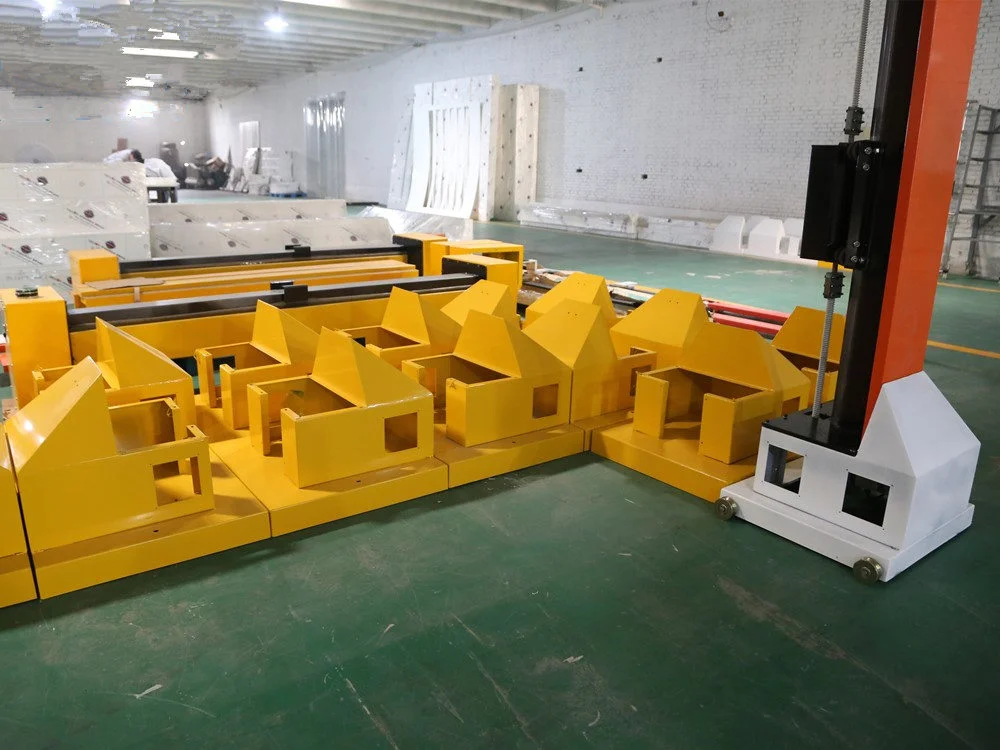
Equipment spare parts supply
Original spare parts supply and support. The quality and adaptability of original spare parts are more guaranteed and can ensure the normal operation and performance of the equipment. The supplier should establish a perfect spare parts management system to ensure the timely and reliable supply of spare parts, and provide the spare parts list and ordering channels to the customer.
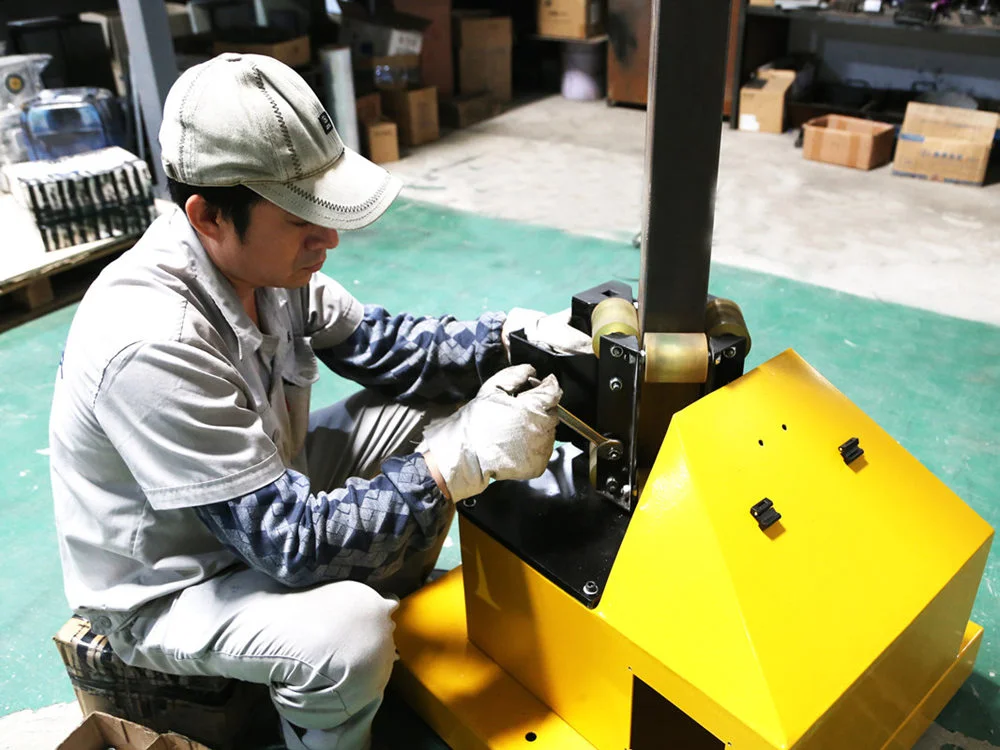
Regular maintenance and servicing
Regular equipment maintenance and servicing services. Regular maintenance can prevent equipment failures and problems and keep the normal operation and stable performance of the equipment. The supplier should make a maintenance plan and dispatch technicians regularly for equipment inspection, cleaning, lubrication, and adjustment to ensure the good condition and best performance of the equipment.
Need an electrophoresis line planning?
FAQ
Yes, our electrophoretic coating equipment meets the industry standards and certification requirements. Our equipment has undergone strict quality control and testing to obtain relevant certifications, such as ISO certification, CE certification, etc. We ensure that the quality and performance of our equipment can meet your needs.
Answer: Yes, we can customize the equipment according to your coating process requirements. We have a team of professional engineers and experienced technicians who can work with you to ensure that the configuration and parameters of the equipment will meet your specific requirements. We will provide detailed technical solutions and process flows and ensure that the equipment will achieve the coating results you need.
Answer: Yes, our electrodeposition coating equipment is high performance and energy efficient. We use advanced technology and design to optimize the energy efficiency of our equipment and reduce energy consumption. We also offer advanced automatic control systems for precise control of the coating process and reduced paint waste. With our equipment, you can get high efficiency and environmentally friendly coating results.
Answer: Yes, we provide comprehensive after-sales service and maintenance support. We have professional after-sales team and technicians who can provide services such as installation and commissioning, operation training, troubleshooting and repair of the equipment. We also provide the supply and replacement of equipment spare parts to ensure the normal operation and long-term reliability of the equipment. We will establish a long-term relationship with you to ensure that you receive timely and professional support during the use of your equipment.
Answer: Yes, we have a wealth of successful cases and testimonials from satisfied customers. We have worked with many industry leading customers and provided them with high quality electrodeposition coating equipment and services. We can show you our case studies and customer testimonials to prove our competence and professionalism.
Answer: Yes, our electrodeposition coating equipment has good safety performance and complies with the relevant safety standards. We adopt advanced safety design and protection measures to ensure the safety of the equipment during operation. Our equipment has undergone rigorous safety testing and certification and complies with international safety standards to ensure the safety and security of our customers.
Answer: Yes, we have the ability and flexibility to customize our equipment. We understand that each customer’s needs are unique, so we can customize equipment to meet your specific requirements. Whether it’s equipment specifications, functional configuration or design, we can work with you to customize the equipment to meet your specific needs. Our team of engineers has extensive experience in customization and will provide you with expert technical support.
Answer: Yes, our equipment is highly reliable and stable. We select high quality materials and components and ensure the stability and long-term reliability of our equipment through strict quality control and testing processes. We also perform comprehensive equipment testing and validation to ensure stable operation under a wide range of operating conditions, and provide appropriate warranty and maintenance support.
A: Yes, our equipment is scalable and upgradable. We design our equipment with scalability in mind, taking into account the future growth and changing needs of our customers. Our equipment has a modular design and flexible configuration options that allow for upgrades and expansions based on customer needs. This allows customers to easily upgrade their equipment to increase production capacity and efficiency as their business grows.
Answer: Yes, we are committed to technological innovation and providing advanced coating solutions. We continually monitor the latest technologies and trends in the industry and are constantly improving our equipment and processes. Our team of engineers has the technical knowledge and experience to provide our customers with innovative coating
Complaints & Feedback
We are pleased to receive your feedback, which helps us to improve our work. Hanna is always committed to providing reliable products and proper services to our customers.
Your valuable comments will be valued and will be handled by our direct manager and responded to within 24 hours (working days).
We have set up a special feedback mailbox, which will be read and processed by our direct manager. Your feedback will have a very positive impact on our product design, production and service processes. Thank you for your attention to Hanna products, Hanna will face the problems and difficulties, improve the products and services to satisfy our customers. Hanna has always been committed to providing customers with reliable products and appropriate services, which is Hannah’s pursuit and goal.
- Please indicate your valid contact information.
- We recommend that you download the feedback form and write your answers.
- Finally send it to our e-mail address for handling feedback and complaints.
- Our feedback email: fdback@coating-equipment.com
Thank you for your patience, we’ll get back to you as soon as we receive the email and get back to you within 24 hours (working days).
1,Your feedback problems are categorized into
①product problems ②service attitude ③delivery delay ④installation operation ⑤after-sales service
2, The product you purchased and the date is?
3,You contacted the business manager is?
4,What is the situation and problem you encountered?
5,Your contact information (name/email/WhatsApp/phone number)
6, Attachment
Search Form
/WHO IS SERVING
Our outstanding Employees
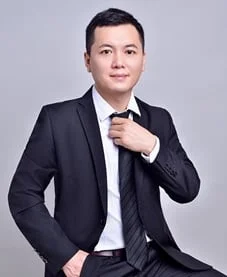
- Project number, item description and pictures.
- +86 150 8119 5156 ( WeChat / WhatsApp )
- sales06@coating-equipment.com
General terms and Conditions – Spare parts, components and accessory equipment If you need spare parts and do not find a service team near you, please call us on
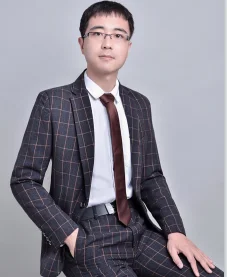
- Project number, item description and pictures.
- +86 186 3304 5156 ( WeChat / WhatsApp )
- sales05@coating-equipment.com
Since the purchase of the e-coating line leaves the question of preventive service open, we can offer you a wide range of customized service and maintenance solutions and are able to tailor make an agreement suited for you.
On the premise of meeting customer requirements and ensuring quality, the Technical Review Committee, together with the sub-designers, reasonably determines and divides the stages of design, production, installation and commissioning, and formulates detailed progress plans for each stage.
In the early stage of design, the company’s technical evaluation committee will review the painting line and non-standard products, so that the designed products strictly comply with the requirements of national painting equipment and the actual needs of customers.
Design input: collect customer original data in detail, formulate design rules, and determine the design standards and specifications of the project by the sub-engineers;
Design output: ensure the output quality of the design, and the output of the design completely meets the design input requirements.
Design review: Design rules and scheme design must be reviewed by technical review committee, and construction drawing design should be reviewed by technical review committee.
Design verification: ensure that each drawing is passed two inspection and two validation.
Design confirmation: design plan and construction drawing design must be examined and confirmed by customer.
Documentation and data control: The relevant professional engineers ensure that the standards and specifications used by each profession are the latest and effective versions;
Strictly abide by our company’s validation system, construction drawings must be approved and signed by the Technical Review Committee before they can be deliver goods
Strictly abide by our company’s signing system, all design changes must be notified to the relevant sub-engineers to make corresponding changes;
All finished drawings must be filed in time according to the requirements of our company.
Strengthen the quality assurance system and quality protection measures of equipment manufacturing department. Our company is specially equipped with quality inspectors to strictly control product processing quality.
All purchasing requirements put forward by our company must go through the project and be approved and signed by the project manager before they can be implemented.
/SERVICE CASE
Provide customers with all -round service
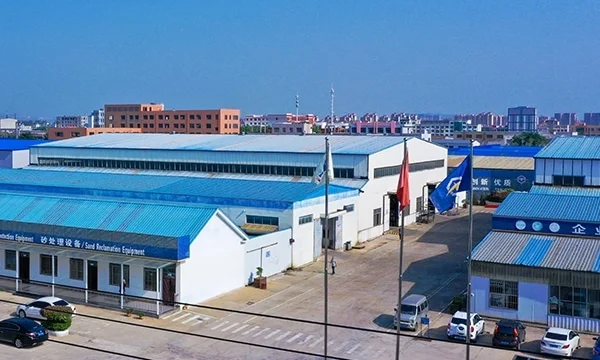
Adhering to the concept of integrity, ATHI will continue to be a trustworthy group
considers a sound reputation the foundation of business and recognizes that integrity is the prerequisite for maintaining our reputation …
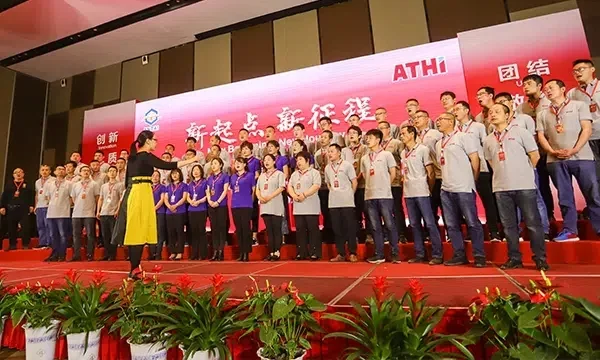
Respects all employees’ rights and provides humanistic care
Respects all employees’ autonomy and creativity and supports their self-development. We provide all employees with an equal opportunity to …
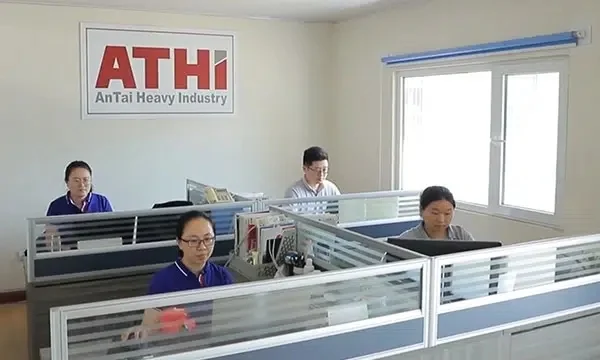
Provides Adequate After-sales Service and Support
Aims to improve product quality and strengthen comprehensive after-sales service. As an excellent manufacturer of surface cleaning and casting …